Профилактические и прогностические методы обнаружения крутильных колебаний
Бывает, что мы встречаемся с необъяснимыми проблемами, которые не можем истолковать используя обычные средства и методы вибродиагностики. И не всем нам приходит в голову, что повышенная вибрация и отказы оборудования могут быть связаны с крутильными колебаниями. Что они собой представляют, чем опасны и как выявляются, читайте в данной статье.
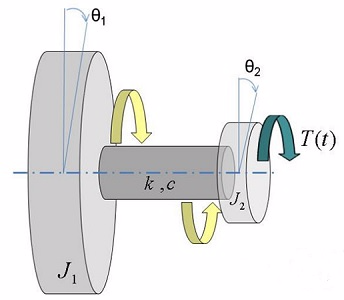
Аннотация
В то время как анализ вибрации рассматривается как один из наиболее эффективных инструментов оценки работоспособности оборудования, крутильная вибрация часто игнорируется и неправильно понимается. Измерение радиальной и осевой вибрации вала и/или корпуса оборудования обычно не дает представления об угловых вибрациях, создаваемых кручением, в центробежных или возвратно-поступательных машинах. Оставленная незамеченной, крутильная вибрация может привести к быстрому выходу из строя муфт, подшипников и валов, создавая потенциальную угрозу для работоспособности и безопасности.
Профилактическое обслуживание может помочь в обнаружении крутильных колебаний путем определения характера истирания, сцепления гибких элементов и точек возникновения трещин. Однако, эти условия возникают позже, после отказа и не дают достаточно информации, чтобы правильно определить серьезность, частоту или источник вибрации.
Начиная с понимания законов движения, динамику кручения любой механической передачи можно анализировать на этапе проектирования оборудования, чтобы избежать возникновения неблагоприятных ситуаций. Для оборудования, которое уже смонтировано, современные системы измерения крутящего момента могут использоваться для проверки теоретических моделей, оценки изменений в компонентах трансмиссии или постоянного мониторинга крутящего момента для эффективной идентификации дефекта. Интеграция угловых, радиальных и осевых колебаний может обеспечить комплексную систему мониторинга состояния критических активов, подверженных этим режимам отказов во многих отраслях промышленности.
Введение
Крутильная вибрация описывает угловое движение вала(ов) в трансмиссии, которое накладывается на установившееся вращательное движение центробежной или возвратно-поступательной машины. Проще говоря, крутильная вибрация относится к угловому или «крутящему» движению вращающихся валов, которые соединяют различные части оборудования в трансмиссии. Эта форма вибрации может быть вызвана приводом, приводным оборудованием или просто быть результатом того, как различные инерции (вращающиеся массы) и жесткость пружин распределены по трансмиссии. Приводы, такие как поршневые двигатели и ЧРП (частотно-регулируемые приводы), и приводное оборудование, такое как мельницы, большие вентиляторы, поршневые компрессоры, генераторы и различные турбомашины, могут быть подвержены проблемам с крутильной вибрацией.
В зависимости от источника, крутильная вибрация может присутствовать в разных формах. Внезапное воздействие (пример, показанный на рисунке 1) из-за прерывистой нагрузки, запуска оборудования или сбоев технологического процесса может вызвать вибрации, которые состоят из резкого пика, сопровождаемого последующими колебаниями, которые в конечном итоге затухают. В качестве альтернативы крутильные колебания могут иметь более непрерывный характер в результате постоянных условий процесса, колебаний управления двигателем или резонансных условий, как показано на рисунке 2.
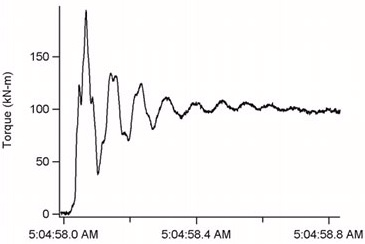
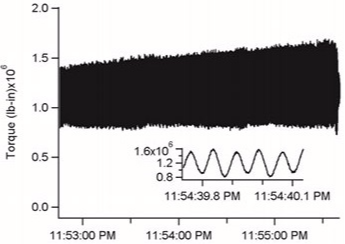
Как и в случае любого типа вибрации, резонансное состояние будет существовать, когда частота возбуждения находится в непосредственной близости от собственной частоты. Как правило, крутильный резонанс более распространен в высокоскоростных (> 600 об / мин) машинах. Пример крутильного резонанса во время запуска и выбега двигателя центробежного компрессора показан на рисунке 3. В этом случае первая собственная крутильная частота возбуждалась скоростью вращения, создавая колебательные моменты на частоте 16 Гц. Эти измерения крутящего момента могут быть использованы для выявления потенциально вредных условий эксплуатации, которых следует избегать.
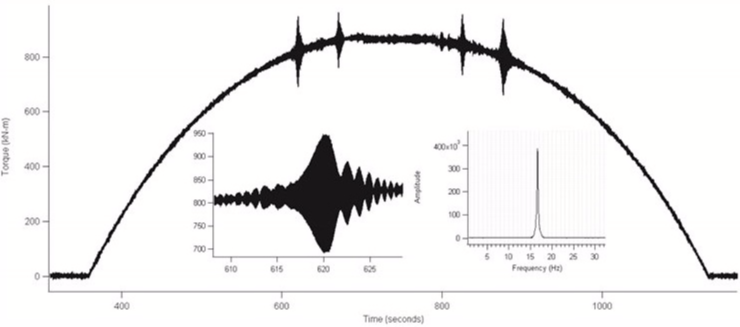
Использование измерений крутящего момента
Для практического использования измерение значения крутящего момента должно быть связано с механическим напряжением, которое оно вызывает в компоненте трансмиссии. Крутящий момент может повредить оборудование, когда он вызывает напряжения в материале, передающем нагрузку, которое превышает предел выносливости или предел текучести. Предел выносливости - это максимальное напряжение, которому материал может подвергаться многократно, не испытывая усталости. Эти значения, как правило, намного ниже, чем напряжение, необходимое для деформации или разрушения материала от однократно приложенной нагрузки. Усталость обычно прогрессирует в трех стадиях: зарождение трещины, распространение трещины и окончательное разрушение. На начальных этапах распространения усталостной трещины (рисунок 4) деформация материала не происходит, пока напряжения остаются ниже предела текучести. Это одна из основных причин того, что крутильные отказы трудно обнаружить. Позднее, при отказе или в случае нагрузок с большой амплитудой, деформации вращающегося вала, гибкой муфты или зубьев шестерни обычно можно обнаружить с использованием традиционных средств анализа вибрации, поскольку они могут вызвать эксцентрическое вращение компонента, что приводит к дисбалансу (рисунок 5). Следует отметить, что отказ может произойти после того, как усталостная трещина выросла, и компонент машины больше не способен передавать номинальную нагрузку, даже если она ниже предела текучести материала. Трещины и изломы, которые развиваются под углом 45 градусов к оси вала, типичны при отказах, связанных с крутящим моментом.
