Determination of a pump bearing defect by time signals
Recently we had a joyful event - our instrument park (QUARTZ, TOPAZ, AGAT-M) was replenished with the long-awaited Leonova Diamond from SPM Instrument. The instrument, coupled with the Condmaster Ruby software, enables complete analysis of time signals. A bearing defect on one of the pumps was not long in coming, and there was a reason to work with time signals.
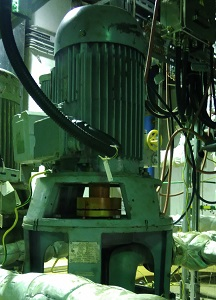
At one of the stages of the repairmen's struggle with defects in the coupling and a crooked shaft of the vertical pump HP45 / 54-2.0 (N = 30 kW, n = 3000 rpm) bearing No. 3 was replaced.
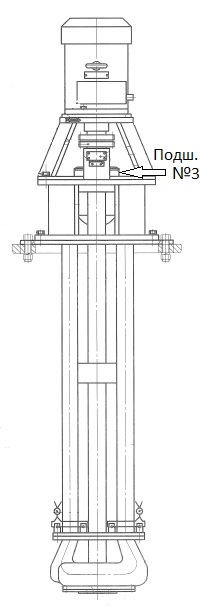
On my part, there were no complaints about the bearing, the replacement was carried out purely on the initiative of the repair personnel. During testing after repair and vibration measurement, the bearing No. 3 and the shaft in its area became very hot, there was a smell of burnt lithol. The pump was stopped urgently.
In the vibration envelope spectra, frequency components were identified, indicating a defect in bearing No. 3 (66410 according to the documentation), which is to be identified further.
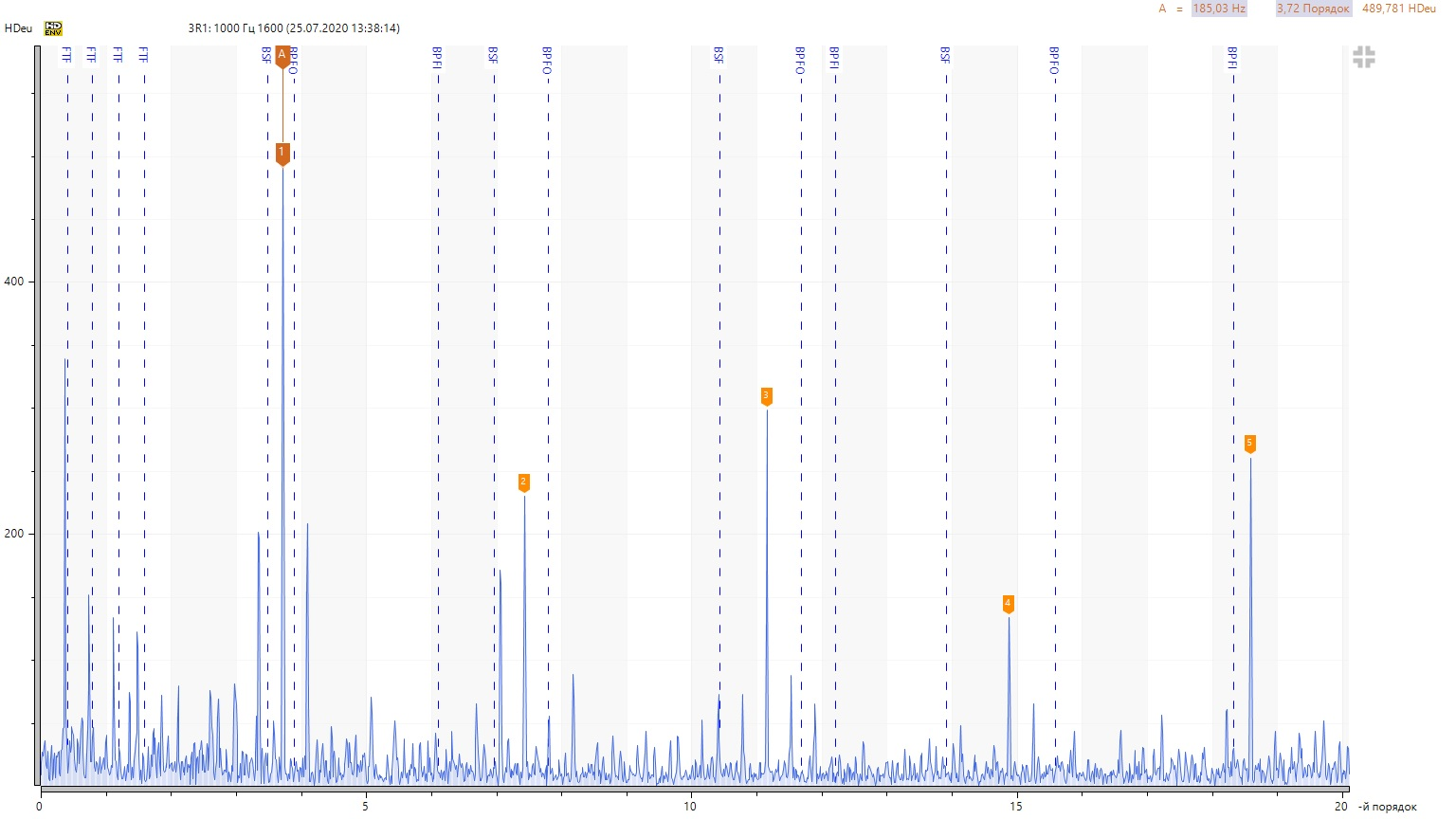
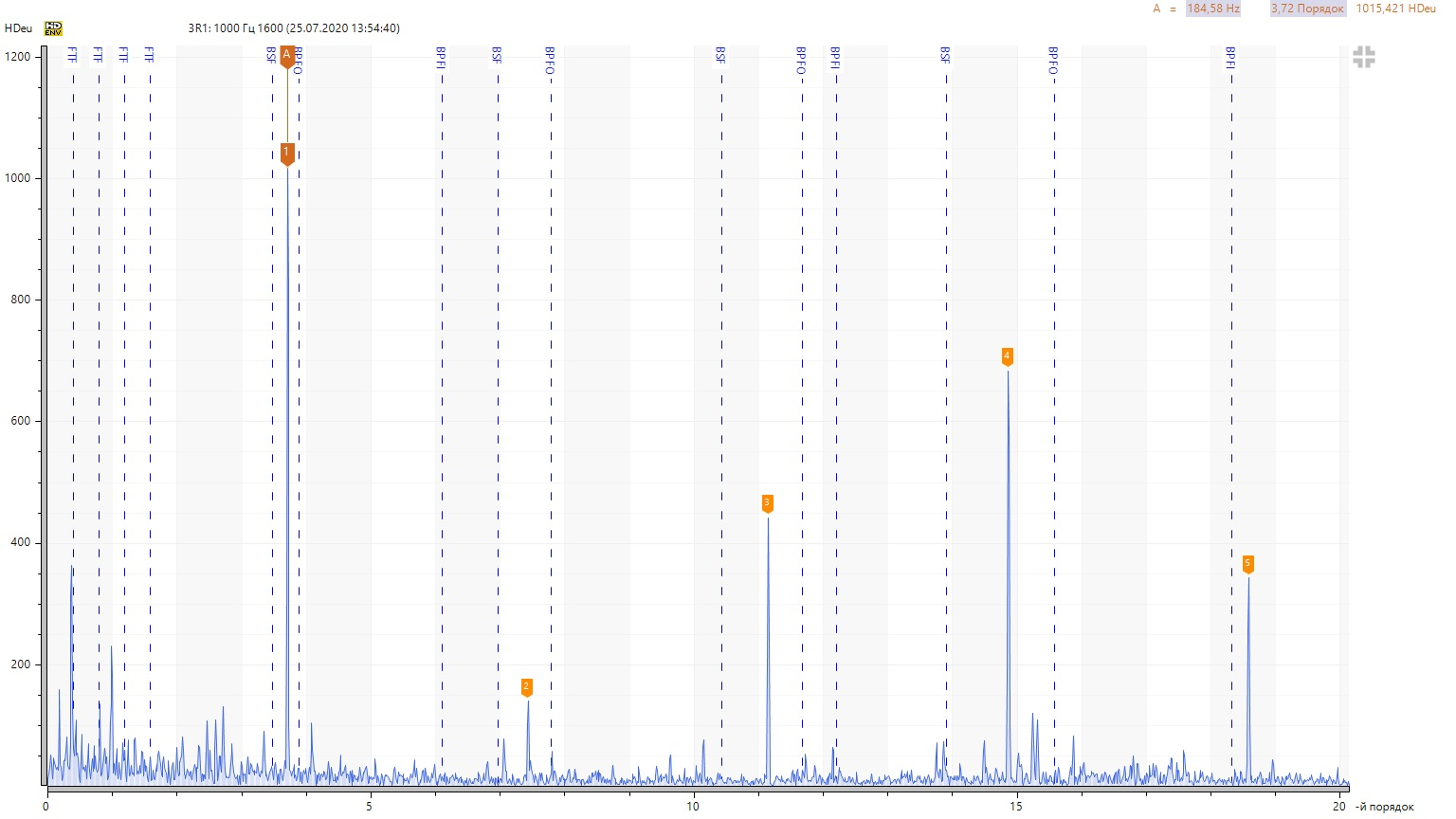
Frequencies of bearing defects (dashed lines) are calculated for the revolving speed taken from the spectrum. And if the separator frequency more or less coincides with the calculated one (FTF), then the defect at a frequency of 185 Hz and its harmonics is between the frequency of rolling of the rolling elements on the outer ring (BPFO) and