Features of balancing at a rotation frequency of 220 Hz
In the opening lines, I want to sincerely thank Evgenii Ochkasov for providing the material for this article.
Instead of a preface.
On one of the rare sunny days under the sky of Bologoye, I was sitting at my mom's house enjoying her magnificent pancakes with fragrant raspberry jam, washing them down with currant and mint tea. Mom, standing by the stove, looked at me, smiled, and said:
'You look so much like Kurchatov with that beard.'
Slightly choking on my tea from such a comparison, I coughed and replied with a smile:
'You know, just the day before yesterday, my boss offered me a choice between two research institutes, one of which is the Kurchatov Institute, and I decided to work there starting this Thursday.'
'Really? How interesting! And what will you be doing there, my son?'
'I'll be balancing a vacuum pump for a rocket engine.'
'Wow! Good luck!'
On Thursday, after a fairly tedious procedure of obtaining passes for myself and the equipment, I walked through the territory of the research institute with two colleagues, recounting how my mom said I looked like Igor Vasilyevich. The senior of the two, Alexander, said:
'You have a very smart mom if she knows who Igor Vasilyevich is.'
'That's one way to put it, but that's not the point,' I replied. 'I'm just from the city next to the nuclear power plant and I live on Kurchatov Avenue. Everyone in our city knows him.'
And all three of our faces stretched into a synchronous smile...
Then, out of habit, I started asking leading questions about what, why, and how, to get to the essence of the work. And that's when the client mentioned that when the unit operates at 160 Hz, it behaves one way, but when it reaches 200 Hz and above, the entire set of monitoring and metering equipment starts shaking so much that it becomes worrisome, and the sound becomes unpleasant.
'What are its operational speeds?' I asked.
'From 190 to 220 Hz,' Alexander replied.
Understanding that surprises might await me at these speeds, I contacted Evgenii Stepanovich and shared my concerns:
'...there's a situation. I recall hearing somewhere that measurements are done in microns up to 200 Hz, but above that, they need to be measured in millimeters per second.
'Here's the deal, lad: measure in both, and then publish the results. I think it might be useful not just for you.'
And that's what I did.
So, the vacuum pump is part of a rocket engine. In the photo provided of the overall installation, it's highlighted in orange."
The unique feature of its balancing was that the phase detector read through glass, and I was concerned that it would glare and the measurement results would be unsatisfactory.
But it turned out that I was facing another problem, which I'll mention a bit later. I installed two sensors at a 90-degree angle on the lower pump flange, with one of them oriented towards the exhaust pipeline.
When the client turned the pump on, he began observing the acceleration of the unit on the instrument display. It took a long time for the vacuum to build up; the machine revved up to 170 Hz for almost half an hour. When it stabilized, Alexander asked, 'Is this sufficient, or do you want to see what happens at 190 Hz?'
'Let's not waste time; we'll balance it at 170 first, then consider going higher.' – I said
As a result, the balancing outcome and the values of the rotational component of vibration velocity and vibration displacement are presented in the table.
Later, on the following day, the balancing process continued, and we started reaching speeds higher than 200 Hz. As Alexander explained, this was the minimum operating speed for the setup. As the speed increased, at around 190 Hz, a noise emerged, which became fluctuating as the rotation frequency increased, and at approximately 198 Hz, the phase detector signal suddenly disappeared. No matter how much I tried or rotated the marker, the phase information wouldn't return. We had to stop and check if the reflective marker had been sucked in by the deep vacuum. However, it turned out that it hadn't, and when we slowed down to 160 Hz, the signal reappeared, and the phase measurement resumed. It then occurred to me something I had heard from the instrument developer before—specifically, that at high speeds, a marker that's too narrow can slip past the measurements, requiring a wider one. After stopping the setup and depressurizing it, the marker was replaced with a new one, twice as wide as the previous. We restarted the process. At 220 Hz, the machine's rotations stabilized. This time, the balancing results appeared as follows:
What was notable was that on the balanced machine, the phase of vibration velocity remained stable, while the phase of vibration displacement began to fluctuate significantly, changing by more than 100 degrees. This ruled out the possibility of further calculating corrective loads based on vibration displacement parameters.