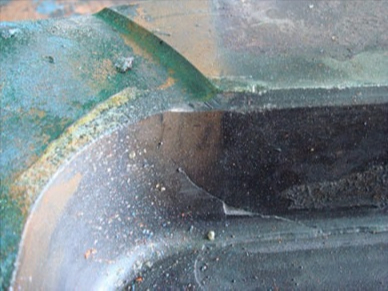
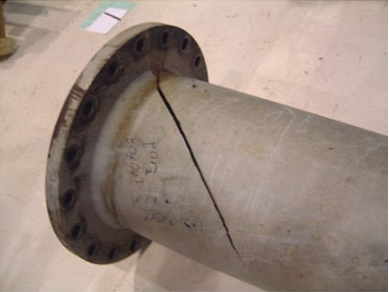
Одним из относительно простых методов определения приемлемых уровней напряжения от переменных нагрузок является модифицированная диаграмма Гудмана. Этот график отображает значение среднего напряжения на горизонтальной оси и значение переменного напряжения на вертикальной оси. Комбинация средних и переменных напряжений в области под «линией текучести» и «измененной линией Гудмана» (заштриховано серым цветом на рисунке) указывает на бесконечную усталостную долговечность. Напряжения за пределами этого региона указывают на конечную долговечность. Значения, приведенные на рисунке 6, были рассчитаны, чтобы понять влияние переменных нагрузок на усталостную долговечность зубьев шестерни, в частности усталость при изгибе в основании зуба. Среднее напряжение считалось как напряжение от номинального крутящего момента (в зависимости от мощности и скорости, указанной на паспортной табличке). Поскольку измерения крутящего момента не были доступны, гипотетические значения переменного крутящего момента добавлялись в виде процентов от номинального крутящего момента. Анализ показал, что средние напряжения, в 4-5 раз превышающие номинальные значения в сочетании с циклическими нагрузками, могут создать конечное время жизни зуба шестерни. В то время как напряжения зубьев зубчатых колес относительно просто рассчитать, для более сложной геометрии необходимо использовать другие методы, такие как анализ методом конечных элементов.
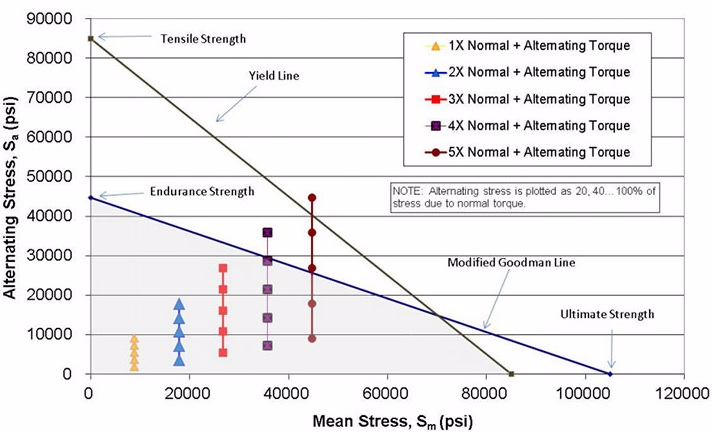
В примере, использованном для рисунка 2, предел выносливости рассчитывался как процент от предела прочности при растяжении (обычно 42,5% от предела прочности для данного материала). При определении безопасных пределов следует учитывать и другие факторы, которые могут еще больше снизить предел выносливости: состояние поверхности, рабочая температура, размер, нагрузка и критичность. Испытание образца материала является наиболее точным способом определения предела выносливости, и его следует проводить для критических компонентов и тех, которые рассчитаны на срез в случае перегрузки (штифты, канавки и т.п.).
Ограничением подхода использования модифицированной диаграммы Гудмана является то, что он предполагает, что переменные напряжения возникают с постоянной амплитудой. В большинстве случаев амплитуда крутильных колебаний (и, следовательно, переменное напряжение) будет меняться. Кроме того, крутящие моменты, как показано на рисунке 7, лучше анализировать с помощью других методов. Правило Палмгрена-Майнера является одним из методов определения усталостной долговечности в случаях переменной амплитудной нагрузки.
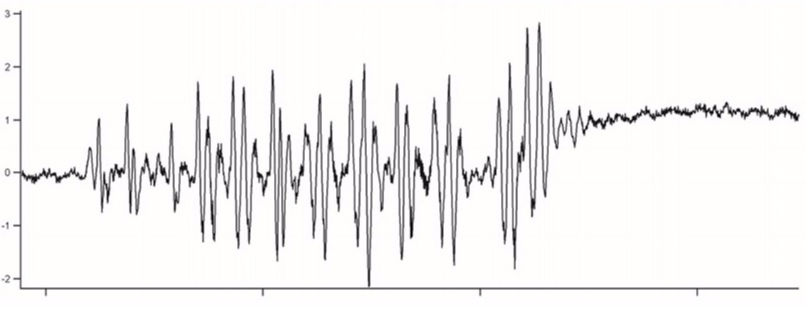
Профилактические методы
Амплитуда крутильных колебаний может быть разрушительной, и, поскольку большинство механизмов не оборудовано средствами для ее измерения, первым признаком проблемы обычно является отказ компонента механической передачи. Однако существуют некоторые методы, которые можно использовать для определения наличия крутильных колебаний. Гибкие соединительные муфты часто имеют признаки, которые можно обнаружить визуально при разборке или, в некоторых случаях, во время работы. Гибкие элементы муфты (т.е. пакет пластин, эластомерные блоки и т.д.), предназначенные для компенсации перекоса валов при передаче нагрузки, в первую очередь подвержены повреждениям, которые видны невооруженным глазом. Кроме того, части валов, шпоночные пазы и болтовые фланцевые соединения могут иметь видимые повреждения.