double the frequency of rotation of the rolling elements around their own axis (BSF). Both possible defects can affect the rotation of the separator.
For clarity of the problem, let's take a look at the vibration acceleration spectra.
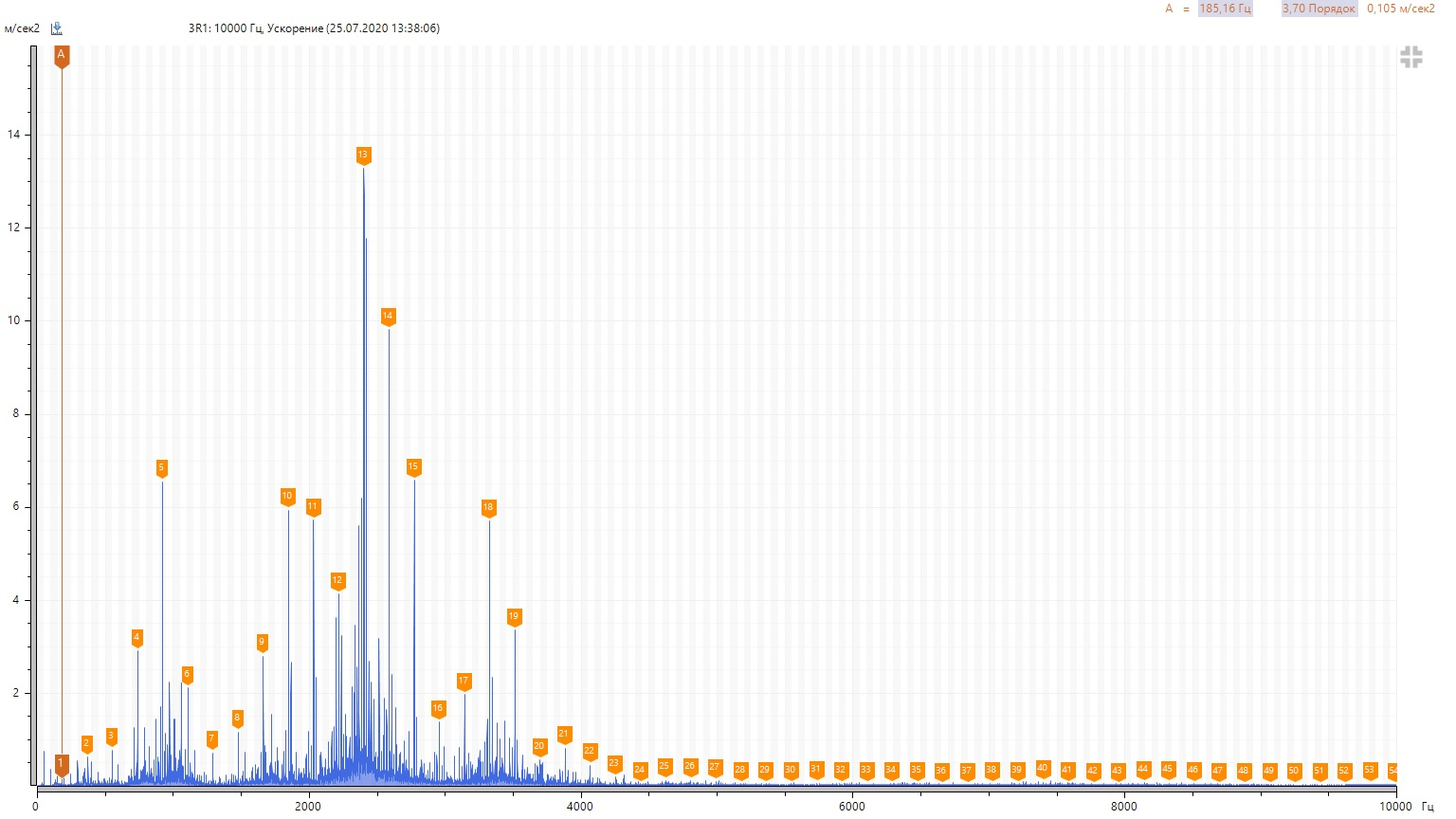
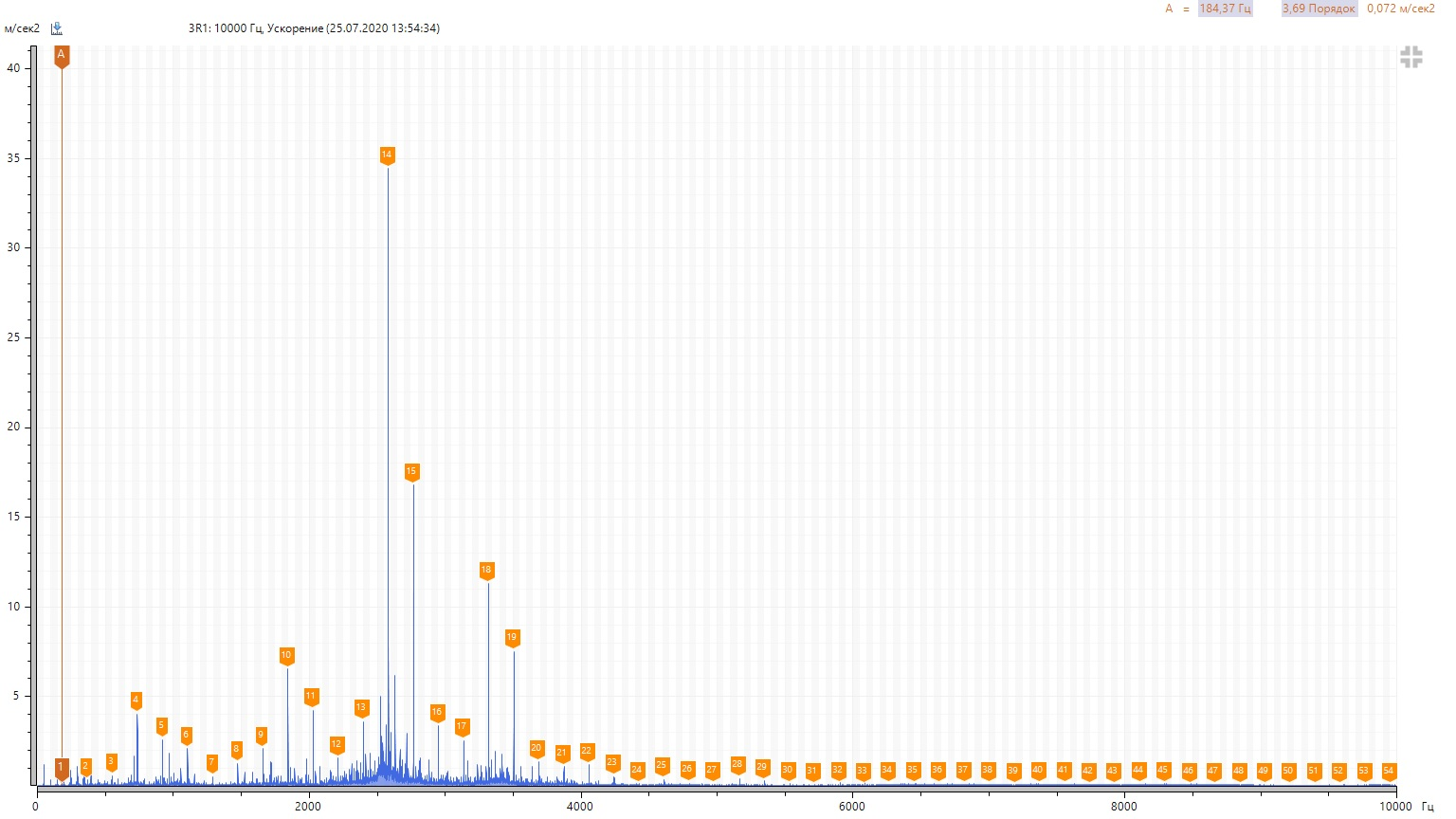
The spectra show that the main contribution to the vibration acceleration of the bearing is made by the harmonic series of the frequency component of 185 Hz. It is necessary to determine the defect more precisely. It can be assumed that since the separator frequencies are lower than the calculated FTF, it means that when the BSF and BPFO lines are shifted towards lower frequencies, we will practically fall by the BPFO line to the defect frequency. But let's look at the timing signals.
