Практический результат работ по переходу к обслуживанию оборудования по техническому состоянию на предприятии ООО "Томскнефтехим"
Всегда интересно ознакомиться с результатами работы коллег других предприятий. Посмотреть с какими проблемами сталкиваются, какие задачи им приходится решать. К сожалению, в области технической диагностики специалисты не спешат делиться своим опытом и знаниями. Поэтому, с особой благодарностью к коллегам из Томскнефтехима, предлагаю взглянуть на примеры из их практической деятельности.
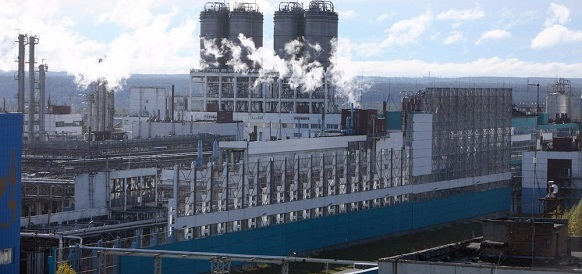
Введение
Надежная работа основного и вспомогательного оборудования в настоящее время не представляется возможной без периодического виброконтроля и вибродиагностирования его состояния. Основные дефекты деталей, узлов возникают в процессе эксплуатации и ремонта оборудования. Одни дефекты – такие как естественный физический износ – объективны, но многие дефекты – «рукотворные» и являются чей-то недоработкой как при ремонте, так и при эксплуатации, и при изготовлении и входном контроле.
Мы в Томске стараемся изучать и систематизировать причины повышенной вибрации оборудования, чтобы понять истинную обстановку, сложившуюся с нашим
динамическим оборудованием. Анализ основных дефектов, выявленных при диагностике оборудования в течение 2011г., представлен на диаграмме 1.
Диаграмма 1.
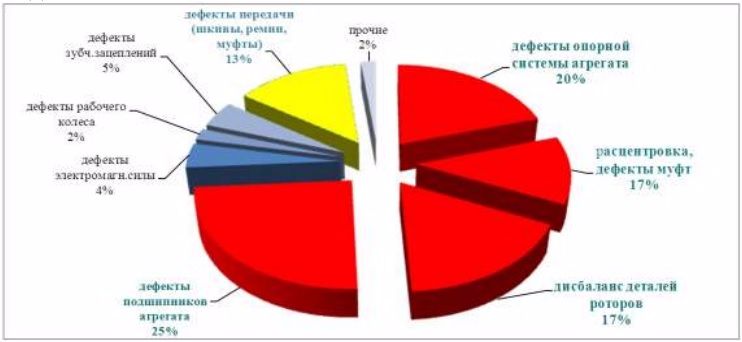
Мне хочется предложить вашему вниманию несколько практических примеров по выявлению наиболее распостранённых дефектов, являющихся в основном типовыми для
данного вида оборудования. Приведены описания нескольких особо ответственных агрегатов, протоколов их диагностирования и порядок устранения дефектов. В протоколах приведены только дефекты, имеющие уровень развития не ниже среднего.
При подготовке настоящего материала использован опыт автора и его коллег по применению разработанных мер для повышения надежности реально существующих и
эксплуатируемых машин на нашем предприятии.
На схеме агрегата приняты обозначения В,Г,О указывают направление измерений СКЗ виброскоростей соответственно: вертикальное, горизонтальное и осевое и их
значения в мм/сек. С целью предоставления компактности доклада предусмотрены:
− сокращение в фрагментах протоколов вибродиагностирования с оценками “Допустимо” и “Допустимо после ремонта”;
− дополнительные рекомендации и комментарии о необходимости виромониторинга данного оборудования и его периодичность;
− цифрами обозначены номера опор;
− ЭД –электродвигатель;
− СКЗ- среденеквадротичное значение;
− КИПВ- контрольные измерения параметров вибрации.
Пример 1.
1.1 После ремонта электродвигателя и установки его на технологическую позицию перед центровкой валов и подключения к насосу произведено виброобследование ЭД.
Фрагмент протокола диагностирования
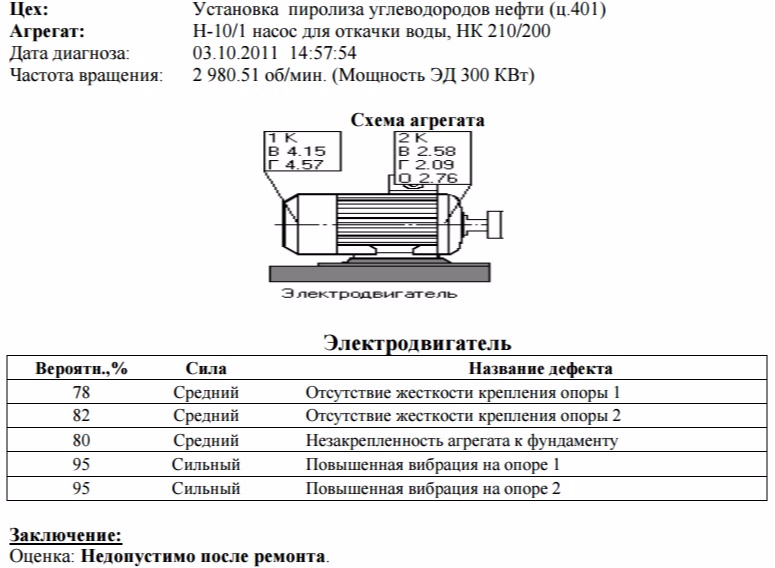
Комментарии:
Измерения вибрации в режиме реального времени показали, что уровень СКЗ виброскорости в горизонтальном направлении является не стабильным и изменяется от
3 мм/с до 6 мм/с, с периодичностью 1 минута, при этом вибрация в вертикальном направлении (4,1 мм/с) практически не меняется.
Проведенные исследовательские мероприятия позволяют сделать предположение, что высокий уровень вибрации и ее нестабильность в горизонтальном направлении являются следствием недостаточной площади опорной поверхности лап электродвигателя.
В результате «принудительного» притягивания лап происходила деформация корпуса электродвигателя, что приводит к высоким уровням вибрации.
Рис.1. Сигнал виброускорения 1кГц опоры 1 направление горизонтальное.
