Vibrodiagnostics of the pump bearing D 2500-62-3
Посторонний шум, Дефекты подшипников, Вибродиагностика
In this article, we consider a practical example of the diagnosis of extraneous noise from a pump D 2500-62-3 (N = 500 kW, n = 750 rpm) from the side of bearing No. 4. We identify the defect and determine the root cause of its formation.
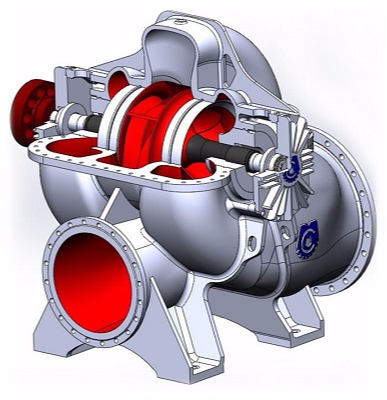
We have three such pumps - two in operation, one in reserve. During the next vibration control, one of them (let's call it pump No. 1) detected an extraneous noise from the side of bearing No. 4, strong enough to be distinguishable from the noise from the equipment around it.

RMS measurement data of vibration velocity in the range of 10-1000 Hz:
Norm 4.5 mm / s. As you can see, according to the parameters of the general level of vibration velocity, everything is fine. To determine the source of extraneous noise, we will analyze the spectra of vibration velocity and envelope spectra, compare with similar spectra on bearing No. 4 of pump No. 2. To do this, we need the calculated bearing frequencies. The task is