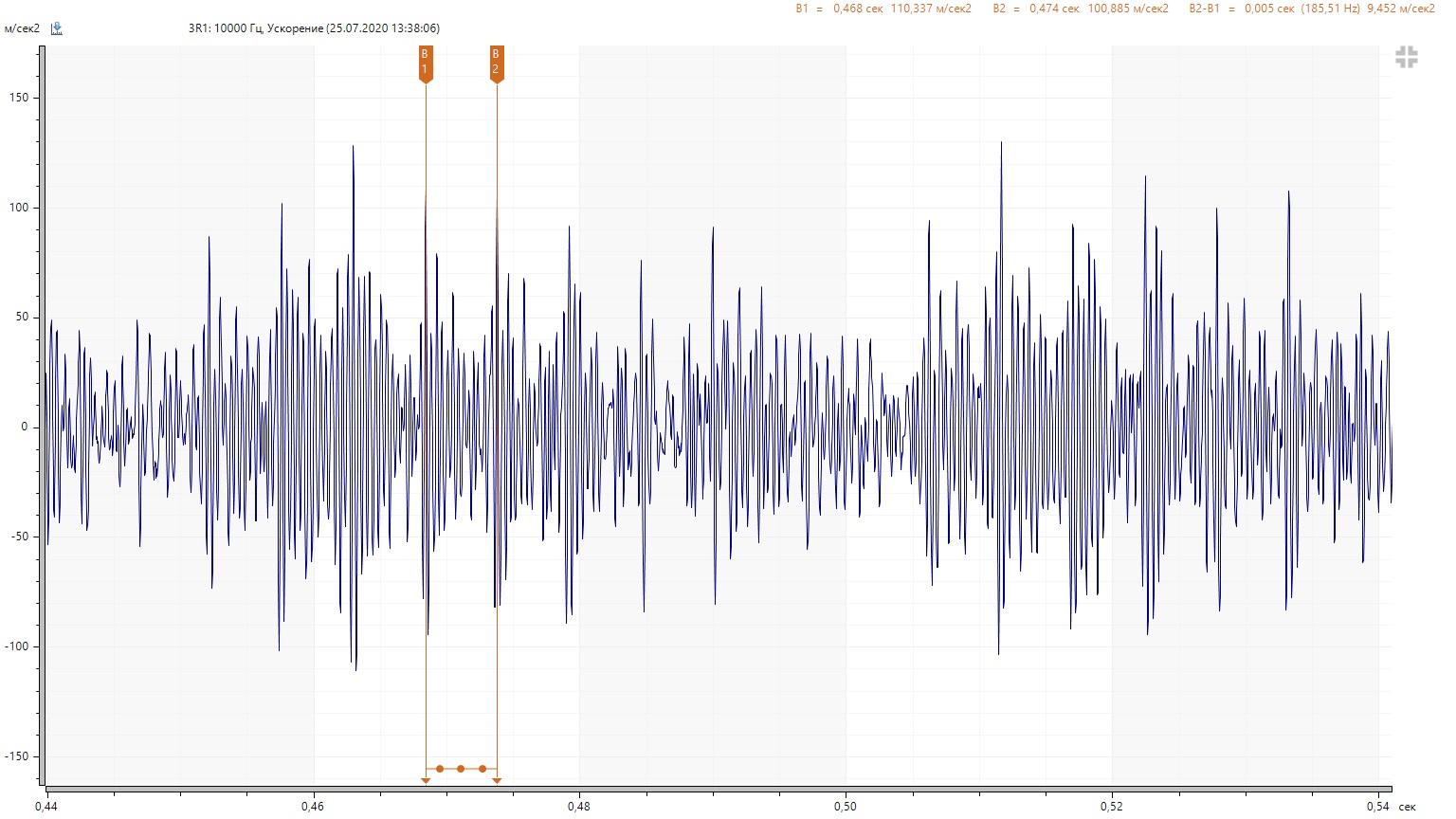
Impulses in the form of "fish" are characteristic of the defect of the outer ring. We know the number of balls in the bearing is 10. Can we dig deeper and determine the number of defective spots and their size?
The developers of Condmaster Ruby have included in the software an interesting tool for analyzing time signals - a round chart. They represent the translation of the time signal from the Cartesian coordinate system to the polar one. By default, the period (turnover) in the round-chart is the turnover