Even after installing balancing mass, an extraneous noise continued to trouble Alexander. He mentioned that another backup pump didn't behave or make noise like this one and suggested continuing the balancing process despite the vibration velocity component reading 0.05 mm/s. I realized that imbalance might not be the issue anymore and captured the enveloping spectrum to check for bearing defects. True to form, approximately 0,4 times the rotational frequency, precisely at 91,88 Hz, a peak with a modulation depth of 27,2% was detected—the so-called 'bearing cage peak'.
This is what I shared with the client, saying that it seems there's an issue with the bearing and it's about time to replace it.
When I was writing the report at home, a surprise awaited me. Specifically—in polar coordinates, the data from the latest run looked like this:
So, the phase wasn't just changing randomly; it was changing along a single axis. I remembered that the pressure pipeline was positioned at approximately the same angle to the sensor, and it seemed that it was causing the setup to oscillate. Consequently, I included a recommendation in the report: to install a flexible hose between the pipeline and the pump.
That's all for now. If anyone's interested in my scribblings or, on the contrary, has questions, feel free to write them in the comments.
Опыт интересный. Можно подробнее о требованиях к вибрации/балансировке и процессе "установки" грузов?
Про требования можно отдельный рассаз запилить, но если кратко, там же по дороге от кпп к установке я поведал историю о том как балансировал привод мясорубки у которого на шкиве было 4 балансировочных отверстия, причем установив в одно из них шпильку я увидел, что вектор направлен четко в ноль, как в лузу шар) и стал потихоньку эту шпильку обтачивать на наждаке. так дзинь дзинь, вкрутил, проверил, опять, дзинь дзинь, проверил. в итоге с 3,1 мм/с вибрация упала до 0,06 мм/с и механик азиат, увидев на дисплее 0,06 воскликнул: Вах! Мэньши нуля! Заказчик ухмыльнулся и то же попросил, мэньши нуля. Вот прям так и сказал, до второго знака после запятой, а лучше было бы превзойти себя и сделать 0,05 мм/с. И как видите мне это удалось. А груза устанавливались в штатные резьбовые отверстия М4 расположеные в рабочем колесе
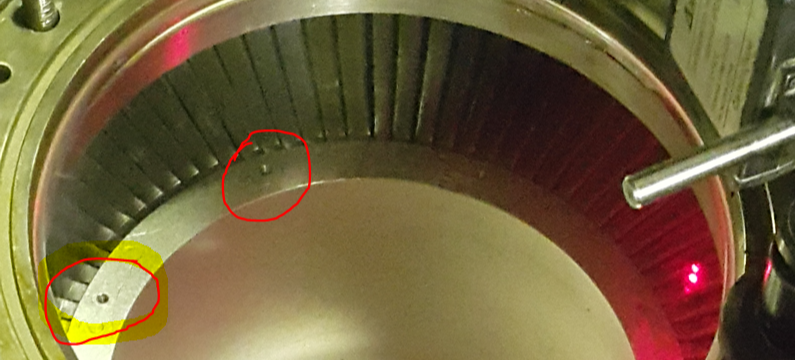
сначала мы вкручивали шпильки из нержавейки, а затем из алюминиевого сплава. Самый маленький груз весил 0,11 грамм. В итоге, уже по достижению 0,05 мм/с, Заказчик снова попросил рассчитать массу груза и угол, мол он потом его сам изготовит и поставит (т.к. надо было уходить, а машина как я сказал выбегала с пол-часа плюс надо было срывать вакуум и т.д. Я сделал. груз требовался массой 0,017 грамма и я только ухмыльнулся, желая удачи в его изготовлении. Кстати, мне реально пришлось натянуть сову на глобус и выдумать нормы для этой машины. Итоговая таблица после балансировки выглядела вот как
insolution bisindolylmaleim 1pc x 1ml - купить онлайн в интернет-магазине химмед
Tegs: methyl hydrogen malonate 96% - купить онлайн в интернет-магазине химмед
methyl hydrogen succinate, 95% - купить онлайн в интернет-магазине химмед
methyl hydrogen succinate, 95% - купить онлайн в интернет-магазине химмед
insolution casein kinase i 1pc x 1mg - купить онлайн в интернет-магазине химмед https://chimmed.ru/products/insolution-casein-kinase-i-1pc-x-1mg-id=4142752