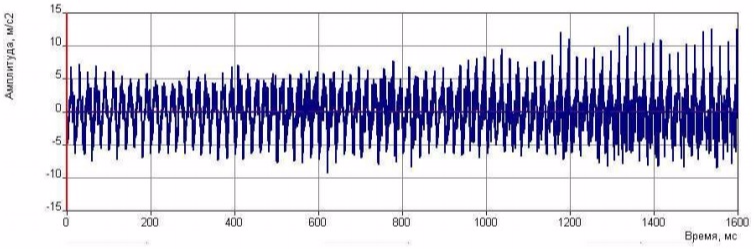
Рекомендации:
Увеличить опорную поверхность прилегания лап электродвигателя к раме.
Рис.2. Фото опорных поверхностей лап электродвигателя.
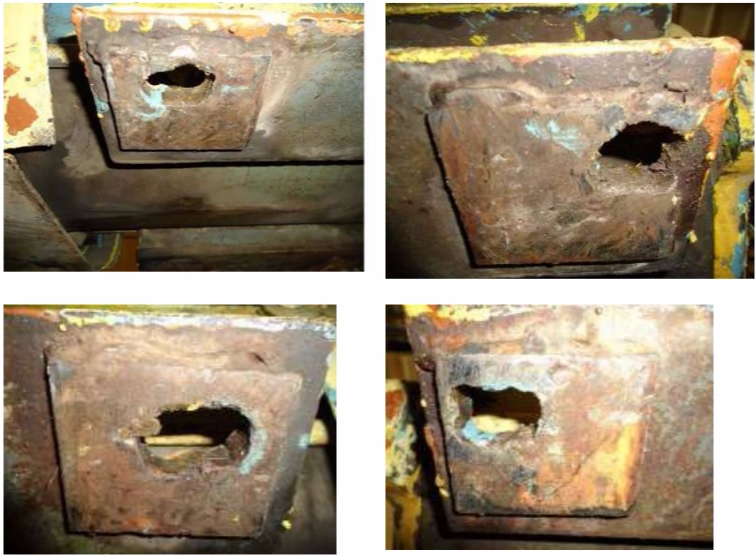
1.2 Состояние агрегата после проведения дополнительных мероприятий (доработка опорной поверхности лап), инициированных группой вибродиагностики.
Фрагмент протокола диагностирования
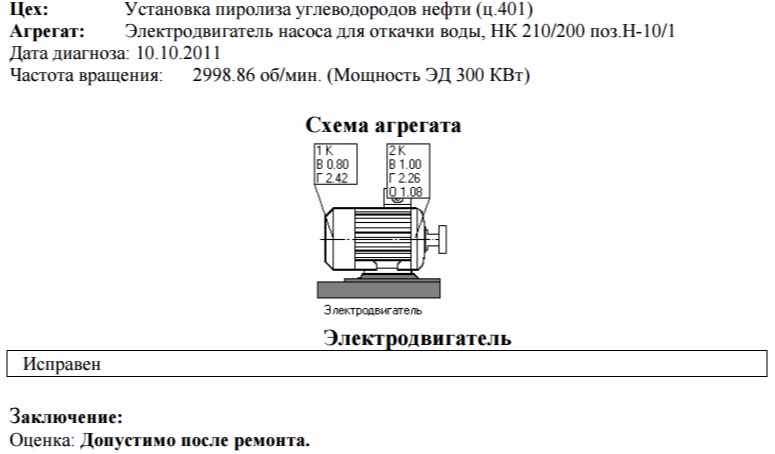
Пример 2.
2.1 Диагностирование сетевого насоса СЭ 1250\140 поз.402.Б производилось по графику вибродиагностирования перед ремонтом.
Фрагмент протокола диагностирования

Комментарии:
Основными причинами повышенной вибрации агрегата являются: дефект рабочего колеса насоса (См. Рис.5), дефект подшипника опоры №4 (См. Рис.5).
Рис.3. Спектр СКЗ виброскорости опоры № 4 – направление осевое.
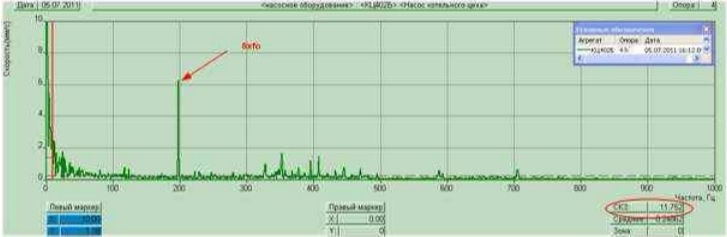
Основной вклад в повышенное значение вибрации агрегата вносит восьмая гармоника оборотной частоты (198,13 Гц), что свидетельствует о дефекте рабочего колеса насоса.
Рис.4. Спектры виброускорения от 10 до 10 000 Гц. Подшипниковая опора № 4 – горизонтальное направление.
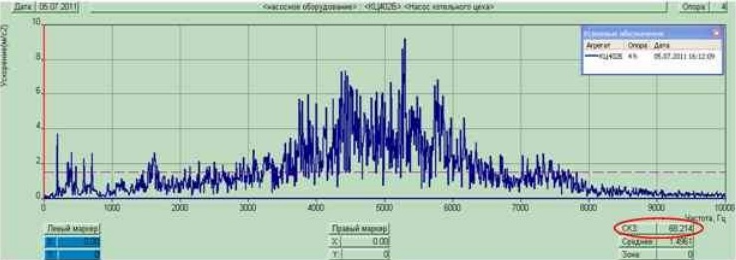
Значение СКЗ виброускорения составляет 68 м/с², что свидетельствует о развитии трения в подшипниковом узле опоры 4.
Рекомендации:
Произвести замену подшипника опоры 4, ремонт/замену рабочего колеса насоса.
Рис.5. Фото демонтированного рабочего колеса с дефектом одной лопатки (слева) и подшипника опоры 4(справа).