В трансмиссиях, включающих в себя коробку передач, при наличии крутильных колебаний могут быть обнаружены слышимые шумы. Они могут звучать как «дребезжание» или ослабление в зубчатом зацеплении. Однако без более детального осмотра или фактических измерений невозможно определить нагрузки, происходящие во время этих событий. Обратите внимание, что радиальная вибрация на коробках передач очень ощутима, когда крутильная вибрация является сильной.
Фреттинг является результатом относительного движения двух поверхностей, подвергающихся нагрузке. Крутильная вибрация может вызвать фреттинг-износ болтовых фланцевых соединений, шлицев и стыков между втулкой и валом. Во время ревизии, муфты и валы должны быть тщательно осмотрены на наличие признаков истирания, так как оно уменьшает усталостную долговечность и является причиной возникновения трещин. Для материалов с металлической поверхностью, истирания проявляются в виде красновато-коричневых участков, которые являются частицами окисленного износа. Также, некоторые участки могут выглядеть полированными от частиц износа в соединении. На рисунке 8 показан истирающий износ вокруг болтового отверстия фланцевого соединения, вызванный относительным перемещением фланца и шайбы.
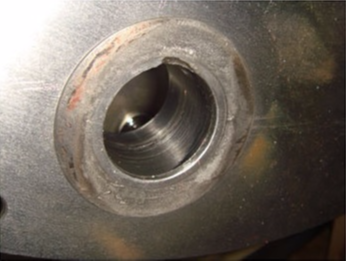
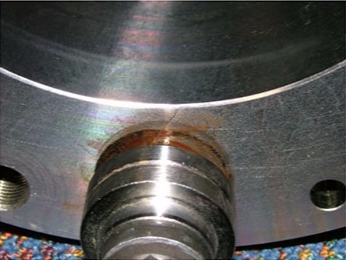
Визуальный осмотр также должен быть направлен на обнаружение поверхностных трещин в несущих компонентах. Следует обратить внимание на участки, где напряжение может концентрироваться из-за острых углов или резких изменений геометрии, таких как ступеньки вала, шпоночные канавки, сварные соединения и т.д. Недостатком визуального контроля является отсутствие возможности увидеть невооруженным глазом небольшие и подповерхностные трещины. Для критически важного оборудования, восприимчивого к крутильным колебаниям, методы контроля для обнаружения трещин должны включать либо контроль проникающего красителя, либо магнитопорошковый контроль. Пенетрант-красители эффективны для быстрого выявления поверхностных трещин, но не способны обнаруживать трещины под поверхностью и в некоторых случаях могут быть сложны в использовании. Магнитопорошковый является лучшим методом обнаружения трещин в металлах.
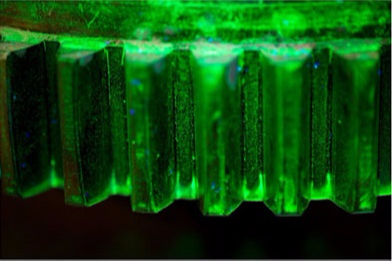
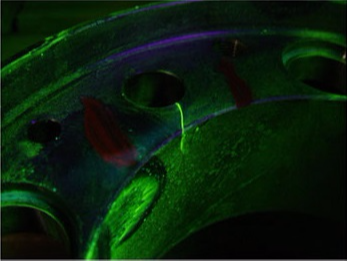
С некоторыми типами муфт, гибкий элемент которых виден во время работы, могут быть возможны неинтрузивные методы контроля. Использование стробоскопа во время работы может помочь выявить аномальные отклонения гибких элементов. В качестве примера, рисунки 12 и 13 показывают гибкий диск во время работы. Крутильная вибрация может привести к тому, что отдельные диски отделятся и будут прогибаться. Производители муфт могут предоставить рекомендации по допустимым пределам использования дисковой муфты. Обратите внимание, что расцентровка валов и ошибки при сборке также могут привести к этому эффекту. Проблемы, связанные с крутящим моментом, обычно приводят к тому, что на каждом элементе между болтовыми соединениями возникает изгиб. Это связано с тем, что пакеты дисков поочередно крепятся болтами к ведущей и ведомой стороне муфты.
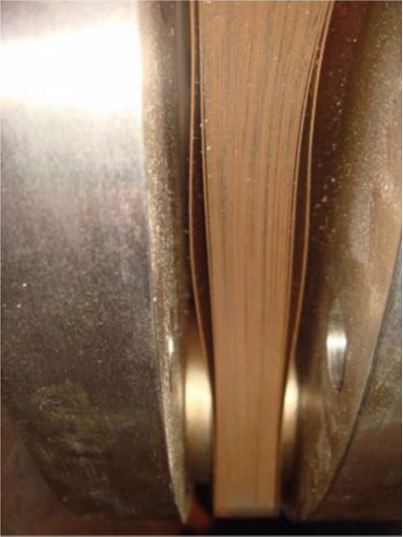
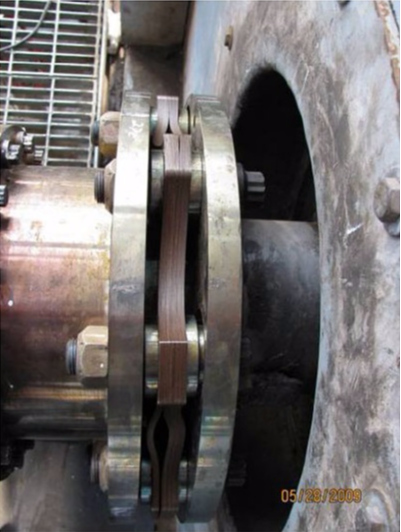
Эластомерные муфты часто устанавливаются для увеличения демпфирования системы и, следовательно, для уменьшения или ограничения крутильных колебаний. Эти муфты в качестве гибких элементов используют резину, работающую на растяжение/сжатие или сдвиг. Сжатая резина будет стремиться поглощать энергию крутильных колебаний в блоках, где она преобразуется в тепло. Чрезмерные вибрации расплавят резиновый материал изнутри блоков, которые не будут видны до тех пор, пока не произойдет полный отказ или пока эти блоки не будут срезаны для проверки при их замене. Резина в сдвиговых муфтах часто будет демонстрировать признаки разрушения на границе раздела между резиной и металлическим материалом, что может быть проверено визуально.