human usp32 gene orf cdna clone expression plasmid - купить онлайн в интернет-магазине химмед
Tegs: latanoprost - купить онлайн в интернет-магазине химмед
latanoprost - купить онлайн в интернет-магазине химмед
latanoprost - купить онлайн в интернет-магазине химмед
human usp32 gene orf cdna clone expression plasmid, c myc tag - купить онлайн в интернет-магазине химмед https://chimmed.ru/products/human-usp32-gene-orf-cdna-clone-expression-plasmid-c-myc-tag-id=1620067
l methionine, reagent grade, 98% hplc - купить онлайн в интернет-магазине химмед
Tegs: mouse 1810037i17rik gene orf cdna clone expression plasmid - купить онлайн в интернет-магазине химмед
mouse 1810037i17rik gene orf cdna clone expression plasmid, c flag tag - купить онлайн в интернет-магазине химмед
mouse 1810037i17rik gene orf cdna clone expression plasmid, c ha tag - купить онлайн в интернет-магазине химмед
l methionine, reagent grade, 98% hplc - купить онлайн в интернет-магазине химмед https://chimmed.ru/products/l-methionine-reagent-grade-98-hplc-id=3970086
kromasil 10 amycoat column - купить онлайн в интернет-магазине химмед
Tegs: napsin a napsa antibody, rabbit pab, antigen affinity purified - купить онлайн в интернет-магазине химмед
napsin a napsa antibody, rabbit pab, antigen affinity purified - купить онлайн в интернет-магазине химмед
napsin a napsa antibody, rabbit pab, antigen affinity purified - купить онлайн в интернет-магазине химмед
kromasil 10 amycoat column - купить онлайн в интернет-магазине химмед https://chimmed.ru/products/kromasil-10-amycoat-column-id=269980
immunochemicals antibodies anti aging preventive medicine - купить онлайн в интернет-магазине химмед
Tegs: mouse fam126b gene orf cdna clone expression plasmid, c myc tag - купить онлайн в интернет-магазине химмед
mouse fam126b gene orf cdna clone expression plasmid, c ofpspark tag - купить онлайн в интернет-магазине химмед
mouse fam126b gene orf cdna clone expression plasmid, n gfpspark tag - купить онлайн в интернет-магазине химмед
immunochemicals antibodies anti aging preventive medicine - купить онлайн в интернет-магазине химмед https://chimmed.ru/products/immunochemicals---antibodies-anti-aging---preventive-medicine-id=5030513
iron foil, 0 127mm 0 005in thick 99 5% metals basis - купить онлайн в интернет-магазине химмед
Tegs: mission human kinase epha2 sirna2 - купить онлайн в интернет-магазине химмед
mission human kinase epha2 sirna3 - купить онлайн в интернет-магазине химмед
mission human kinase epha3 sirna1 - купить онлайн в интернет-магазине химмед
iron foil, 0 1mm 0 004in thick 99 99% metals basis - купить онлайн в интернет-магазине химмед https://chimmed.ru/products/iron-foil-01mm-0004in-thick-9999-metals-basis-id=4639550
4 bromo 2 difluoromethoxy pyridine - купить онлайн в интернет-магазине химмед
Tegs: 4 chloro 7h pyrrolo 2, 3 d pyrimidine - купить онлайн в интернет-магазине химмед
4 chloro 7h pyrrolo 2, 3 d pyrimidine - купить онлайн в интернет-магазине химмед
4 chloro 7h pyrrolo 2, 3 d pyrimidine - купить онлайн в интернет-магазине химмед
4 bromo 2 difluoromethyl 1 fluorobenzene - купить онлайн в интернет-магазине химмед https://chimmed.ru/products/4-bromo-2-difluoromethyl-1-fluorobenzene-id=4727104
