The electric motor burned out. Search for a reason
Technical diagnostics and adjustment of equipment is a big responsibility. And now imagine that after the repair of the unit and the balancing performed by you, the electric motor burns out in two days. Your feelings I think at least unpleasant. And when the electricians tell you that the cause is seized bearings - it looks like a stone in your garden. You can agree and blame the unexpectedly failed bearings for everything (what happens?), Or you can conduct your own investigation and get to the bottom of the root cause.
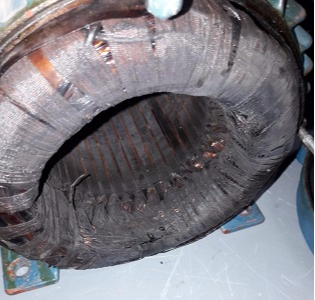
As you understand, I myself found myself in this situation. It will be about a supply fan, the balancing of which is described in [this article] (https://techdiagnost.com/en/post/18/). Since after balancing I performed vibration diagnostics of bearings and defects I didn’t see there, I don’t believe in their unexpected failure. It's time to search for information and its analysis.
From the owner of the equipment I learn the history of the ventilation unit. He once had a bearing defect. After replacing it, the fan worked for some time and the electric motor burned out. The reason is that the bearings are jammed. The electric motor was sent for rewinding, the bearings were replaced and, in fact, they called me to measure the vibration. Increased vibration, balancing and here again. That is, the problem repeated itself.
The likelihood of a mechanical defect is extremely low and one must look towards electromagnetic problems. There is nothing interesting in the vibrational spectra - only the reverse component and not about any winding closures, charred rods, etc. there is no speech. But I still didn’t like something while balancing - the rotation speed was 45.1 Hz. Frequency converter? The workshop owner assures him that he is not. Increased glide due to high load? Is the resistance in the ventilation network high (maybe some valve was not opened)? The answer is no. Wrong motor connection diagram? I am not an expert in electrical matters, and there’s no point in consulting with electricians, they have already resolved the issue - bearings.
A search for information on the Internet on the consequences of an incorrect motor connection scheme did not give concrete answers. Moreover, fierce discussions are being held on electrician forums on this issue. But most electricians react in the same way as in our company - look at the nameplate and do not bother yourself. The most important thing that we managed to draw: when connected by a "triangle", the electric motor develops maximum active power, when connected by a "star" with the same supply voltage, the active power is 3 times less. That is, we can assume the option of motor overload due to low power on the shaft. I involuntarily recalled the experience of setting up suction units (industrial ventilation to remove dust from the places of loading of bulk solids with its subsequent separation in filters or cyclones). Once upon a time, at one of the objects of the Belgorod region, the task was to carry out adjustment by air of the existing network. The project was so unsuccessful that it was necessary to block the suction line with a diaphragm by 70%. At the same time, the network resistance, and, accordingly, the load on the fan motor, has seriously increased, which in a matter of minutes led to strong heating of the electric motor - its case became simply fiery. This effect of overload on the electric motor was firmly deposited in my memory.
Therefore, we look at the passport for the electric motor: 5.5 kW, 2860 rpm, the connection diagram is a "triangle". The cable is thrown back, we go with a colleague to see the connection diagram in Borno. And there is a "star". And on the nameplate of the electric motor, a star connection diagram. Interesting. What to believe, given from the passport or from the nameplate? I think it's better to trust logic. The engine with such a connection has a minimum power on the shaft. When overloaded, the speed should fall. The electric motor must maintain revolutions, respectively increase the torque on the shaft. The stronger the load, the higher the slip should be (and we have almost 5 Hz!). All this entails an increase in currents in the windings, and, accordingly, and heat losses in it. In an article about balancing, I wrote about severe thermal deformation of the impeller of blowing the electric motor after a previous failure. Therefore, the probable cause of failure is overheating of the winding due to a star connection. That is, I would trust my passport.
These are the thoughts I shared with the staff of the workshop owner of the fan. And in response I heard that the WEG engines they burn are not the first time. On chillers there was the same trouble - due to an incorrect connection scheme indicated on the nameplates, several electric motors burned out. The plant fully admitted its mistake, apologized and replaced the engines. According to the plant, there was a marriage in the production of these same nameplates.
At this time, electricians report to the management that the electric motor is disassembled and the bearings are the cause of the failure. I, in turn, go to three identical ventilation units that are in operation.
A fan with a burned-out electric motor is called fan No. 1. The rest are No. 2, No. 3 and No. 4. I measure the vibration and temperature of the stator.