frequency, but nothing prevents us from changing it at our discretion. Since we believe that we have defects on the outer ring, I suggest taking a look at the round diagram with a full revolution equal to the cage speed.
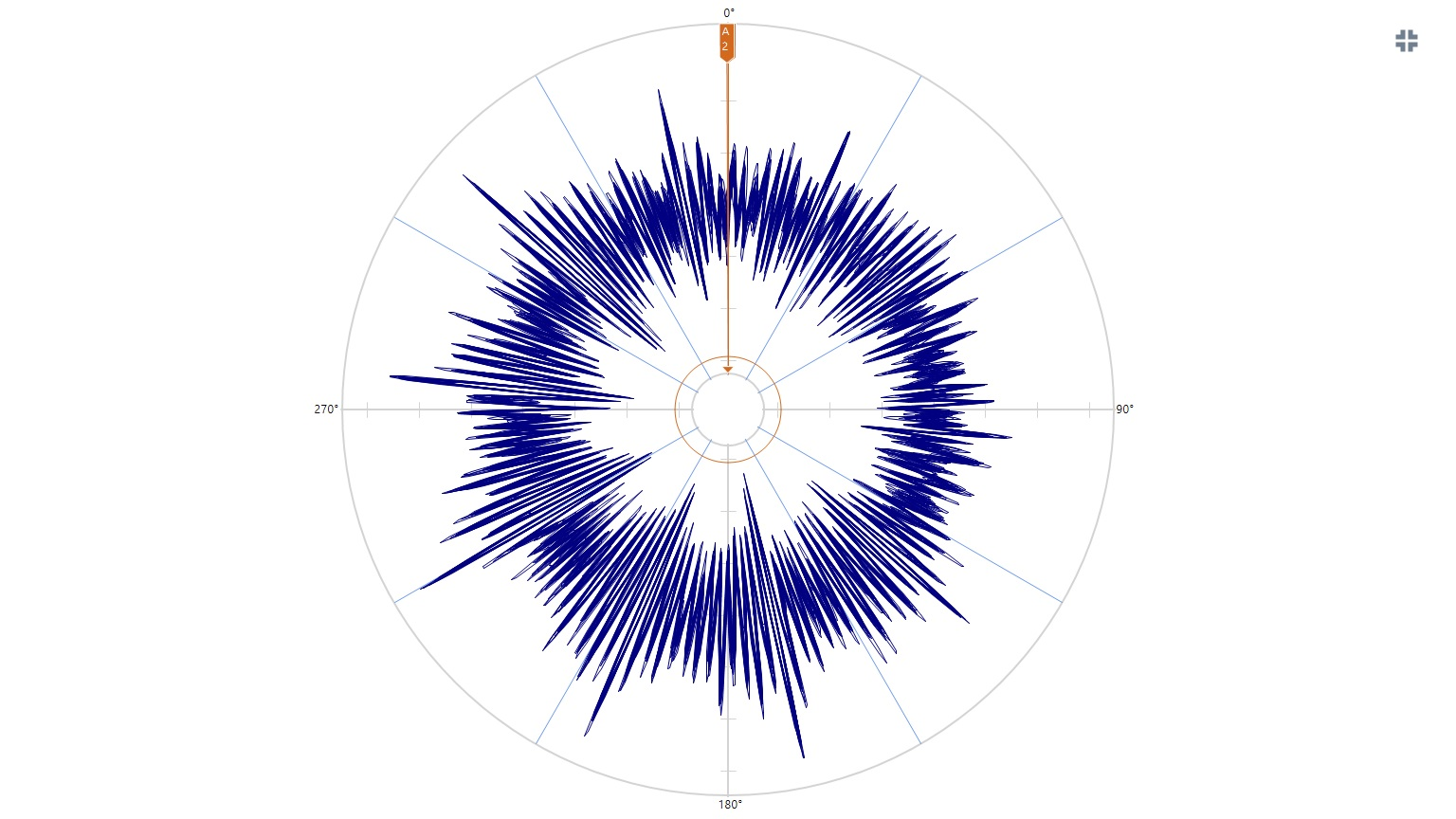
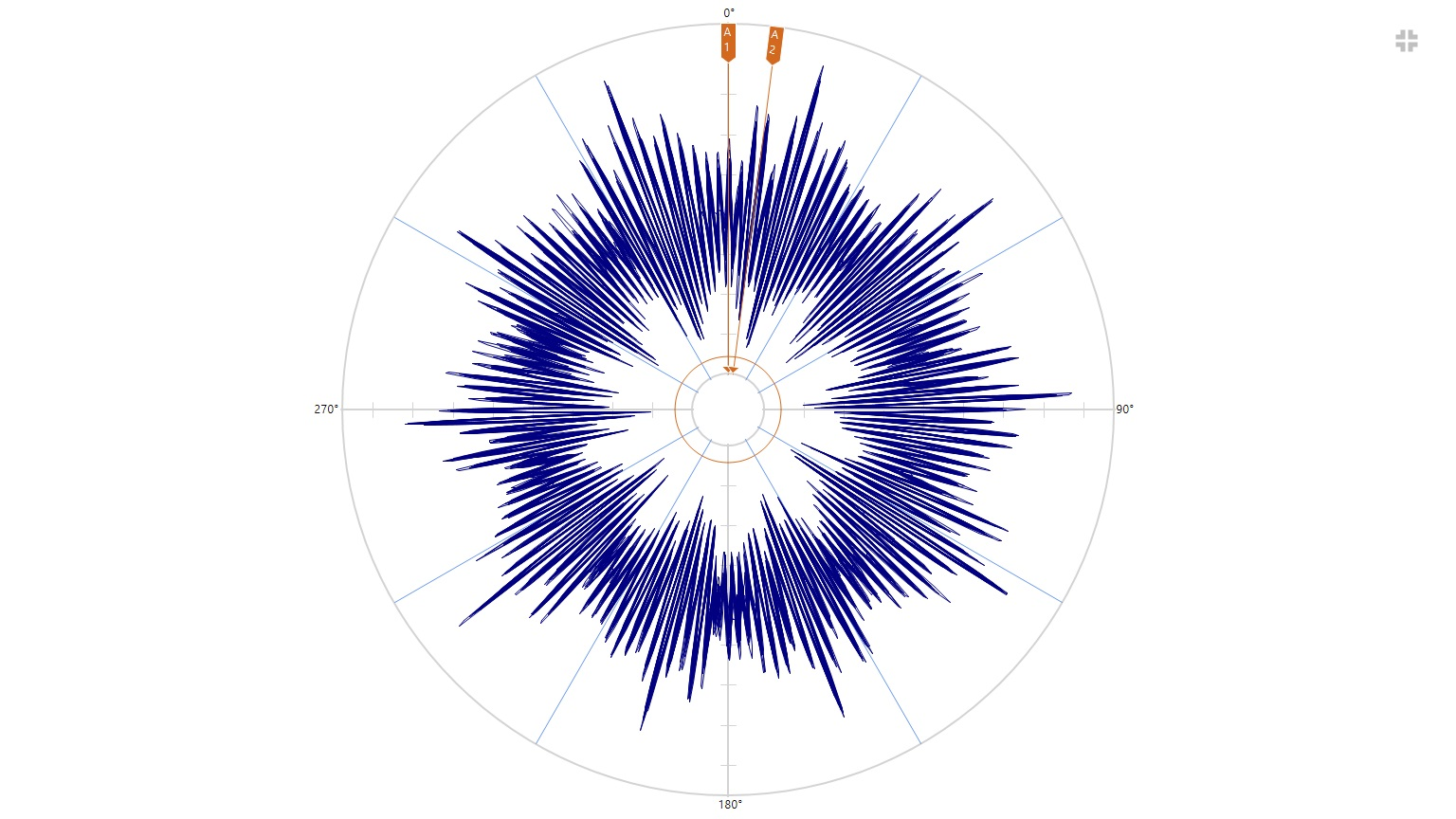
As you can see, 10 blows occur in one revolution of the separator. We have 10 rolling elements in the cage, respectively, we have only one defect on the outer ring. I propose to see what will happen if you do the same with the envelope signal.