В случае возникновения неисправности следует проверить поверхность разрушения, поскольку она может помочь отличить различные потенциальные источники неисправностей - однократную перегрузку или крутильные колебания, которые присущи конструкции или работе трансмиссии, что требует более обширных корректирующих действий.
Анализ металла, выполненный компетентной испытательной лабораторией, даст наиболее полные результаты, но он может занять много времени и, как правило, не дает представление о необходимых конструктивных или эксплуатационных изменениях для устранения проблемы. Ключевой информацией, которая может быть получена от поверхности с трещиной, является точка зарождения трещины. Простое знание того, где началась трещина, может определить, следует ли учитывать конструктивные изменения, которые могут быть такими простыми, как увеличение радиуса, дробеструйная очистка поверхности от усталостного сопротивления или признание необходимости в улучшени технологических процессов. Большинство поверхностей с усталостным разрушением будут иметь бороздки, напоминающие приливные отметки на пляже. Эти метки расширяются наружу от точки возникновения трещины в виде круглой или полукруглой формы и сопровождаются областью быстрого разрушения. Могут присутствовать несколько точек инициации, которые возникают при пересечении отдельных меток.
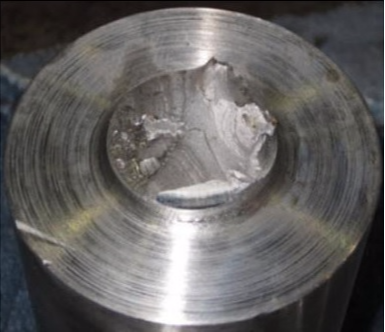
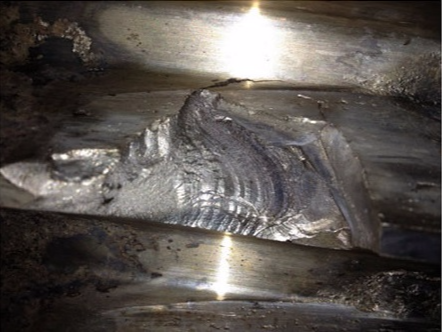
Усталость иногда используется как синоним возрастного отказа или износа оборудования. Усталостный износ происходит за время, связанное с циклами вибрации, но в некоторых случаях оно может быть считано секундами. Усталостные отказы, как правило, характеризуются низким циклом (<1000 циклов) или высоким циклом (>1000 циклов). Теоретически, если трансмиссия работает при 1800 об/мин и скорость совпадает с собственной частотой, усталостное разрушение может произойти в течение 30 секунд при условии, что вызванные напряжения превышают предел выносливости материала.
Отказы из-за периодической ударной нагрузки могут напоминать отказы из-за крутильных колебаний. Воздействие представляет собой один или несколько циклов вибрации, которые обычно возникают во время запуска, останова, изменения скорости или являются результатом механики процесса. Опять же, величина напряжений и частота их возникновения будут определять усталостную долговечность.
Крутильная динамика
Как и при любой форме вибрации, колебательное движение объекта определяется универсальными законами движения и обычно описывается в терминах системы масса-демпфер-пружина. Аналогично массе, при линейных колебаниях, инерция описывает вращающуюся массу в системе отсчета кручения. В трансмиссии инерцией обладают роторы двигателей, зубчатые передачи, маховики, роторы компрессоров, рабочие колеса насосов и т.д., которые связаны друг с другом муфтами и секциями вала. Простая система скручивания показана на рисунке 16 и может использоваться в качестве простого представления вентилятора с приводом от двигателя. Незатухающая собственная частота этой системы определяется в уравнении. Для более крупных трансмиссий с дополнительными инерциями вычисления для собственных частот становятся более сложными.
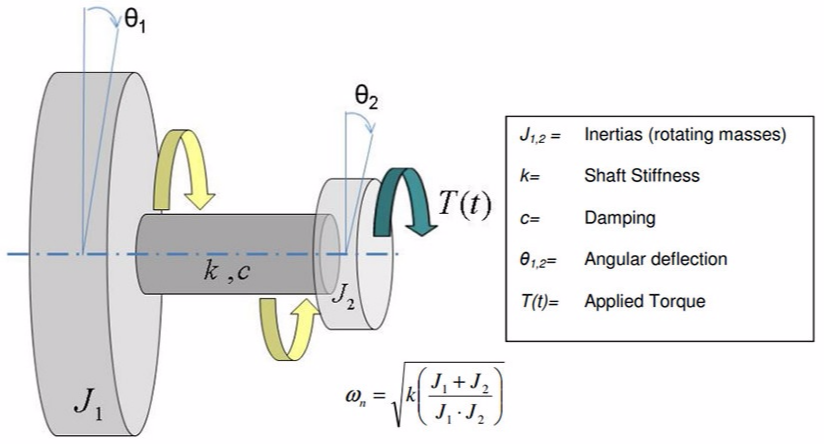
При проектировании трансмиссии характерно, что собственные крутильные частоты рассчитываются и сравниваются с известными источниками возбуждения, чтобы гарантировать отсутствие резонансов при нормальных рабочих условиях во всем предполагаемом диапазоне скоростей. Диаграмма Кэмпбелла, показанная на рисунке 17, обычно используется для определения мест пересечения собственных частот с источниками возбуждения.