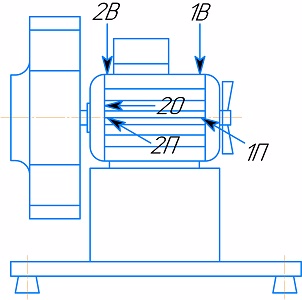
Vibration of fan No. 2 (vibration speed, mm / s):
The stator temperature is 65 ° C.
Vibration of fan No. 3 (vibration speed, mm / s):
The stator temperature is 66 ° C.
Vibration of fan No. 4 (vibration speed, mm / s):
The stator temperature is 57 ° C.
From the spectra, we determine the rotation frequencies (for fan No. 1, the spectrum is taken before balancing):
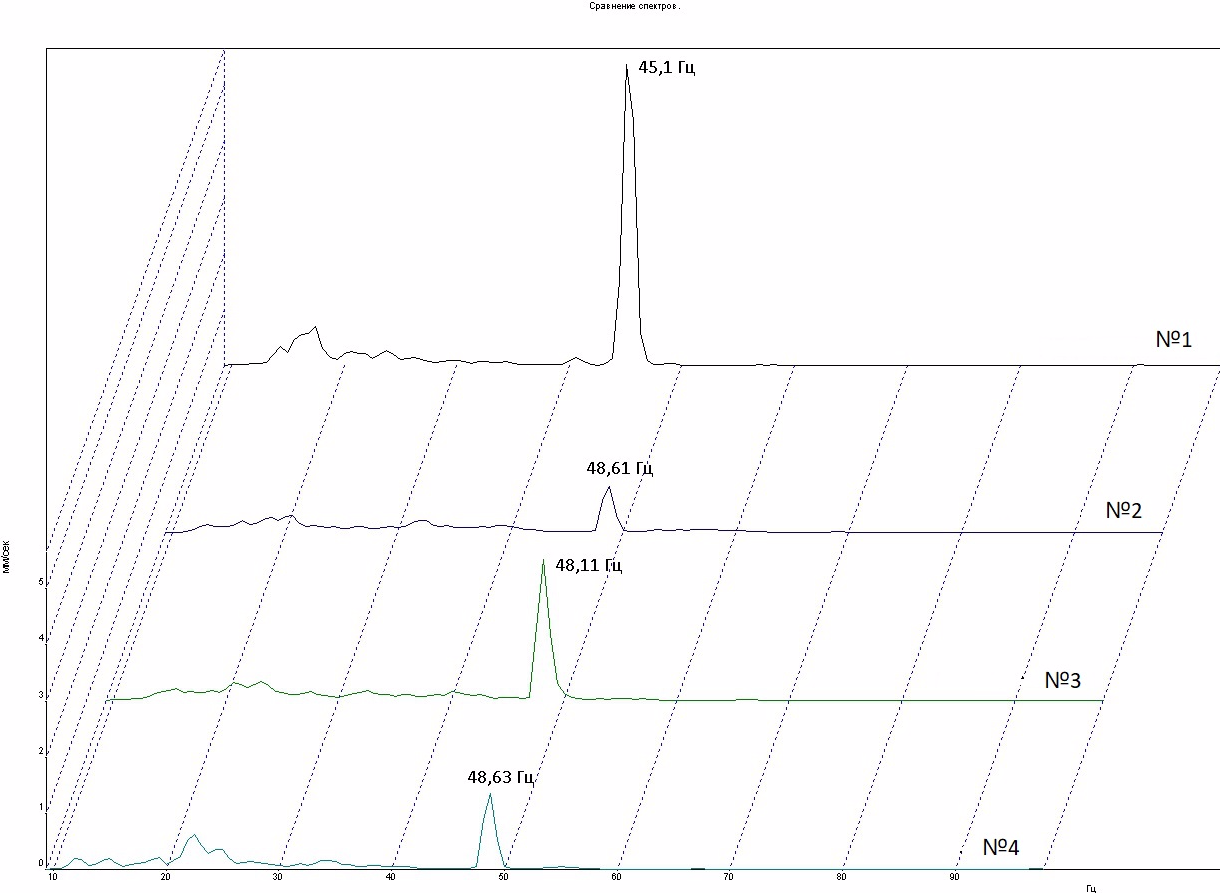
Recalculated in rpm:
As you can see, the burned fan number 1 was 200 rpm less.
Next, turn off the fan number 2, disassemble the wiring diagram and open the boron. The connection diagram is a "triangle".