4 chlorophenyl 2 phenyl 1, 3 thiazol 5 yl methanone - купить онлайн в интернет-магазине химмед
Tegs: 6 bromofuro 3, 2 b pyridin 2 yl methanol - купить онлайн в интернет-магазине химмед
6 bromofuro 3, 2 b pyridin 2 yl methanol - купить онлайн в интернет-магазине химмед
6 bromofuro 3, 2 b pyridin 2 yl methanol - купить онлайн в интернет-магазине химмед
4 chlorophenyl 2 phenyl 1, 3 thiazol 5 yl methanone - купить онлайн в интернет-магазине химмед https://chimmed.ru/products/4-hlorfenil2-fenil-13-tiazol-5-ilmetanon-id=8520557
белок recombinant human cd109, cf - купить онлайн в интернет-магазине химмед
Tegs: 1 4 chloro 2 methoxy 5 methylphenyl 5 pyridin 4 yl 1h 1, 2, 3 triazole 4 carboxylic acid - купить онлайн в интернет-магазине химмед
1 4 chloro 2 methoxy 5 methylphenyl 5 ethyl 1h 1, 2, 3 triazole 4 carboxylic acid - купить онлайн в интернет-магазине химмед
1 4 chloro 2 methoxybenzoyl 4 3 phenyl 1, 2, 4 oxadiazol 5 yl methyl piperidine - купить онлайн в интернет-магазине химмед
белок recombinant human cd14 - купить онлайн в интернет-магазине химмед https://chimmed.ru/products/belok-recombinant-human-cd14-id=375617
2 chloro 5 methylpyridin 3 yl methanamine min 95% - купить онлайн в интернет-магазине химмед
Tegs: 4 1, 1 dioxo 2 thiazinan 2 yl benzoic acid - купить онлайн в интернет-магазине химмед
4 1, 1 dioxothiomorpholino benzaldehyde - купить онлайн в интернет-магазине химмед
4 1, 1 dioxothiomorpholino benzaldehyde - купить онлайн в интернет-магазине химмед
2 chloro 5 nitrophenyl 4 methylphenyl methanone 95% - купить онлайн в интернет-магазине химмед https://chimmed.ru/products/2-chloro-5-nitrophenyl4-methylphenylmethanone-95-id=4555845
spectinomycin dihydrochloride pentahydra - купить онлайн в интернет-магазине химмед
Tegs: r piperidin 3 ol - купить онлайн в интернет-магазине химмед
r piperidin 3 ol - купить онлайн в интернет-магазине химмед
r piperidine 2 ylmethanol - купить онлайн в интернет-магазине химмед
spectinomycin dihydrochloride pentahydra - купить онлайн в интернет-магазине химмед https://chimmed.ru/products/spectinomycin-dihydrochloride-pentahydra-id=4085285
Undertaking a study of the complex sphere of sartorial expression illustrates a tapestry of Coach handbags
factors that determine as well as what we wear additionally the way we view individual expression and group dynamics. Figuring out the chronological progression of various styles provides a significant perspective for the purpose of appreciating the rotational aspect of vogues, in which past influences occasionally are revived with current enhancements. Paying close attention to the delicate interaction linking color psychology, advancements in fabrics, as well as the essentials of clothing creation and structure facilitates a more insightful means of interacting with ARKET Damen
creating a harmonious array of clothing. Furthermore, the surge in green and socially accountable actions within the fashion industry underscores a remarkable transformation moving towards increased accountability and a more profound awareness concerning the wider implications of our sartorial choices. In the end, fashion endures as GAP Sweats
a vibrant expression of the spirit of the times and presents a constant avenue in order to finding one's unique voice as well as the joyful act of displaying our unique characters within our communities.