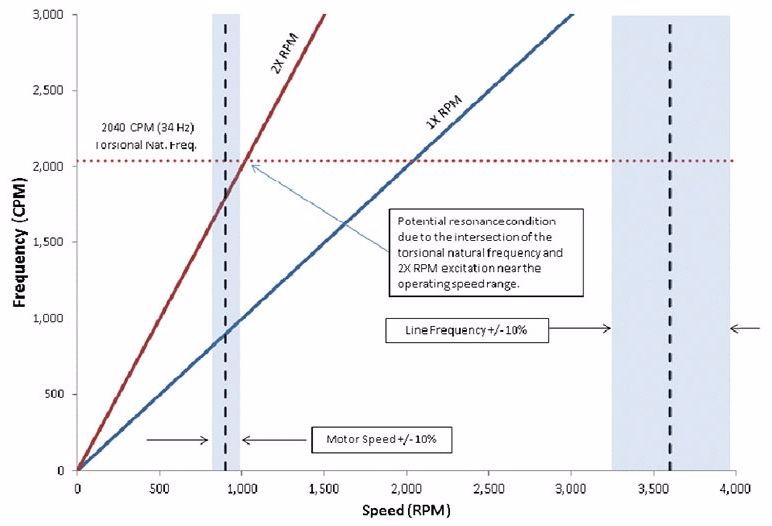
Горизонтальная пунктирная линия представляет собственную частоту системы. Когда она пересекаются с потенциальными частотами воздействия (1X об/мин, 2X об/мин, показанные наклонными линиями), существует вероятность того, что у вас будет резонансное состояние. Наибольшую обепокоенность вызывают пересечения в диапазоне рабочих скоростей.
Как показано на диаграмме Кэмпбелла, существует вероятность резонанса, когда оборудование работает в пределах нормального диапазона скоростей, который может быть возбужден собпадением крутильной собственной частоты и источников возбуждения со скоростью 2X об/мин. На практике это указывает на то, что вибрации, возникающие при 2-кратной частоте вращения двигателя, могут возбуждать собственную частоту кручения. Потенциальные источники этого типа вибрации будут включать в себя расцентровку валов. Если не будет правильно диагностирована проблема крутильного резонанса, корректирующие действия могут быть неправильно направлены на уменьшение смещения валов. В этом примере, хотя улучшенная центровка валов приведет к уменьшению источника возбуждения, будет трудно уменьшить амплитуду крутильных колебаний из-за характера резонанса.
Чтобы избежать усиления крутящего момента из-за резонанса, Американский институт нефти (API) рекомендует использовать минимальный запас в 10% между собственными частотами и источниками возбуждения. На диаграмме Кэмпбелла потенциальные источники возбуждения показаны в виде вертикальных полос. В соответствии с API 684:2005, анализ крутильных колебаний всегда должен выполняться для новых конструкций. Однако это не практикуется в других отраслях, и, к сожалению, крутильная вибрация не считается проблемой до тех пор, пока не произойдет отказ. Следует отметить, что безопасность и надежность системы с кручением определяется напряжением, а не просто запасом прочности от источников возбуждения, которые могут иметь или не иметь какое-либо значение.
Хотя большинство производителей оборудования изучают динамику кручения при проектировании трансмиссии, тем же анализом часто пренебрегают, когда модернизируется оборудование трансмиссии или меняются условия процесса для увеличения производительности установки. Измерение и анализ крутильных колебаний (либо на стадии проектирования, либо во время модернизации) помогут обеспечить оптимизацию процесса и надежность оборудования за счет снижения рисков, связанных с потенциально опасными условиями эксплуатации.
Анализ кручения может иметь различные уровни сложности. Взачастую, анализ заканчивается, если нет признаков возбуждения собственных частот. Тем не менее, из-за неопределенности в расчетах и вероятности возникновения непроектных условий эксплуатации, рекомендуется, чтобы анализ кручения включал расчет отклика вынужденной вибрации.
Анализ принудительного отклика обычно включает в себя создание математической модели трансмиссии и расчет результирующих напряжений от внешних крутящих моментов, генерируемых приводом и/или приводным оборудованием. Математическая модель обычно представляет собой дискретную систему масс-пружин с сосредоточенными параметрами в виде главных моментов инерции и пружин кручения в трансмиссии. Поскольку движение одной инерции в трансмиссии зависит от всех других инерций, разработана система уравнений, основанная на законах движения. Теоретические крутящие моменты могут быть применены к модели для моделирования различных условий, таких как запуск, удары и резонанс, путем изменения функции вращающегося во времени момента.
Уравнения движения для каждой инерции могут быть определены путем суммирования сил, приложенных к каждой инерции, как показано в уравнениях 2 ab для системы с двумя инерциями, показанной на рисунке 18. Из универсальных законов движения Ньютона сумма сил, действующих на объект равна массе объекта, умноженной на ускорение. В системе отсчета кручения это соответствует инерции (J), умноженной на угловое ускорение (Ӫ). При приложении к инерции внешнего изменяющегося во времени крутящего момента T (t) будут действовать равные и противоположные силы реакции, передаваемые по трансмиссии в соответствии с законами движения. Равные и противоположные силы связаны с характеристиками демпфирования и жесткости соединяемых валов.
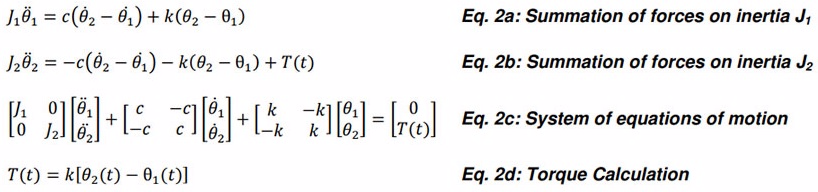
Большинство систем плохо описывается моделью с двумя инерциями, соединенными пружиной, и поэтому система уравнений будет намного больше. В этих случаях для моделирования крутильного отклика используется компьютерное программное обеспечение с использованием методов численного моделирования, таких как Рунге-Кутта.
Это моделирование используется для идентификации участков трансмиссии, которые могут подвергаться крутильным колебаниям высокой амплитуды. Это позволяет разработчикам вносить изменения в модель, такие как изменение жесткости пружины, добавление демпфирования или изменение значений инерции, чтобы определить, можно ли реализовать положительный эффект. Физически эти модификации могут включать изменение геометрии вала (трубчатое или сплошное), использование эластомерного соединения для увеличения демпфирования или добавление/снятие маховика с трансмиссии. Если модификация компонентов трансмиссии невозможна, анализ может все же дать информацию относительно лучшего местоположения, чтобы использовать перегрузку крутящего момента или ограничивающее устройство. Поскольку изменения могут повлечь за собой значительные временные и технические затраты, важно, чтобы моделирование крутильной динамики было точным и эффективным. По возможности, лучше всего использовать эмпирические данные измерений крутящего момента в полевых условиях для проверки и нормализации модели кручения.