The problem is identified - the nameplate, according to which the connection of the electric motor No. 1 was carried out, contains incorrect information. I compile all the information in the certificate and send it to the management of the concerned workshops.
Now you need to go to the monastery of electricians and take a look at the disassembled electric motor. Electrician version: there was a destruction of the bearing cage No. 2, the cage itself knocked out the bearing washer and damaged the stator winding.
Here is bearing No. 2 with a missing protective washer (it can be seen that the bearing is black from overheating):
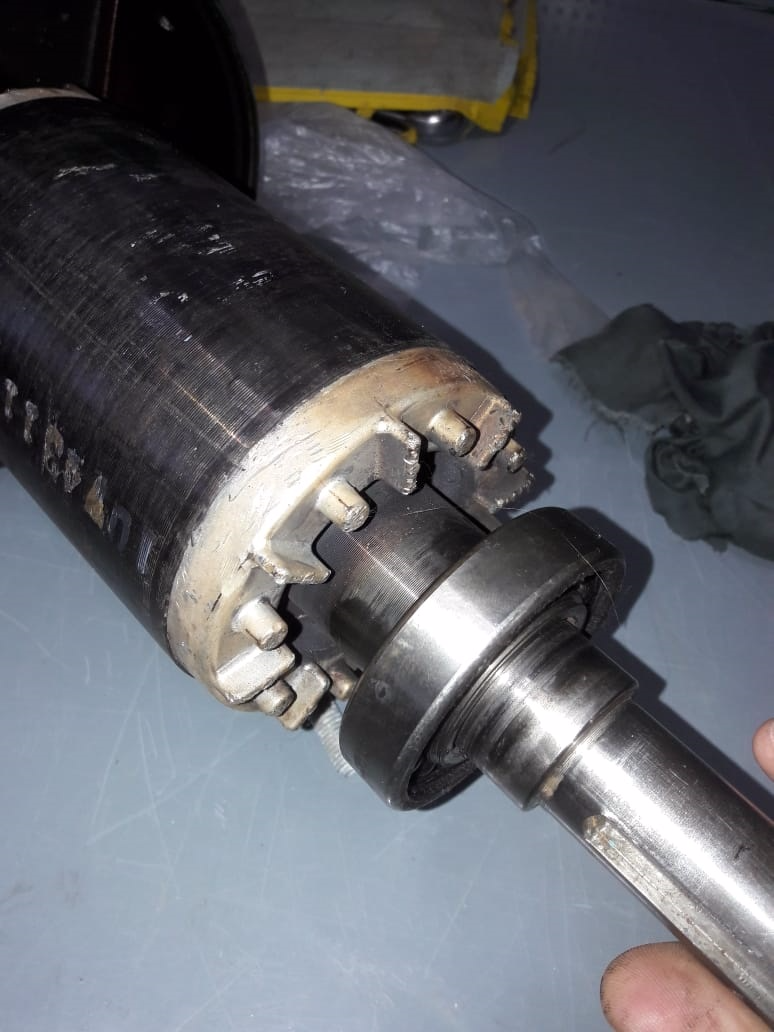
Here is the part of the cage that jumped out of the bearing (we see signs of overheating):
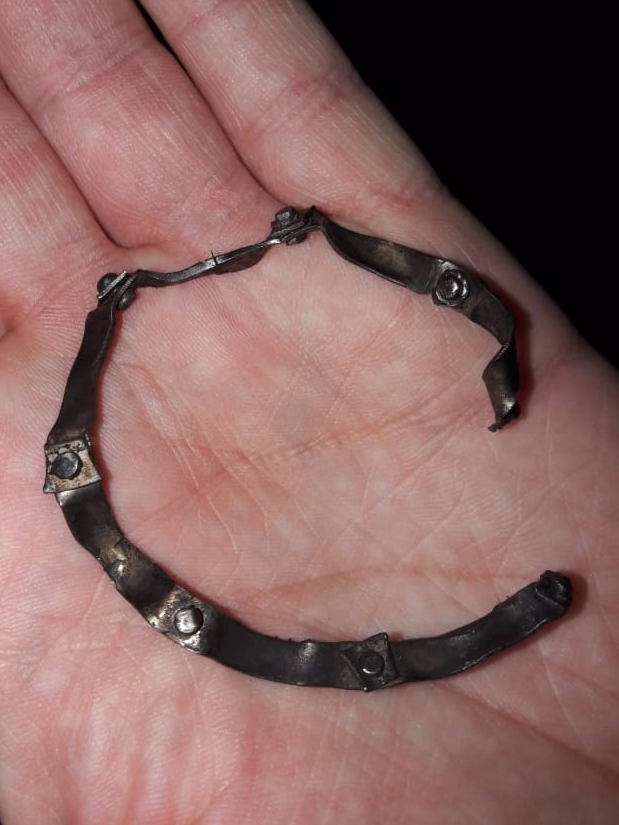
Embossed bearing washer:
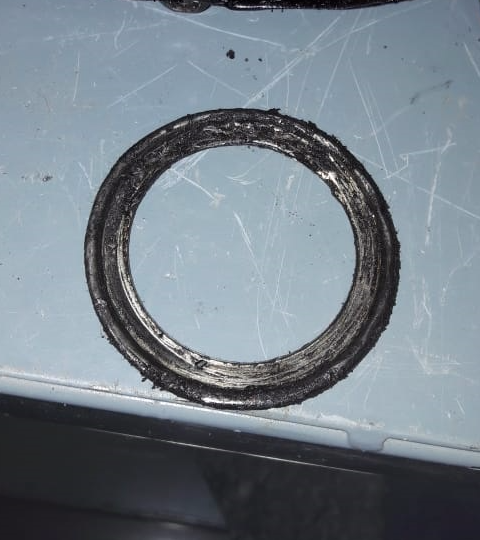
And here is what the separator did:
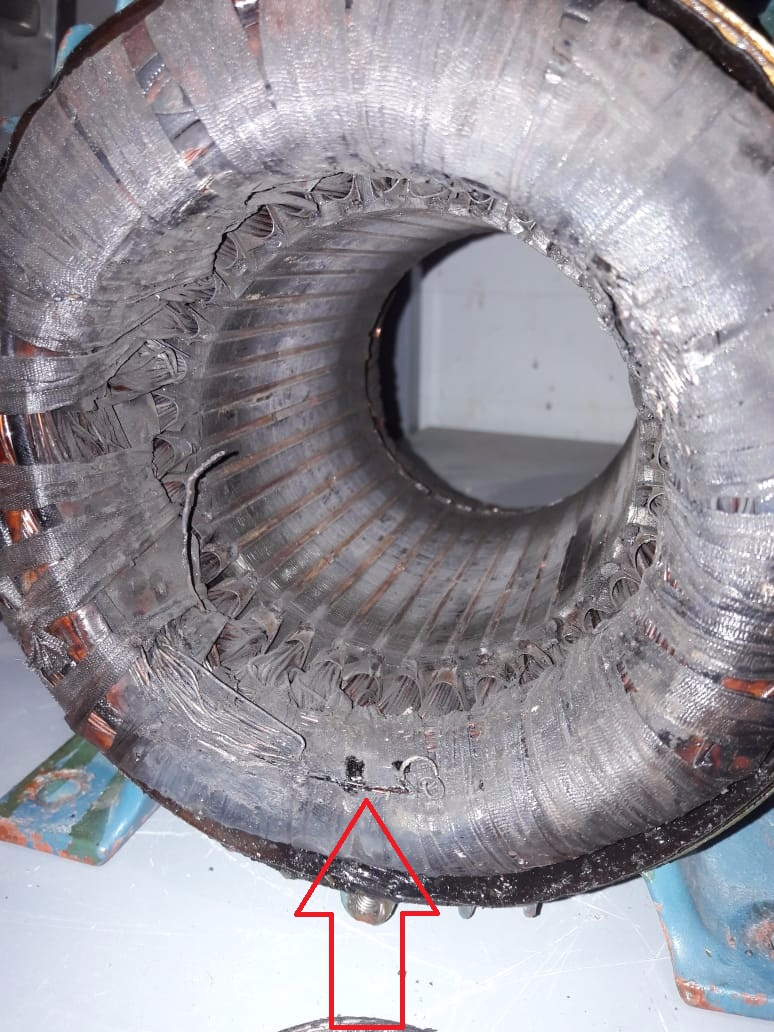
And I have a question. A protective washer is not available only on the side of the bearing shield. How did the separator get into the winding? On the winding side of the washer in place:
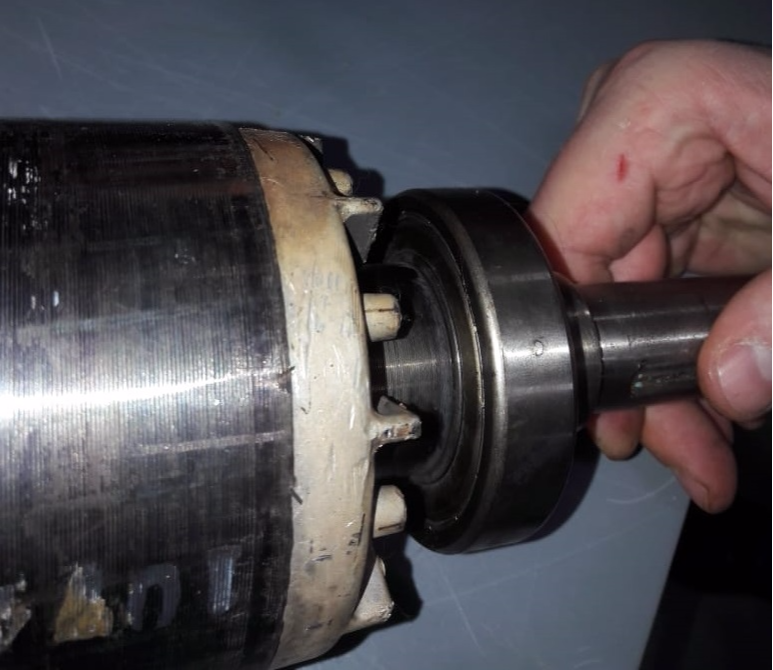
The answer of the electricians was a little struck - there the puck also flew out, we put it back in. There is a dumb question in my head - why?
We turn to bearing No. 1 (photo with a shield and without it):
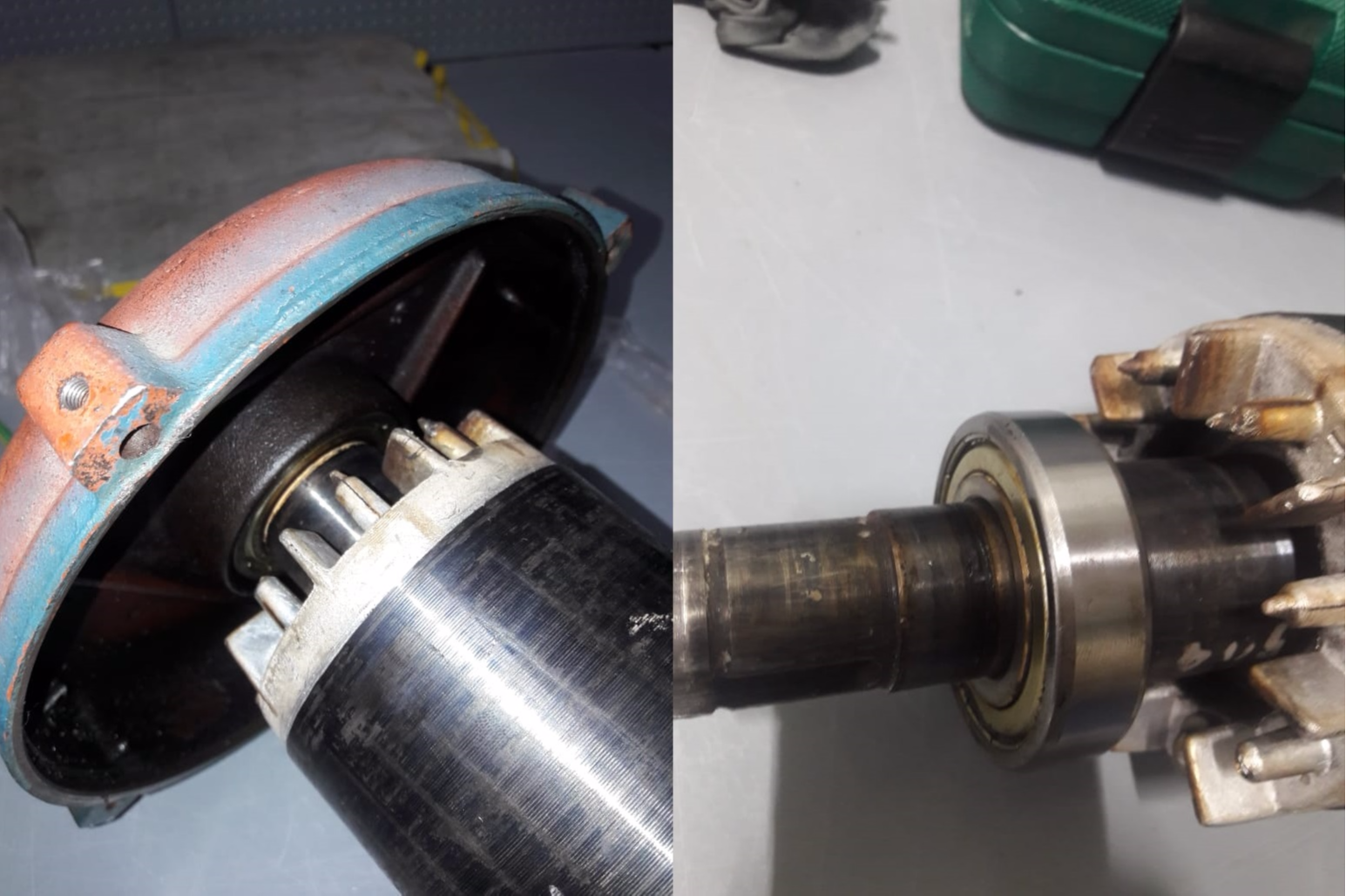
Traces of high temperatures are visible. The bearing is jammed. But the memory reminds me that when my colleague went to see the connection diagram, I showed him the deformed fan of the fan while rotating it.