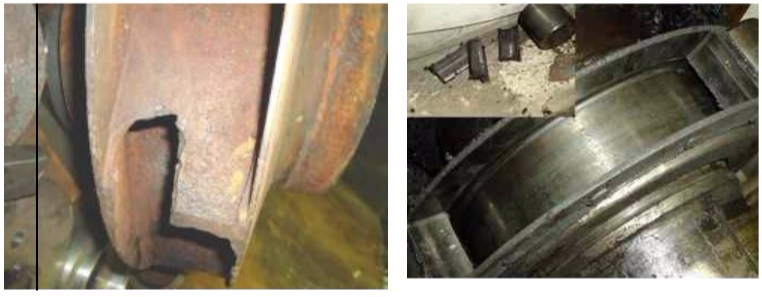
2.2 Состояние агрегата после проведения дополнительных мероприятий (замена подшипника, замена колеса), инициированных группой вибродиагностики.
Фрагмент протокола диагностирования
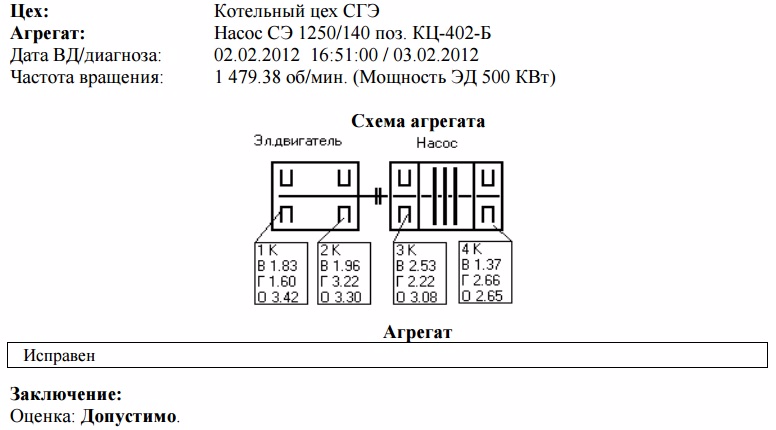
Пример 3.
3.1. Проведение диагностирования выполнялось по заявке механика установки, причиной которой являлась повышенная вибрация агрегата.
Фрагмент протокола диагностирования
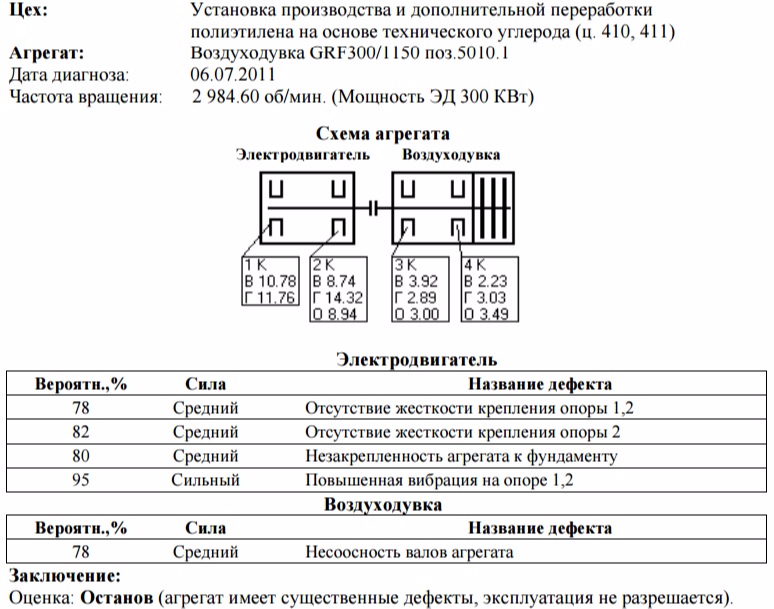
Комментарии:
Основной причиной повышенной вибрации агрегата является отсутствие жёсткости его опорной системы (имеются механические ослабления крепления агрегата в системе «болт-лапа-рама», а также «рама-анкер-фундамент»). Контурная диаграмма распределения вибрации по опорной конструкции агрегата приведена на Рис.6.
Рис.6. Контурная диаграмма распределения вибрации по опорной конструкции агрегата.
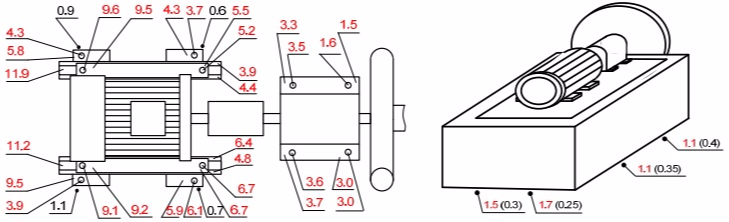
Высокие значения СКЗ виброскорости (Ve – мм/с) в системе болт-лапа-рама свидетельствует о том, что имеется существенное ослабление опорной системы агрегата.
Значение СКЗ виброскорости по периметру фундаментного блока находится в диапазоне 1,1÷1,7 мм/с, для примера в этих же точках по периметру фундаментного блока соседнего агрегата (воздуходувка поз.5010.2) вибрация составляет 0,25÷0,4 мм/с, что примерно в 3÷5 раза меньше. На схеме значения СКЗ виброскорости для агрегата 5010.2 указаны в скобках.
Рис.7. Фото опорной конструкции воздуходувки GRF300/1150 5010.1 до ремонта.
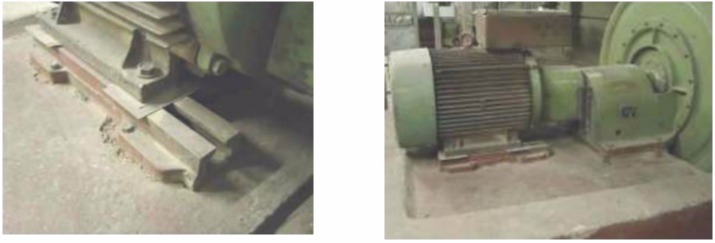
Рис.8. Спектр виброускорения. Опора №2- направление вертикальное.
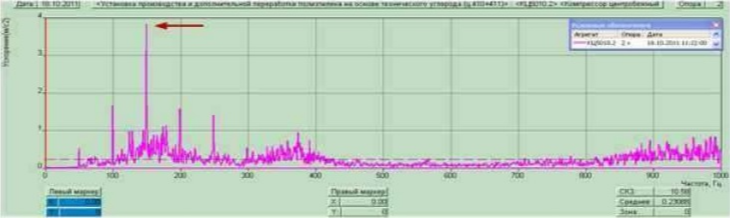
В спектре виброускорения доминирует третья оборотная частота (3fo) ротора электродвигателя, что свидетельствует о недостаточной жесткости опорной системы.