Прогностические методы
Прямое измерение крутящего момента является наилучшим методом устранения неопределенности в расчетах собственной частоты и вынужденного отклика, оценки воздействия эксплуатационных изменений (нагрузки и/или скорости) и регистрации переходных процессов, которые могут снизить надежность системы. Для получения полезных данных важно учитывать место измерения крутящего момента. Большие инерции, имеют тенденцию изолировать ведущую и ведомую стороны трансмиссии от переходных воздействий крутящего момента, поскольку они действуют как маховики. Измерения должны проводиться в месте, где имеется достаточное угловое отклонение, чтобы получить сигнал в датчике крутящего момента. Это означает, что короткие сплошные секции вала могут не сильно отклоняться под нагрузкой. Наконец, для датчиков крутящего момента, таких как тензодатчики, необходимо знать геометрию сечения вала (и свойства материала), где установлен датчик, чтобы можно было рассчитать крутящий момент на основе измеренной деформации. Сложные геометрии затруднят расчет зависимости между напряжением и крутящим моментом.
Часто, электрический крутящий момент, измеряемый на двигателе, используется для определения крутящего момента на выходе трансмиссии. Хотя этого обычно достаточно для установившегося крутящего момента, электрический крутящий момент на двигателе недостаточно быстро реагирует на пики крутящего момента, возникающие на стороне привода трансмиссии. В двигателях с частотно-регулируемым управлением источником крутильных колебаний обычно является привод. Частотное регулирование используется для управления скоростью двигателя посредством манипулирования частотой их выходного сигнала путем выпрямления входящего переменного тока в постоянный ток, а затем с помощью различных методов (обычно широтно-импульсной модуляции) для воссоздания формы выходного сигнала переменного тока и напряжения. В то время как более новые ЧРП производят более плавные выходы и уменьшают амплитуду связанных пульсаций крутящего момента, замечено, что более жесткое регулирование скорости может вызывать другие нестабильности, поскольку привод пытается быстро скорректировать крутильные пульсации, принимая их за изменения нагрузки. Более жесткое регулирование скорости также проблематично, когда двигатели приводят в движение большие массы (вентиляторы большого диаметра, коробки передач и т.д.), которые по своей природе не реагируют на внезапные изменения скорости, поскольку они, как правило, действуют как маховики.
Изменения формы выходной частоты могут привести к соответствующим колебаниям крутящего момента. Как правило, пульсация крутящего момента для обеспечения плавной работы не должна превышать 1%. Казалось бы, логично, что обратную связь от привода можно использовать для измерения переходных моментов; однако данные крутящего момента обычно записываются только при частоте 10 Гц (выборок/секунда), что слишком медленно для захвата переходных процессов без усечения пиков формы сигнала.
Временные события, такие как удары, пуски и сбои процессов, могут привести к пикам крутящего момента, чей первый (и самый большой амплитудный) цикл вибрации происходит всего за несколько миллисекунд. Для адекватного захвата формы волны без усеченных пиков частота дискретизации обычно должна составлять не менее 500 Гц (выборок в секунду).
Доступно несколько распространенных технологий, способных измерять переходный крутящий момент: системы фазового смещения, тензодатчики и оптические датчики. Сравнение различных технологий показано в таблице 1, где «Х» указывает, что технология подходит для конкретных критериев или условий, перечисленных в первом столбце. Выбор конкретной технологии во многом зависит от предполагаемого использования и применения.
Цифровой сигнал от передатчика передается по беспроводной связи на приемник, который может обеспечивать различные аналоговые выходы (4-20 мА, 0-10 В постоянного тока и т.д.), которые могут быть записаны. Усиление (множитель) и смещение применяются к аналоговому выходному сигналу для определения значения крутящего момента на основе известных размеров материала и механических свойств вращающегося вала/муфты.
Системы фазового смещения применяют в зубчатых передачах, которые генерируют импульс каждый раз, когда зуб шестерни проходит чувствительный элемент. Разница во времени (определяемая наборами противоположных датчиков) между зубьями на ведущем и ведомом вращающихся шестерен используется для определения величины углового отклонения, которое существует между колесами известной жесткости, и, следовательно, передаваемого крутящего момента. Пример сигналов переменного напряжения, создаваемых двумя зубчатыми колесами, проходящими через датчики, показан на рисунке 19. Эти системы являются хорошим выбором с точки зрения непрерывности работы, где требуется высокая степень точности для оптимизации процесса и проверки производительности. Системы измерения крутящего момента фазовым смещением обычно устанавливаются в турбомашинных установках и не применяются для оборудования с низкой скоростью (<500 об/мин).
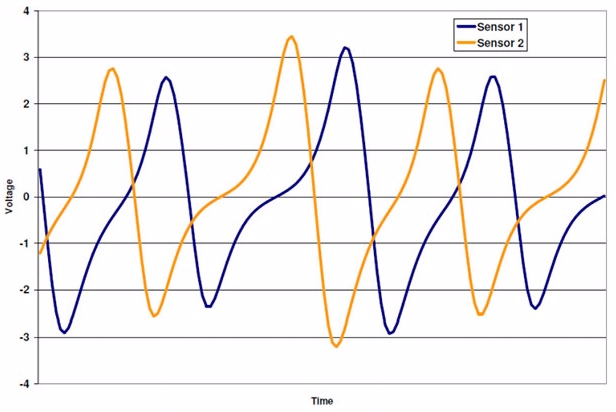
В оптических системах обычно используются полосовые или «зебра-ленточные» кодеры, прикрепленные к вращающемуся валу, и оптический кодировщик для обнаружения изменений цвета при прохождении ленты мимо кодировщика. Оптические системы являются еще одним вариантом для временного измерения крутящего момента, но имеют некоторые ограничения - смазка/масло могут препятствовать работе оптического датчика, тепло ухудшает качество клея. Кроме того, необходимо разработать алгоритмы обработки сигналов, чтобы устранить перекрытие каждого сегмента ленты с полосами, чтобы избежать ложных измерений.