Well, the cherry on the cake. On the side of bearing No. 1 between the stator winding and the housing, scraped parts of a collapsed separator are scraped. To the question of how it got there electricians could not answer.
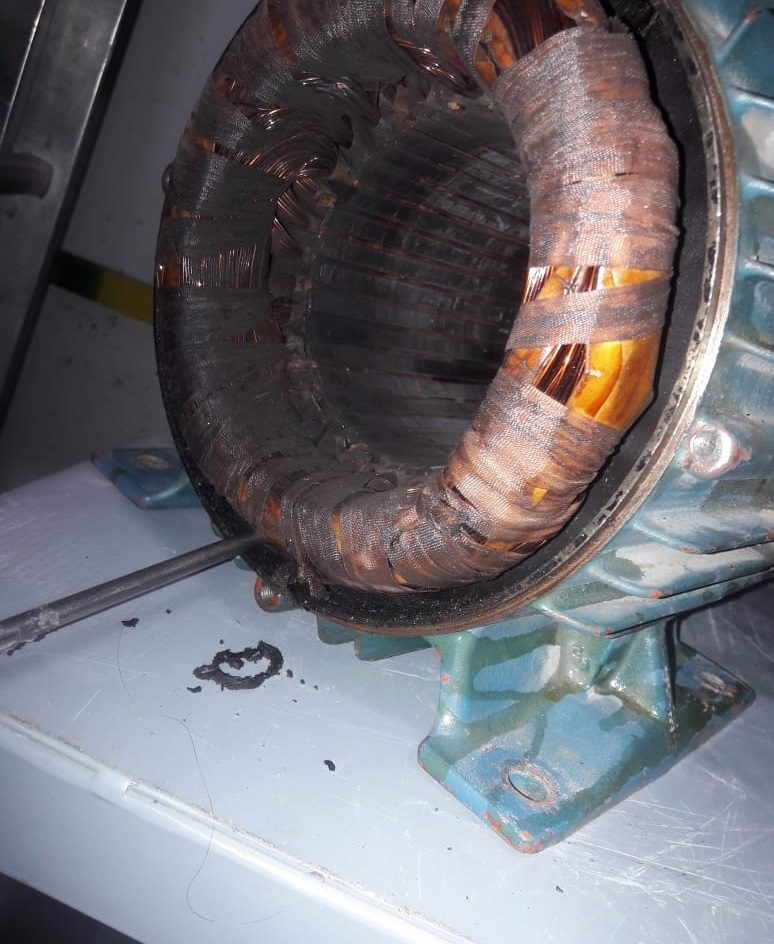
Either they deceive me, or something ...
Pleased with another. When communicating, electricians were not so categorically tuned about the wiring diagram. Of course, I did not open all the cards, but only advised me to go and see how the same electric motors are connected.
What can be summed up? Two options - overheating of the winding led to a short circuit, or to overheating of the bearings with a further history of damage to the stator winding by the separator (this is believed very weakly). Of course, first of all, we must admit our guilt. I had to immediately look for the cause of the rotation frequency of 45.1 Hz, and not to balance. Electricians also burst - when the same engine burns down twice, it is not good to continue rewinding the winding and changing bearings. Well, the wines of the manufacturer of electric motors WEG without a doubt. For me it was an interesting experience in finding the reasons for such a refusal and I am glad to share it with you.
Круто! Никогда с таким не сталкивался! А электрики порой хуже КИПовцев бывают) шулера.