Рекомендации:
Обеспечить жёсткость опорной конструкции агрегата. Произвести замену анкерных болтов под опорами №1 и №2 электродвигателя. Произвести протяжку всех болтовых соединений крепления станины агрегата к раме (по опорам: 1, 2, 3, 4).
3.2. Состояние агрегата после проведения дополнительных мероприятий (см. выше в рекомендациях), инициированных группой вибродиагностики.
Фрагмент протокола диагностирования
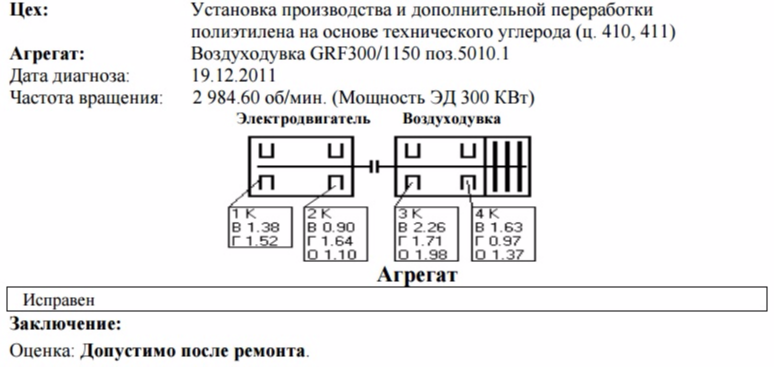
Рис.9. Фото опорной конструкции воздуходувки GRF300/1150 5010.1 после ремонта.
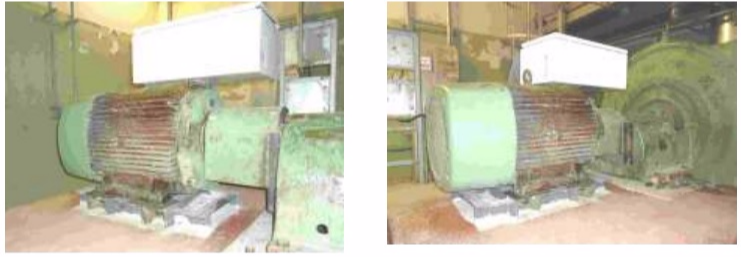
Пример 4.
4.1 Обследование агрегата проводилось по графику после ремонта.
Фрагмент протокола диагностирования
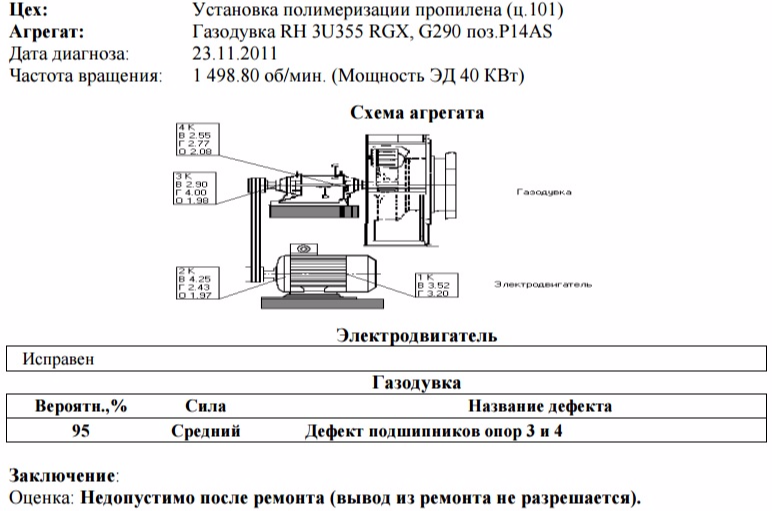
Комментарии:
Уровень СКЗ виброускорения подшипников опор 3 и 4 составляет – 101,23 м/с² и 95,72 м/с², что свидетельствует о повышенном трении в подшипниковых узлах, cм.Рис.10.
После ремонта от 26.10.2011г. спектр СКЗ виброускорения 10 000 Гц, см.Рис.11.
После ремонта от 20.07.2011г. наблюдалась аналогичная ситуация, см.Рис. 12, в результате подшипники отработали менее месяца.
Рис.10. Спектр виброускорения 10 000 Гц опоры 3 от 23.11.2011г.
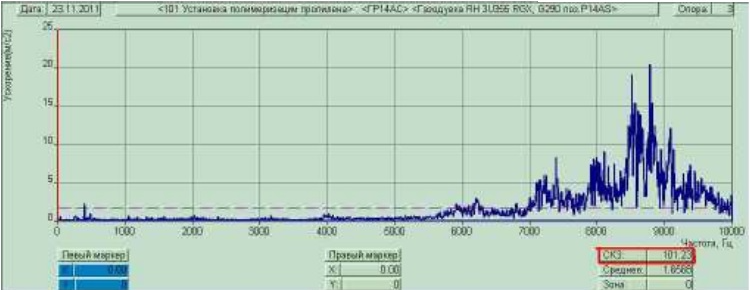
Рис.11. Спектр виброускорения 10 000 Гц опоры 4 от 26.10.2011г.
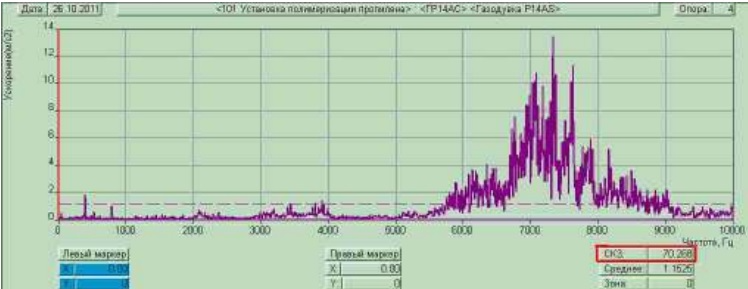
Рис.12. Спектр виброускорения 10 000 Гц опоры 4 от 20.07.2011г.