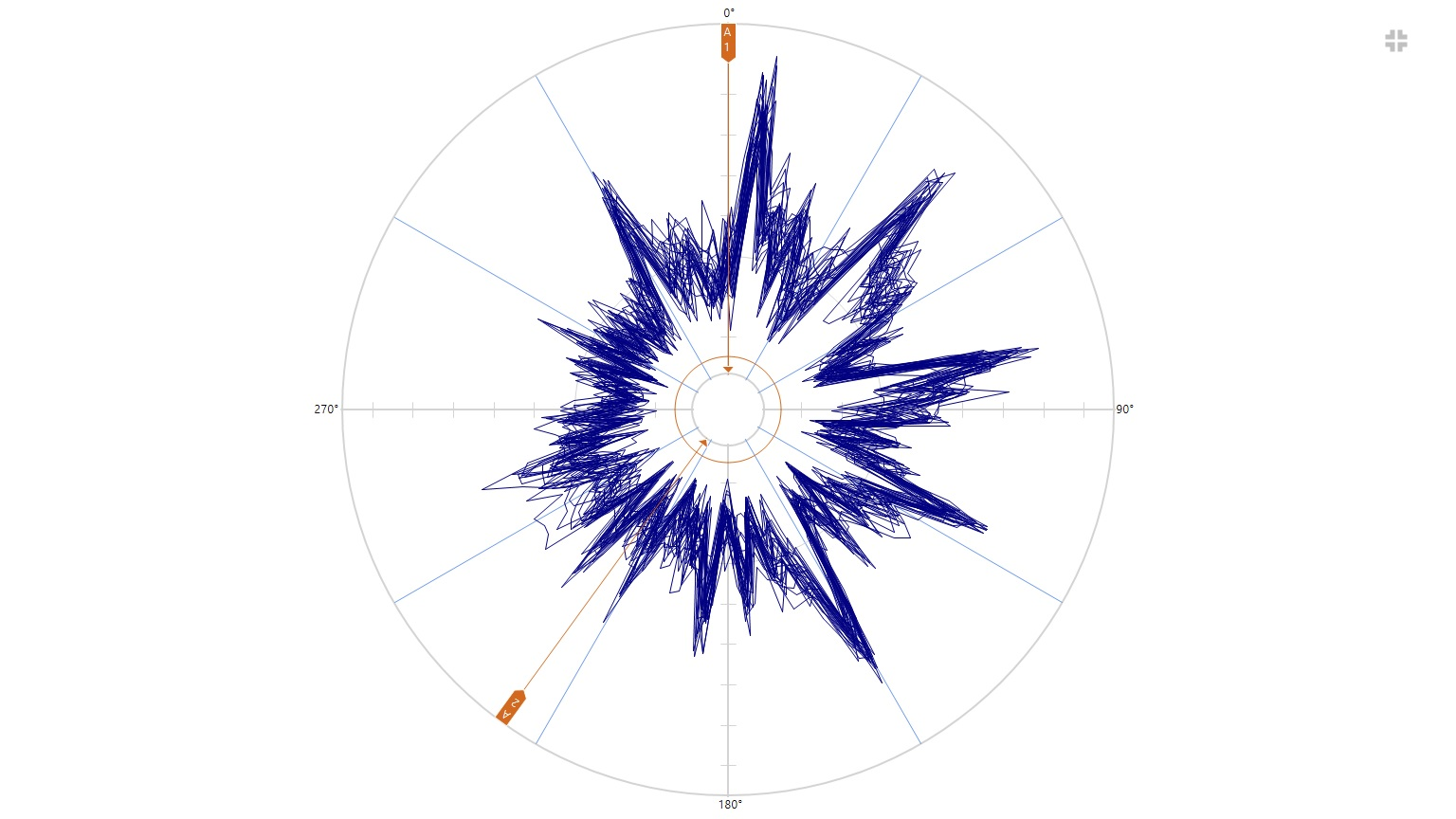
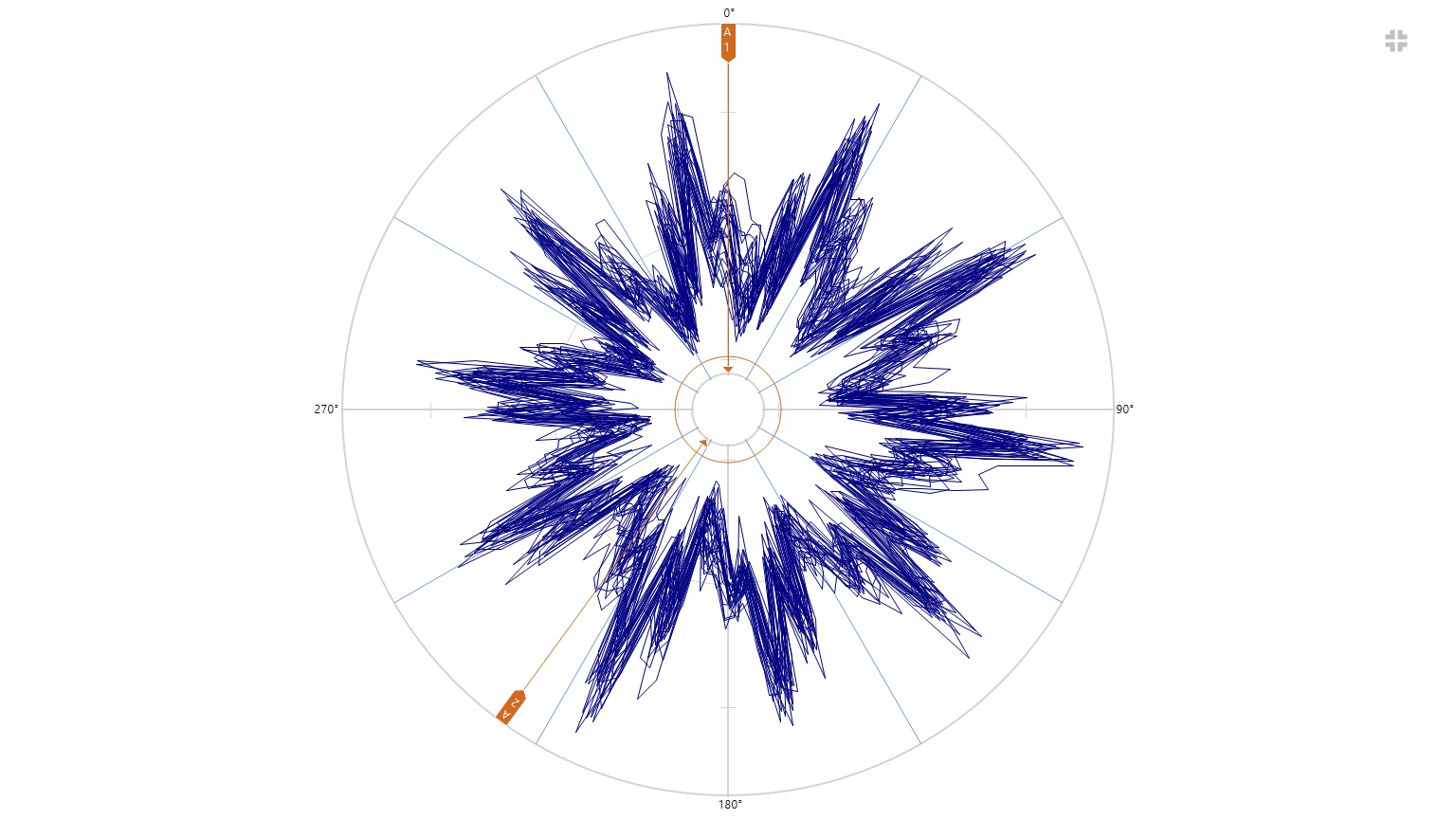
The defect is seen much more clearly along the envelope. Judging by the round diagrams, the defect occupies a sector of 20-25 degrees of the outer ring track.
According to the accelerations and the level of the envelope, a very strong developed defect can be assumed. But let's look at the spectra of vibration velocity and shock impulses.