Тензодатчики, которые состоят из электрических резисторов, ориентированных по мосту Уитстона, установлены на вращающемся валу или муфте, подключены к передатчику сигнала и питаются индуктивно или от батарей. Для измерений переходного крутящего момента необходим выбор системы с адекватной частотой дискретизации, поскольку некоторые системы предназначены только для прерывистых измерений.
Таблица 1. Сравнение систем измерения крутящего момента.
Пусконаладка/диагностика | ||||
Непрерывность | ||||
Низкая скорость | ||||
Высокая скорость | ||||
Агрессивная среда | ||||
Боковое перемещение вала | ||||
Относительная стоимость |
Желаемая длина непрерывного измерения - это первый критерий, который следует учитывать при выборе системы измерения крутящего момента. Значительных затрат можно избежать, выбрав простую систему. Зачастую, измерения крутящего момента требуются только временно для проверки теоретических моделей, ввода в эксплуатацию или диагностики. В этих случаях обычно используются тензодатчики. Пример временной установки тензодатчика показан на рисунке 20. Измеритель и радиопередатчик прикреплены к вращающемуся валу, в данном случае на промвставке. Латунная кольцевая антенна установлена по окружности вала и принимает радиочастотный сигнал от передатчика. В определенных конструкциях этот тип установки может также служить для подачи индуктивной мощности на передатчик, устраняя необходимость в батареях. На рисунке 21 показана постоянная установка с использованием аналогичной системы телеметрии с тензодатчиком. Электронные компоненты на вращающемся валу защищены резиновыми и металлическими корпусами, установленными на валах. Альтернативный корпус, используемый для защиты датчиков и передатчика, показан на рисунке 22. Эта конкретная система не требует кольцевой антенны и передает сигнал по беспроводной связи в приемник и модуль обработки. В высокоскоростных машинах монтаж электроники на вращающемся валу может привести к дисбалансу, создавая другие проблемы. В этих случаях узел преобразователя, установленный на валу, должен быть уравновешен массой, установленной на 180 градусов. В машинах, чувствительных к дисбалансу, компоненты должны быть динамически сбалансированы после установки телеметрической системы. Полые валы допускают возможность установки датчиков и проводки по внутреннему диаметру, что обеспечивает дополнительную защиту и крепление проводки (рисунок 23).
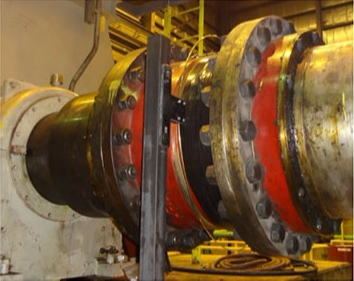
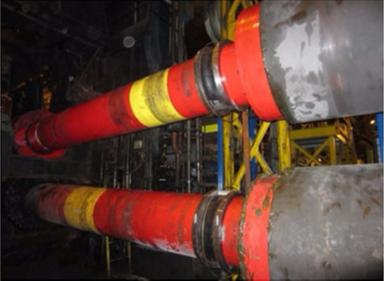
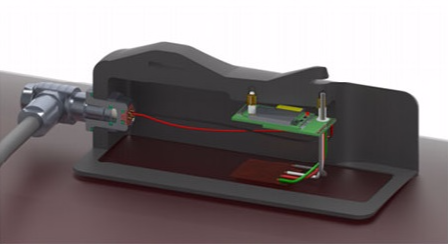
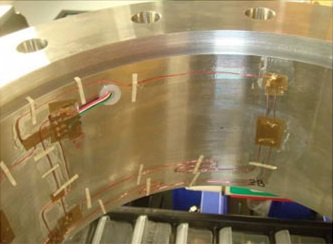
Как и в случае линейной вибрации, форма временного сигнала и спектр БПФ данных крутящего момента предоставляют аналитику информацию, необходимую для определения опасности крутильных колебаний и их источника. Форма временного сигнала может быть напрямую связана с напряжениями, что позволяет оценить надежность трансмиссии с точки зрения усталости и коэффициентов безопасности при выходе.
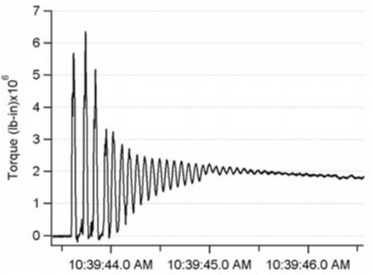
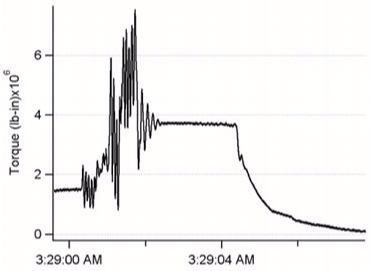
Спектральные данные предоставят аналитику информацию о частотах, присутствующих в осциллограмме. Условия процесса и угловые зазоры, такие как люфт или износ, могут вызвать крутильные колебания внутри оборудования; тем не менее, чаще всего можно увидеть собственные частоты системы в спектральных данных. Это частота, на которой вал колеблется после ударной нагрузки или когда рабочая скорость совпадает с собственной частотой кручения. В то время как для трансмиссии существует бесконечное число собственных частот кручения, вполне вероятно, что наблюдаются только первые две. Собственные частоты высших порядков гораздо менее энергичны и более трудны для возбуждения. Спектральные данные могут быть использованы для проверки теоретических расчетов собственных крутильных частот, чтобы можно было правильно оценить изменения рабочих скоростей для избежания неблагоприятных условий. Кроме того, эмпирические данные позволят «нормализовать» математическую модель трансмиссии, обеспечивая уверенность в оценке любых изменений (модернизация двигателя, изменения крепления и т.д.) в предлагаемой механической передаче для повышения надежности и снижения риска непредвиденных проблем.