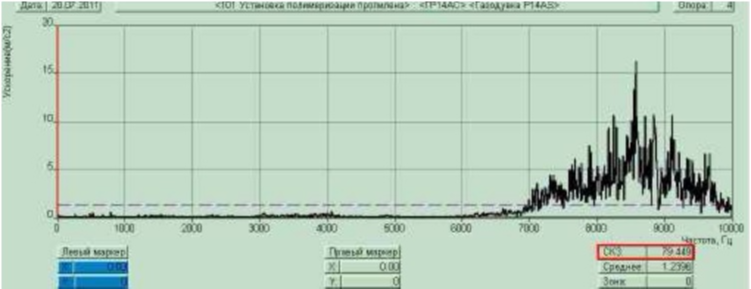
Рис.13. Фото демонтированного подшипника опоры 3.
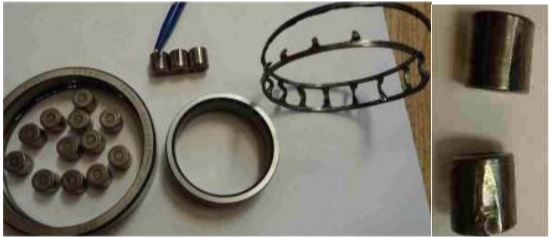
4.2 Состояние агрегата после проведения дополнительных мероприятий, инициированных группой вибродиагностики.
Фрагмент протокола диагностирования
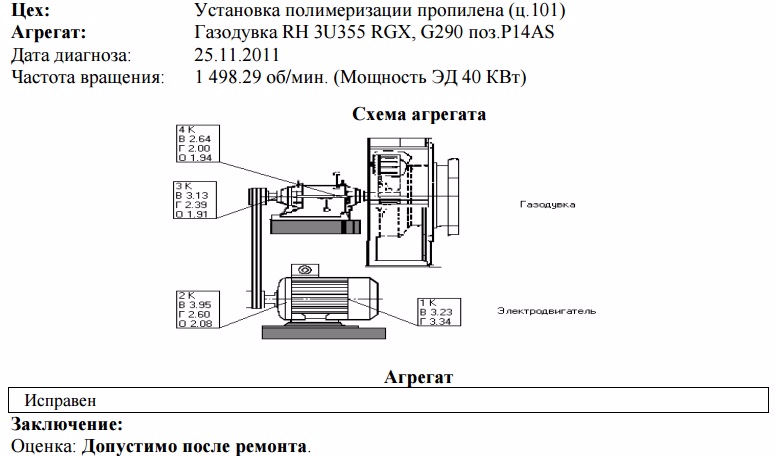
Пример 5.
5.1 Обследование проводилось по графику перед ремонтом.
Фрагмент протокола диагностирования

Комментарии:
Основной причиной повышенной вибрации является несоосность зубчатой передачи (cм. Рис.16).
Рис.14. Фото Экструдер ЧПСп 320х10 поз.А-404/1.
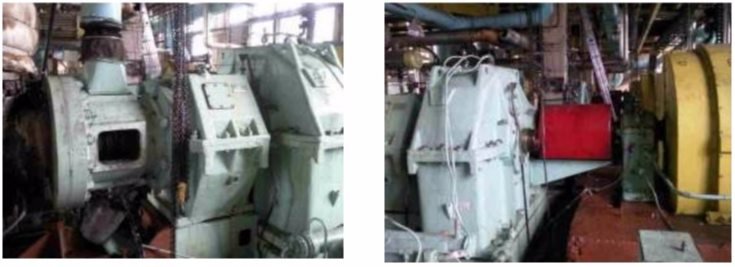
Рис.15. Прямой спектр виброускорения от 2-1000 Гц. Опора № 5, горизонтальное направление.
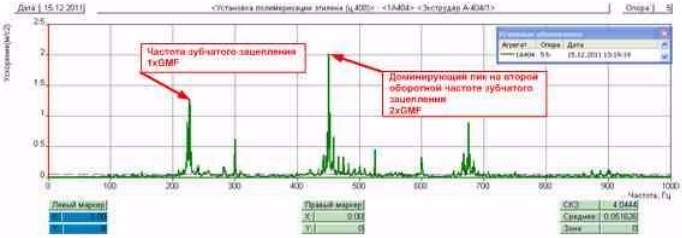
Возбуждение второй гармоники зубчатого зацепления вызвано несоосностью валов редуктора. Вследствие данного дефекта наблюдается повышенное значение СКЗ виброскорости в осевом направлении на опоре № 5.
Рекомендации:
1. Обеспечить проведение КИПВ 1 уровня (вибромониторинг агрегата) – не менее 1 раза в сутки. При резком изменении уровня вибрации относительно значений данного обследования (в 1,5 и более раз, но не менее чем на 1 мм/с) инициировать проведение ВД (КИПВ 2 уровня).
2. В период очередного планового ремонта: произвести ревизию зубчатого зацепления редуктора (проверить параллельность укладки зубчатой пары), ревизию подшипника опоры №5.
В результате ревизии редуктора экструдера поз. А-404/1 выявлен небольшой перекос шевронной передачи. Поскольку ремонт данного дефекта длительный, были разработаны корректирующие мероприятия по устранению дефекта в период остановочного ремонта (ревизия и ремонт посадочных мест подшипников редуктора, параллельную укладку валов и шевронной передачи), а до ремонта организован периодический контроль параметров вибрации.
Рис.16. Фото шевронной передачи на ревизии.
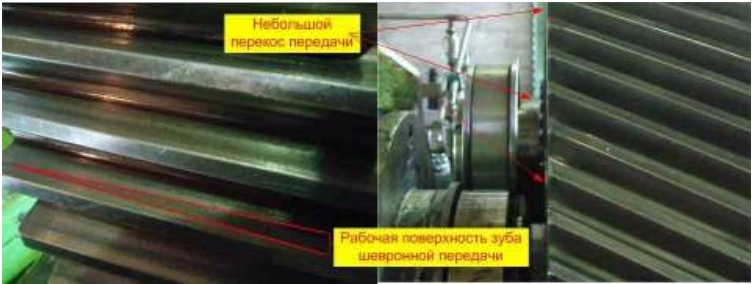
Пример 6.
6.1 Обследование проводилось по графику после ремонта агрегат находился в продолжительном простое, данные о состоянии агрегата до ремонта отсутствуют.