4 2 ethoxyethoxy aniline - купить онлайн в интернет-магазине химмед
Tegs: methyl 2 amino 3 chlorobenzoate - купить онлайн в интернет-магазине химмед
methyl 2 amino 3 chlorobenzoate - купить онлайн в интернет-магазине химмед
methyl 2 amino 3 chloropropanoate hydrochloride - купить онлайн в интернет-магазине химмед
4 2 ethoxyethoxy aniline - купить онлайн в интернет-магазине химмед https://chimmed.ru/products/4-2-etoksietoksianilin-id=8560075
rna polymerase ii polr2a p ser5 antibody ctd 4h8 dylight 650 - купить онлайн в интернет-магазине химмед
Tegs: pcdha8 antibody - купить онлайн в интернет-магазине химмед
pcdha8 overexpression lysate denatured - купить онлайн в интернет-магазине химмед
pcdha8 recombinant protein antigen - купить онлайн в интернет-магазине химмед
rna polymerase ii polr2a p ser5 antibody ctd 4h8 dylight 680 - купить онлайн в интернет-магазине химмед https://chimmed.ru/products/rnk-polimeraza-ii-polr2a-p-ser5-antitela-ctd-4h8-dylight-680-id=6855943
5 dimethylamino thiophene 2 carbaldehyde - купить онлайн в интернет-магазине химмед
Tegs: 2 amino 4 4 butylphenyl thiophene 3 carbonitrile - купить онлайн в интернет-магазине химмед
2 amino 4 4 butylphenyl thiophene 3 carbonitrile - купить онлайн в интернет-магазине химмед
2 amino 4 4 butylphenyl thiophene 3 carboxamide - купить онлайн в интернет-магазине химмед
5 dimethylaminomethylene 2, 2 dimethyl - купить онлайн в интернет-магазине химмед https://chimmed.ru/products/5-dimethylaminomethylene-22-dimethyl-id=3893679
cyclohexylhydrazine hydrochloride - купить онлайн в интернет-магазине химмед
Tegs: 7 trifluoromethyl 2, 3 dihydroquinazolin 4 1h one - купить онлайн в интернет-магазине химмед
7 trifluoromethyl 3, 4 dihydro 2h naphthalen 1 one - купить онлайн в интернет-магазине химмед
7 trifluoromethyl 3, 4 dihydro 2h naphthalen 1 one - купить онлайн в интернет-магазине химмед
cyclohexylhydrazine dihydrochloride - купить онлайн в интернет-магазине химмед https://chimmed.ru/products/ciklogeksilgidrazin-digidrohlorid-id=8555660
2 4 bromophenyl 2, 2 difluoroacetic acid - купить онлайн в интернет-магазине химмед
Tegs: anti mll2 n terminal - купить онлайн в интернет-магазине химмед
anti mll3 - купить онлайн в интернет-магазине химмед
anti mll3 c term - купить онлайн в интернет-магазине химмед
2 4 bromophenyl 2, 2 difluoroacetic acid - купить онлайн в интернет-магазине химмед https://chimmed.ru/products/2-4-bromophenyl-22-difluoroacetic-acid-id=4420776
3 3, 5 dimethyl 1h pyrazol 1 yl 2 methylpropanethioamide - купить онлайн в интернет-магазине химмед
Tegs: esirna human hspa8 esirna1 - купить онлайн в интернет-магазине химмед
esirna human hspa9b esirna1 - купить онлайн в интернет-магазине химмед
esirna human hspa9b esirna1 - купить онлайн в интернет-магазине химмед
3 3, 5 dimethyl 1h pyrazol 1 yl 2 methylpropanethioamide - купить онлайн в интернет-магазине химмед https://chimmed.ru/products/3-35-dimethyl-1h-pyrazol-1-yl-2-methylpropanethioamide-id=4378185
cyclopropyl pyridin 3 ylmethyl amine - купить онлайн в интернет-магазине химмед
Tegs: 7 chloro 3 methyl 2 piperazin 1 yl quinoline hydrochloride - купить онлайн в интернет-магазине химмед
7 chloro 3 methyl 4, 5 dihydro 1h benzo b 1, 4 diazepin 2 3h one - купить онлайн в интернет-магазине химмед
7 chloro 3 methylbenzo b thiophene 2 carboxylic acid - купить онлайн в интернет-магазине химмед