Для машин, которые подвержены крутильной вибрации (либо из-за резонанса на рабочих скоростях, либо от ударных нагрузок), интеграция измерений крутящего момента с радиальной и осевой вибрацией от вихретоковых датчиков или установленных на корпусе акселерометров может обеспечить комплексную систему мониторинга состояния. Во-первых, измерения крутящего момента можно использовать для запуска записи вибрационных данных на основе предикатов. Поскольку легкие и прерывистые нагрузки могут создавать трудности при сборе полезных данных о вибрации, измерения крутящего момента могут помочь аналитикам различить данные, представляющие неисправность, и данные, являющиеся только характеристикой работы оборудования. Чтобы проиллюстрировать это, на рисунке 26 показаны данные из онлайн системы контроля вибрации, которая одновременно записывает данные о крутящем моменте и вибрации в оборудовании для металлопроката. На рисунке показаны периодически записываемые спектральные данные от установленного на корпусе редуктора акселерометра. Измерения вибрации для слабо нагруженных (синий) и полностью нагруженных (фиолетовый) условий были инициированы сигналом от системы измерения крутящего момента, установленной на выходном валу коробки передач. Разница в спектральных данных очевидна, но без знания передаваемого крутящего момента было бы трудно определить, вызвано ли увеличение вибрации нагрузкой или неисправностью в оборудовании.
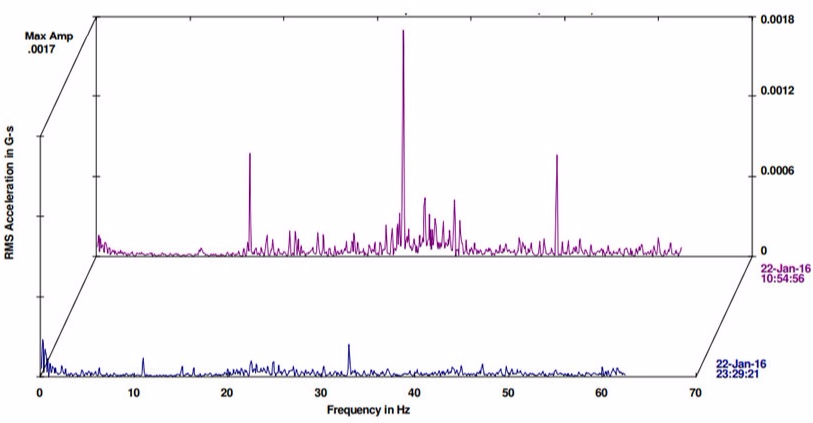
В дополнение к использованию данных крутящего момента для определения влияния нагрузки на измерения вибрации, измерения крутящего момента также могут использоваться для предупреждения операторов о неблагоприятных условиях. Когда амплитуда крутильных колебаний измеряется непрерывно, можно подсчитать количество случаев, когда амплитуда превышает определенный порог, что позволяет предпринять корректирующие действия до того, как произойдет усталостное разрушение. Эти пороговые значения могут быть определены из анализа напряжений компонента, передающего крутящий момент, или на основе кратного номинального рабочего крутящего момента, который будет указывать на ненормальные условия. Пример тенденции крутящего момента показан на рисунке 27, который включает в себя несколько пиков крутящего момента с большой амплитудой.
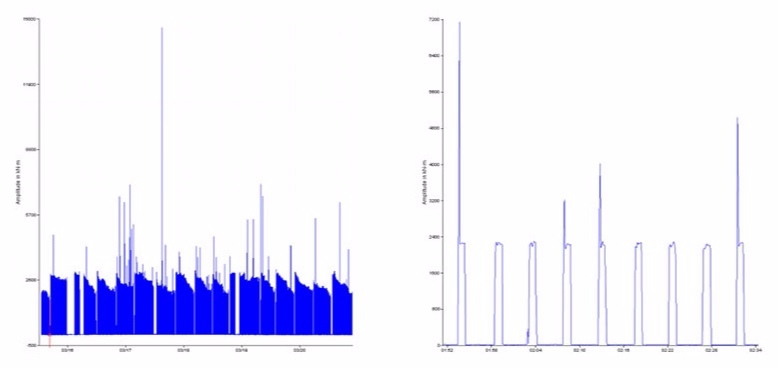
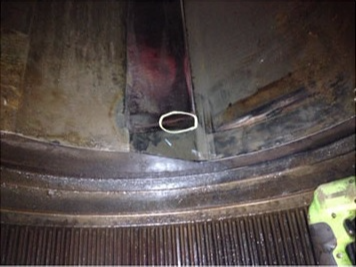
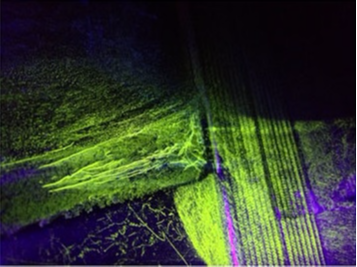
Измерения побудили обслуживающий персонал разобрать компоненты для осмотра и ремонта, в процессе чего были обнаружены небольшие трещины. Идентификация этих усталостных трещин оставалась бы скрытой без измерений кратковременных моментов до дальнейшего распространения или разрушения. Кроме того, замена поврежденного компонента до дальнейшего распространения трещин может значительно сократить время простоя оборудования, связанное с полным разрушением этого компонента.
Заключение
Вредные крутильные колебания могут возникать из-за условий работы и переходных процессов или могут быть просто присущи конструкции трансмиссии. Поскольку большая часть оборудования не оборудована системами для измерения этих вибраций, отказ часто является первым признаком их наличия. В некоторых случаях профилактические (основанные на времени) меры могут быть использованы для выявления наличия крутильных колебаний, но эти методы имеют ограниченную эффективность при определении серьезности и источника.
Трансмиссии, восприимчивые к крутильным колебаниям, используются во многих отраслях промышленности и включают тихоходное оборудование, а также турбомашины. Стандарты API (617:2002 и 684:2005) предоставляют руководство по моделированию кручения, расчетам собственных частот и рекомендации по избежанию резонансных условий. К сожалению, эти стандарты не используются в той степени, в которой они могут использоваться в других отраслях, чтобы избежать сбоев из-за крутильных колебаний.
Методы прогнозирования, которые включают измерение и анализ переходного крутящего момента, могут применяться на временной или постоянной основе. Измерения крутящего момента могут быть использованы для оценки факторов стрессоустойчивости для новых конструкций, увеличения пропускной способности и других модификаций трансмиссии. Кроме того, непрерывный мониторинг крутящего момента может использоваться для выявления неблагоприятных условий, которые могут вызвать усталостные трещины в компонентах трансмиссии, которые трудно обнаружить с помощью обычного анализа вибрации.