Фрагмент протокола диагностирования
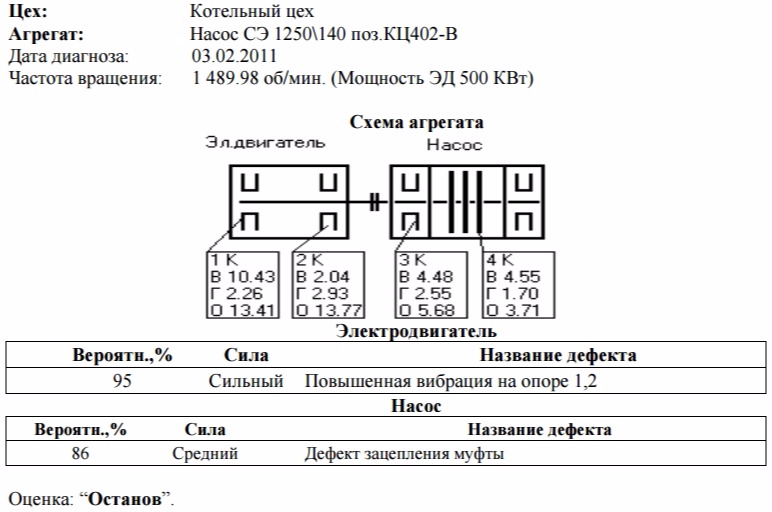
Рис.17. Фото опорной конструкции электродвигателя насосного агрегата СЭ. Опор 1,2 (задняя левая лапа двигателя, задняя правая лапа двигателя соответственно). Контурная диаграмма опоры 1 Электродвигателя Шпилька-Лапа-Рама-Закладная фундамента.
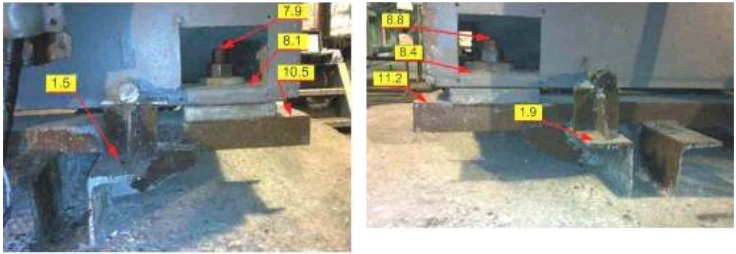
Рекомендации:
Произвести укрепление опорной конструкции опоры №1, ревизию муфтового соединения.
Комментарии:
Из-за длительного технологического простоя агрегата вибрационное обследование до ремонта не проводилось, дефект опорной системы можно было определить ещё ранее. Однако агрегат после ремонта не проходил регламентную обкатку. В течение 2011г. были проведены строительно-монтажные работы на данной позиции по замене рамы и фундамента.
6.2 Состояние агрегата после проведения дополнительных мероприятий, инициированных группой вибродиагностики.
Фрагмент протокола диагностирования
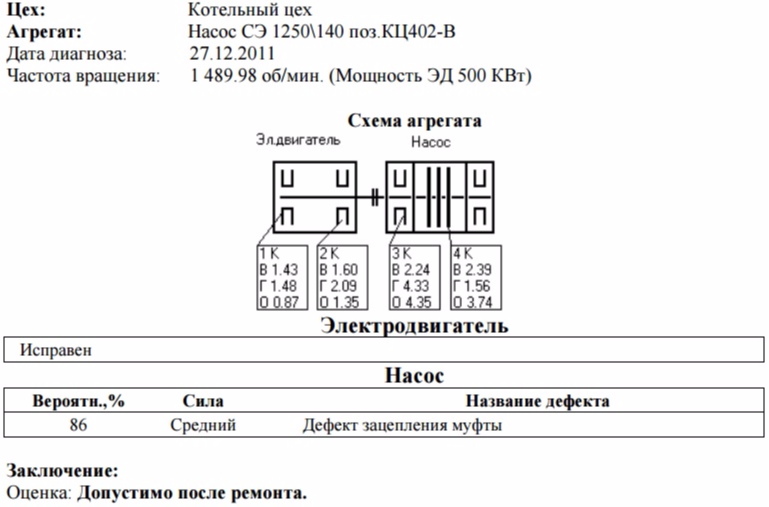
Комментарии:
Дефект зацепления муфты не критичен, требуется периодический вибромониторинг состояния агрегата.
Рекомендации:
В период очередного ТР или технологического останова произвести ремонт муфтового соединения.
Рис.18. Фото опорной конструкции ЭД насосного агрегата СЭ после ремонта.
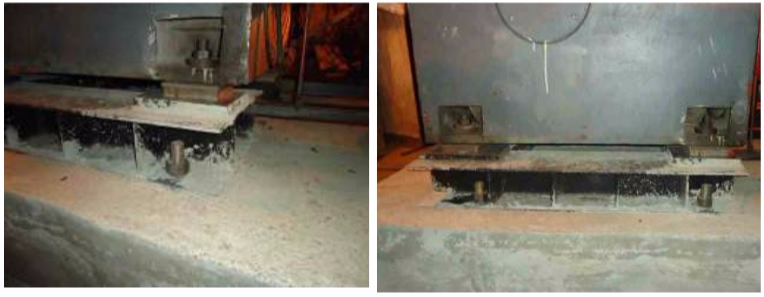
Стационарная система диагностирования поршневых компрессоров PROGNOST
Краткие сведения о системе PROGNOST:
При вибрационном обследовании механизмов роторного типа пока ещё использовался “простой” метод мониторинга среднего уровня вибрации.
Рис.19. Сигнал виброускорения (сверху) и уровень СКЗ вибросигнала (снизу) за один оборот коленвала.
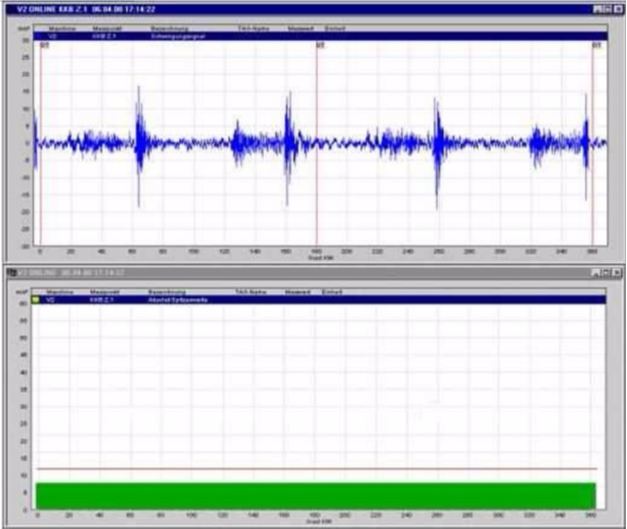
В системе PROGNOST предусмотрен сегментированный анализ вибрации, в зависимости от угла поворота коленчатого вала.