cyclopropyl pyridin 3 ylmethyl amine - купить онлайн в интернет-магазине химмед https://chimmed.ru/products/ciklopropil-piridin-3-ilmetil-amin-id=8553508
ethyl 5 bromo 6 chloro 1h indole 2 carboxylate - купить онлайн в интернет-магазине химмед
Tegs: abn2264 10ul anti sntf cleaved spectrin - купить онлайн в интернет-магазине химмед
abn2264 50ul anti sntf cleaved spectrin - купить онлайн в интернет-магазине химмед
abn2265 25ug anti alpha synuclein, oligo specisyn33 - купить онлайн в интернет-магазине химмед
ethyl 5 bromo 6 chloropicolinate - купить онлайн в интернет-магазине химмед https://chimmed.ru/products/ethyl-5-bromo-6-chloropicolinate--id=4712873
?r ? amino 2 pyridinepropanoic acid - купить онлайн в интернет-магазине химмед
Tegs: methyl 1 phenylcyclobutanecarboxylate - купить онлайн в интернет-магазине химмед
methyl 1 phenylcyclobutanecarboxylate - купить онлайн в интернет-магазине химмед
methyl 1 phenylethyl amine hydrochloride 95% - купить онлайн в интернет-магазине химмед
?r ? amino 3 chloro 4, 5 dihydro 5 isoxazoleethanol mixture of diastereomers - купить онлайн в интернет-магазине химмед https://chimmed.ru/products/r--amino-3-hlor-45-digidro-5-izoksazoletanol-smes-diastereomerov-id=8698310
trans 4 methylcyclohexanecarboxylicacid, 98% - купить онлайн в интернет-магазине химмед
Tegs: z l pyroglutamic acid dicyclohexylammonium salt - купить онлайн в интернет-магазине химмед
z l tic 7 oh oh - купить онлайн в интернет-магазине химмед
z l tpi oh - купить онлайн в интернет-магазине химмед
trans 4 methylcyclohexanecarboxylicacid, 98% - купить онлайн в интернет-магазине химмед https://chimmed.ru/products/trans-4-methylcyclohexanecarboxylicacid-98--id=4563185
bottle carrier for 6 bottles glass, 1l pp - купить онлайн в интернет-магазине химмед
Tegs: human il20rb protein his tag - купить онлайн в интернет-магазине химмед
human il20rb protein his tag - купить онлайн в интернет-магазине химмед
human il21 il 21 gene orf cdna clone expression plasmid codon optimized, c flag tag - купить онлайн в интернет-магазине химмед
переносной холодильник для транспортировки - купить онлайн в интернет-магазине химмед https://chimmed.ru/products/perenosnoy-holodilnik-dlya-transportirovki-id=3051611
rpmi medium 1640 1kg - купить онлайн в интернет-магазине химмед
Tegs: nqo1, human - купить онлайн в интернет-магазине химмед
nqo1, human - купить онлайн в интернет-магазине химмед
nqo2 100 ul - купить онлайн в интернет-магазине химмед
rpmi medium 1640 1kg - купить онлайн в интернет-магазине химмед https://chimmed.ru/products/rpmi-medium-1640-1kg-id=467630
1 benzyloxy 4 fluoro 2 methylbenzene - купить онлайн в интернет-магазине химмед
Tegs: 4 methylsulfonyl phenylacetic acid, 97% - купить онлайн в интернет-магазине химмед
4 methylsulfonyl phenylacetic acid 97% - купить онлайн в интернет-магазине химмед
4 methylsulfonyl phenylacetic acid 97% - купить онлайн в интернет-магазине химмед
1 benzyloxy 4 fluoro 2 methylbenzene - купить онлайн в интернет-магазине химмед https://chimmed.ru/products/1-benzyloxy-4-fluoro-2-methylbenzene--id=4351176
Tegs:
recom hu c1qbp his 25ug - купить онлайн в интернет-магазине химмед
Tegs: d ribose 2, 5 13c2 - купить онлайн в интернет-магазине химмед
d ribose 2, 5 13c2 - купить онлайн в интернет-магазине химмед
d ribose 2, 5 13c2 - купить онлайн в интернет-магазине химмед
recom hu c2 his 5ug - купить онлайн в интернет-магазине химмед https://chimmed.ru/products/recom-hu-c2-his-5ug-id=416567