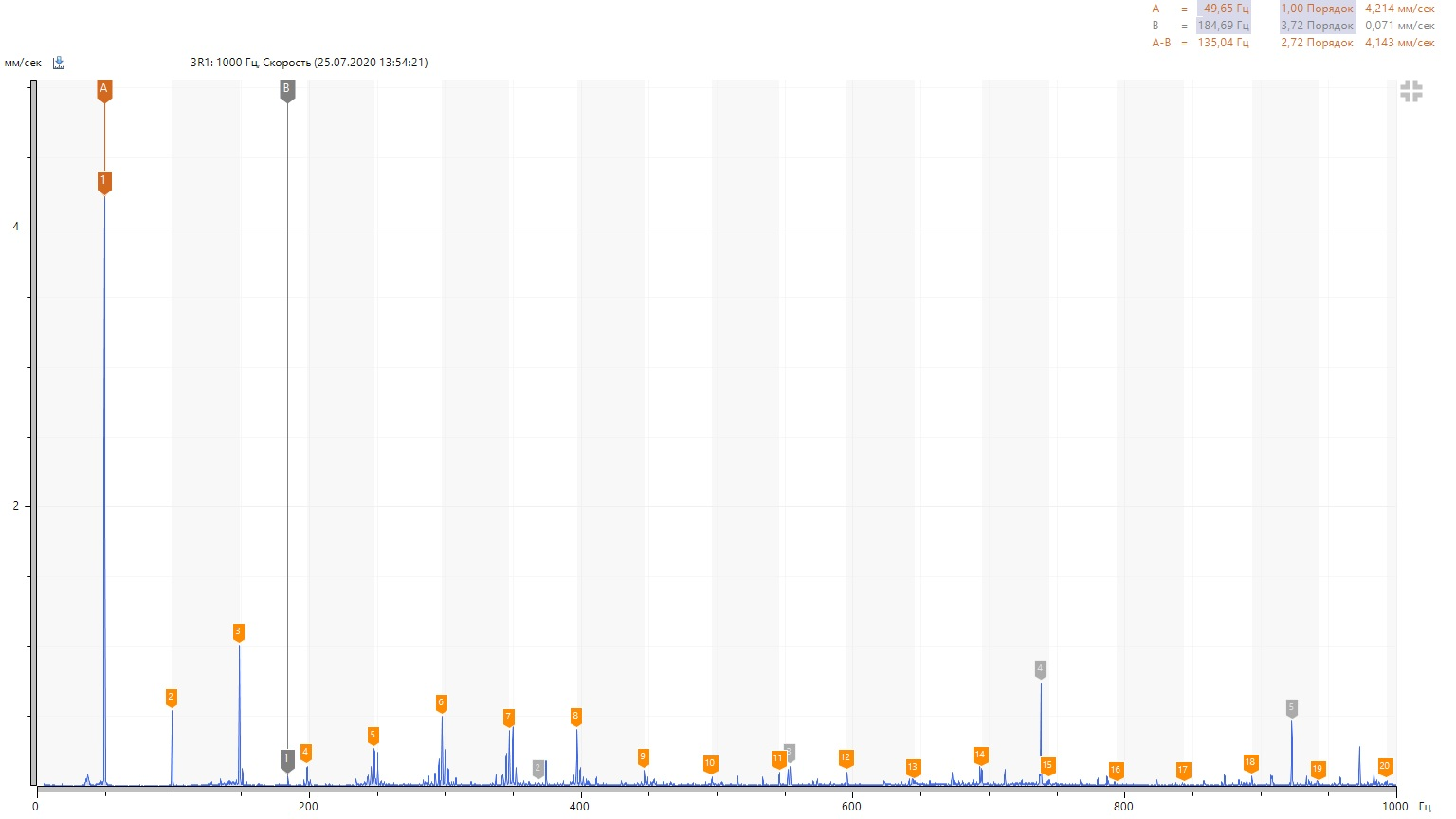
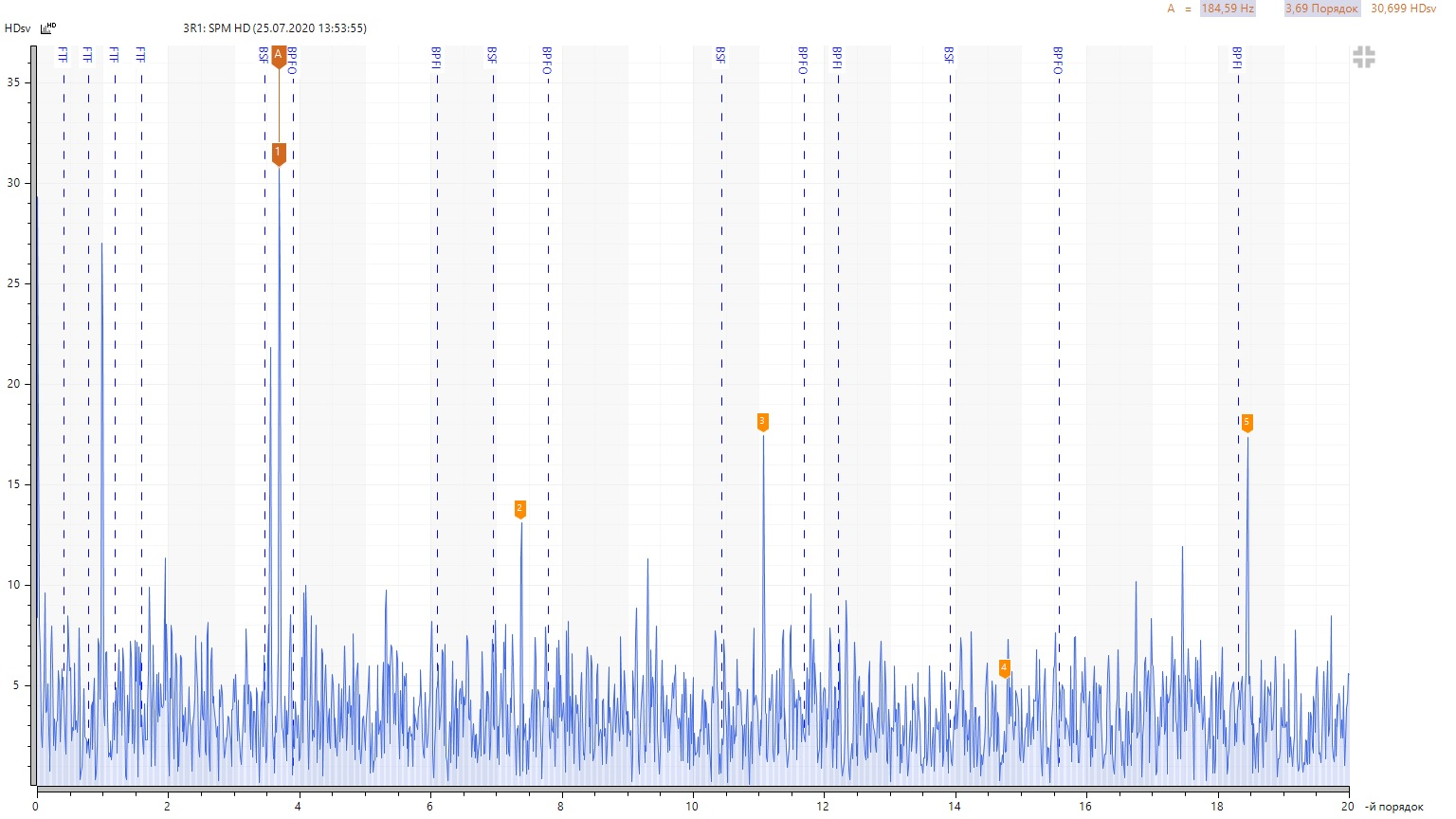
The spectrum of vibration velocity is dominated by the harmonics of the turnover frequency (cursor A) from other defects, the harmonics of the frequency of rolling of the rolling elements along the outer ring (cursor B) are small and there is no background rise around them. In the spectrum of shock pulses, although a defect in the outer ring is noticeable (cursor A), the pulses themselves are not large. That is, the defect is rather weak.