В течение каждого оборота, временное представление вибросигнала разделяется на 36 сегментов, каждый по 10 градусов поворота коленчатого вала. Таким образом, устанавливается взаимосвязь между вибрационными событиями и углом поворота коленвала в зависимости от функционирования компрессора, например: открытие/закрытие всасывающих/нагнетаельных клапанов, вибрация в момент реверса механизма движения и другие. Рассчитываются индивидуальные значения СКЗ или абсолютных максимумов для каждого сегмента, которые сравниваются с соответствующими индивидуальными уставками.
Рис.20. Сигнал виброускорения и значения СКЗ по каждому из сегментов.
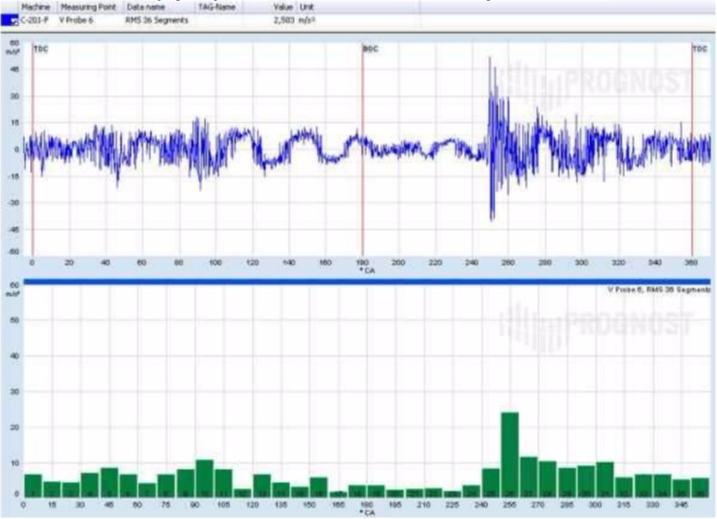
В зависимости от технологического режима работы поршневого механизма автоматически изменяется уставка для всех сегментов индивидуально для каждого компрессора.
Рис.21. Тренд виброускорения и автоматического выбора уставки в зависимсти от технологического режима поршневого механизма.
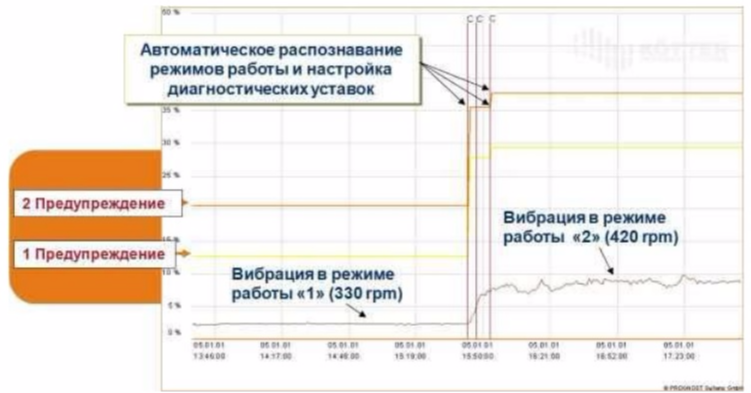
Принятая и записаная кривая давления конвертируется в диаграмму зависимости давление-объём (pV-диаграмма), для которой рассчитываются характеристические
значения для определённых фиксированных точек. Повреждение клапанов, поршневых колец и уплотнений, приводящие к утечкам, вызывают изменения характеристических значений на измеренной кривой давления.
Рис.22. Анализ Pv диаграмм.
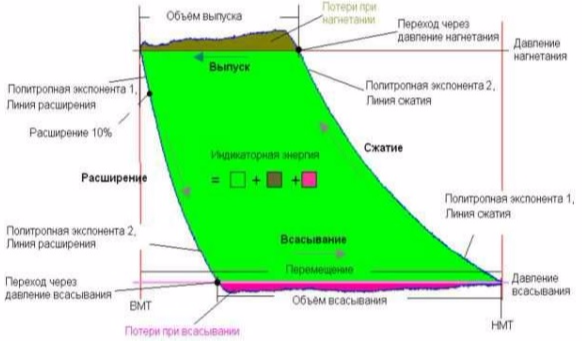
Системы PROGNOST ® не адаптированы для поршневых машин, а специально разработаны для мониторинга машин возвратно-поступательного действия.
Пример 7.
7.1 Обследование поршневого компрессора 1 каскада Производства полиэтилена РТ1.4М16-12,5/17-281М1 поз.А-124 с помощью диагностической системы PROGNOST.
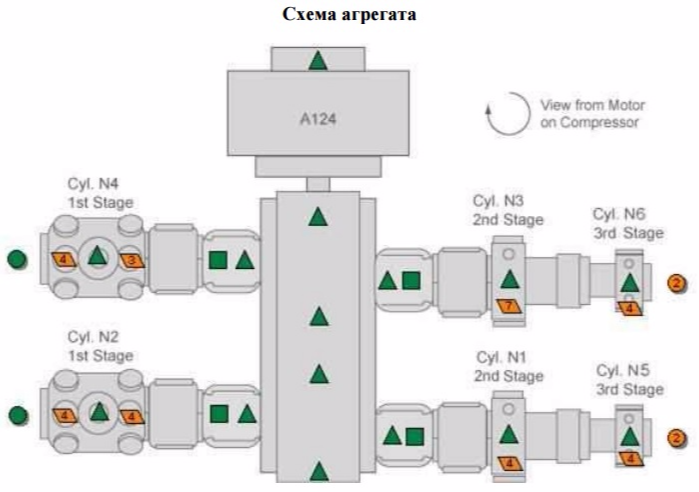
При использовании сегментированного анализа вибрации, сигналов виброускорения используя стационарную систему Prognost совместно со специалистами фирмы “Новые технологии мониторинга” выявили неисправность всасывающего клапана со стороны крышки цилиндра №4.