Finally, let us open the veil of the mystery of the defect. I rejected the bearing and, using further repair of the pump due to other defects, the repairmen replaced it. The bearing turned out to be 7410B (which is not so important, since it differs from 66410 only in a wider brass cage), was disassembled, rubbed and I encountered a defect on the outer ring, which I see for the first time in my practice.
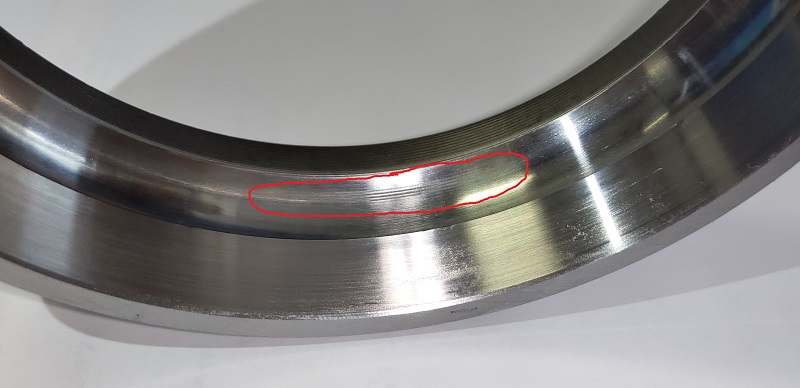
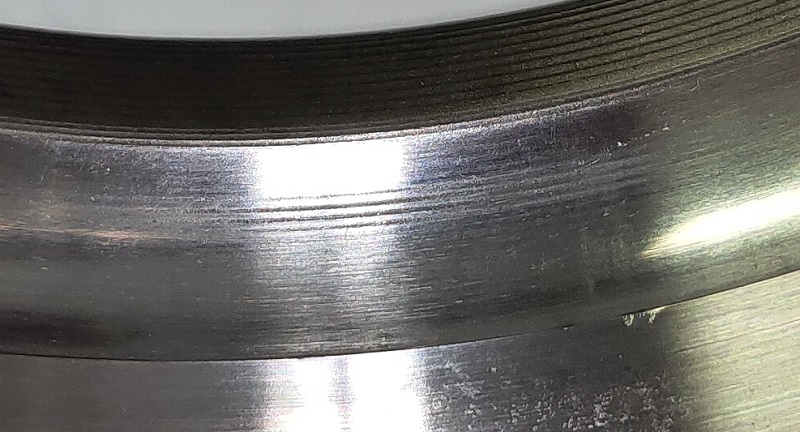
Examining the remaining parts of the bearing, a shell was found on one of the rolling elements.
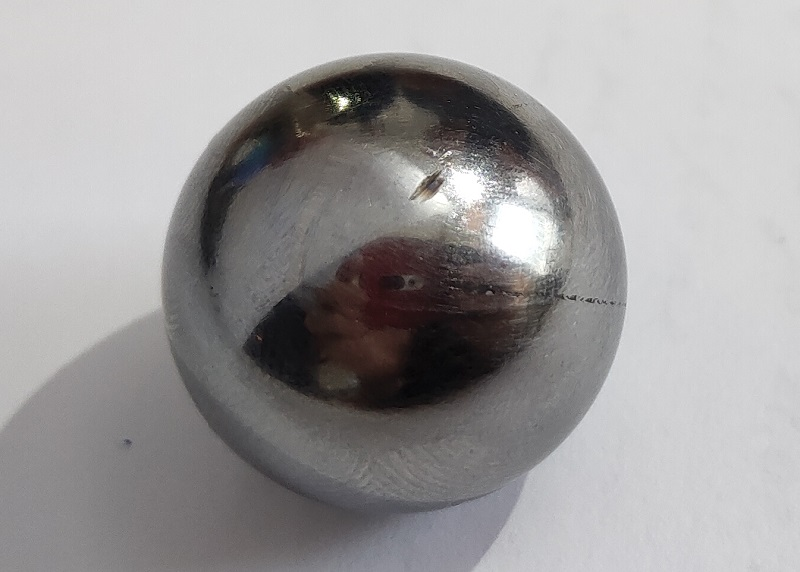
The outer ring has sufficiently deep notches parallel to each other and to the edges of the outer ring. The distance between them is the same. From this we can conclude that these are not scratches from solid inclusions in the bearing grease. If we plunge into the technology of manufacturing bearings, we find out that after turning the outer ring, the operation of polishing it follows. Apparently, the defect is traces from a turning tool. Either they chipped deeply, or they didn't polish this place on the track. In any case, this bearing is of very dubious quality.
High levels of acceleration and envelope, the clarity of the manifestation of such an insignificant defect, are associated with strong rolling of the outer ring by the rolling bodies due to the alignment and deflection of the shaft. The weakness of shock impulses is associated with the absence of shells and chips. The friction just changed greatly when the rolling bodies passed this section.