Рис.23. Сигнал виброускорения 4-го цилиндра компрессора поршневого РТ1.4М16-12,5/17-281М1 поз.А-124 (красный), сигналы с датчиков давления со стороны головки цилиндра (коричневый), со стороны коленчатого вала (зелёный) и усилия поршневого штока (фиолетовый). Дата обследования: 24.01.2012.
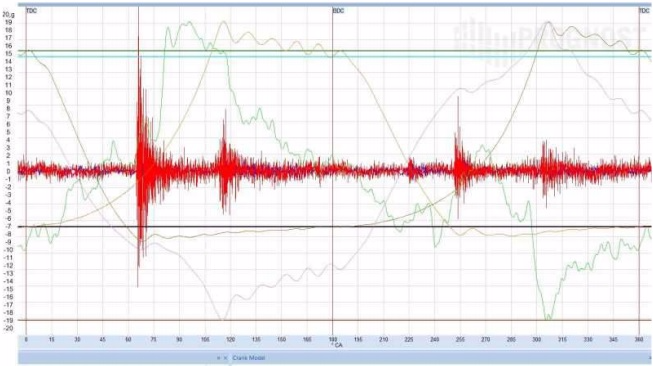
В период ремонта рекомендовали заменить всасывающий клапан цилиндра №4 со стороны головки цилиндра.
Рис.24. Сигнал виброускорения цилиндра 4 компрессора поршневого РТ1.4М16-12,5/17-281М1 поз.А-124 на 15.02.2012. После ремонта.
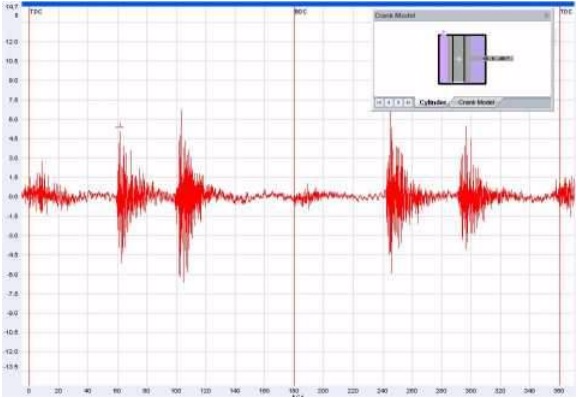
В ходе ремонта клапан был заменён, в результате вибрация значительно снизилась (в 1.5 раза).
Рис.25. 3D-Спектр амплитуды виброускорения 4-го цилиндра компрессора поршневого РТ1.4М16-12,5/17-281М1 поз.А-124.
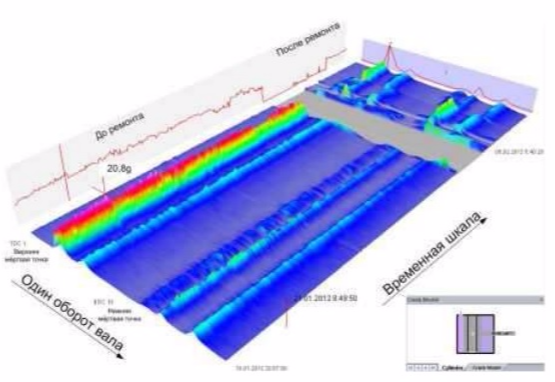
При вскрытии клапана в канавке под пластиной клапана обнаружился обломок материала, из которого изготовлены кольца цилиндра. При работе компрессора в процессе открытия клапана обломок вызывал вибрацию при прохождении газа сквозь клапан. Оказалось, что клапан исправен, но мог выйти из строя при измельчении материала обломка и попадании его под пластину клапана. Кроме того, по наличию обломка можно предположить, что одно из колец указанного цилиндра требует замены при следующем ремонте.
Рис.26. Фото всасывающего клапана 4-го цилиндра компрессора поршневого РТ1.4М16-12,5/17-281М1 поз.А-124.
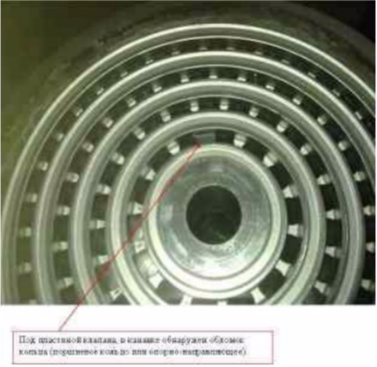
Заключение
Общая статистика работы группы вибродиагностики за период с июня 2010 по декабрь 2011 (19 мес.).
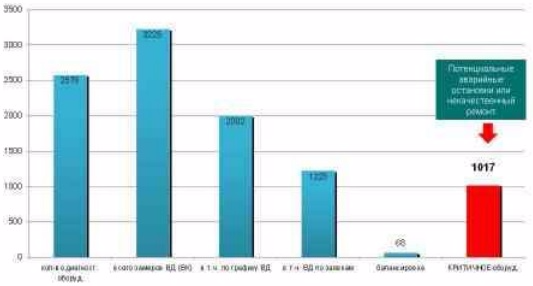
Вибродиагностирование агрегатов на первых этапах перехода к системе ремонта “по техническому состоянию”, в основном, уже позволило определить реальное техническое состояние агрегатов, найти проблемные места оборудования, накопить базу данных вибросостояния оборудования. Вибрационные обследования позволяют
своевременно принять меры к оборудованию с критичными оценками по результатам вибродиагностирования, а так же допустить увеличение межремонтных интервалов при отсутствии дефектов в оборудовании и при организованном периодическом виброконтроле и вибродиагностировании.
Томский опыт вибродиагностики, квалификация наших специалистов и хорошо налаженная работа диагностической службы предприятия подтверждает реальность планов «Томскнефтехим» в переходе на техническое обслуживание и ремонт оборудования по техническому состоянию совместно с надёжными партнёрами ЗАО «ПромСервис», “НТМ” и “Prognost”. Но для этого ещё многое нужно сделать: накопить опыт, укомплектоваться резервным оборудованием, получить формально согласованное право на такой переход.