complicated by the fact that in the documentation I could not find the brand of the bearing used. No problem, I open the drawings and see that the bearing is a double-row roller. According to the landing dimensions, I determine that it is possible to install a bearing 3620 or its foreign counterpart 22320 on this pump. I carry out the calculation of both bearings and compare them with the real frequency components in the spectra:
Rotor speed Fo, Гц | ||||
Fundemental train frequency Fс, Гц | ||||
Ball sping frequency Fтк, Гц | ||||
Ball passing frequency of outer race Fн, Гц | ||||
Ball passing frequency of inner race Fвн, Гц |
The table shows that the bearing 22320 is installed.
Let's move on to the vibration spectra:
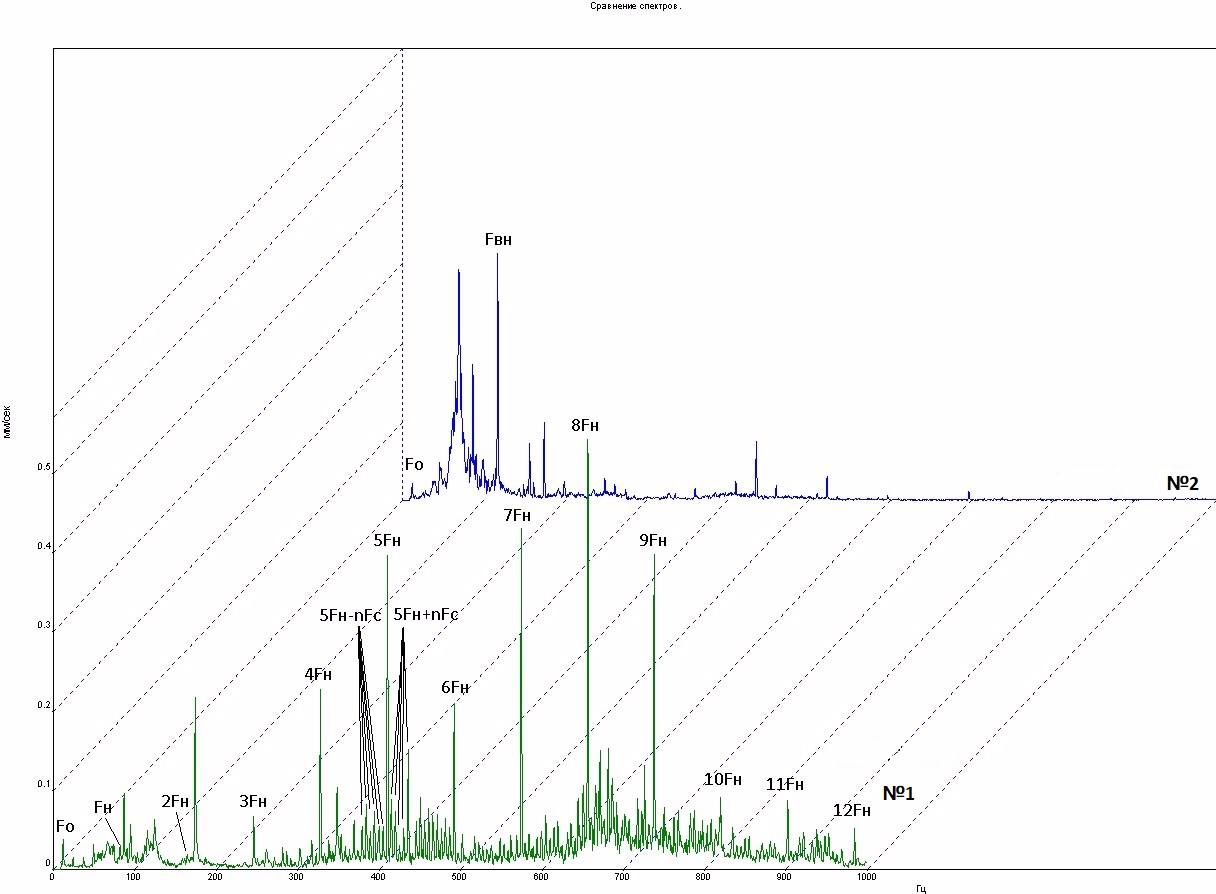
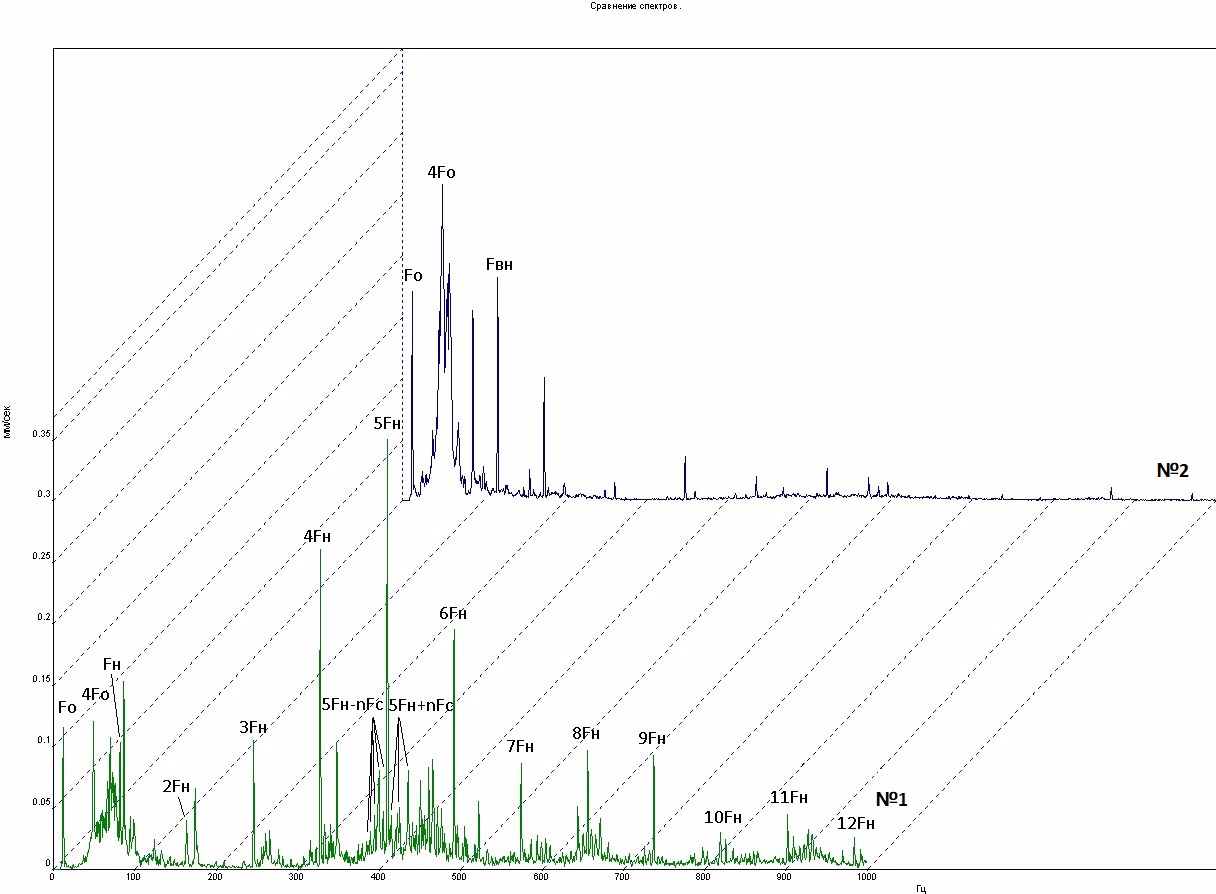
The presence of a large number of harmonics of the frequency of the outer ring Fн and such noisiness indicate developed defects on the outer ring of the bearing. Components ± nFc (where n is an integer) are characteristic for the separator to wedge in - its rotation is uneven.
Envelope spectra:
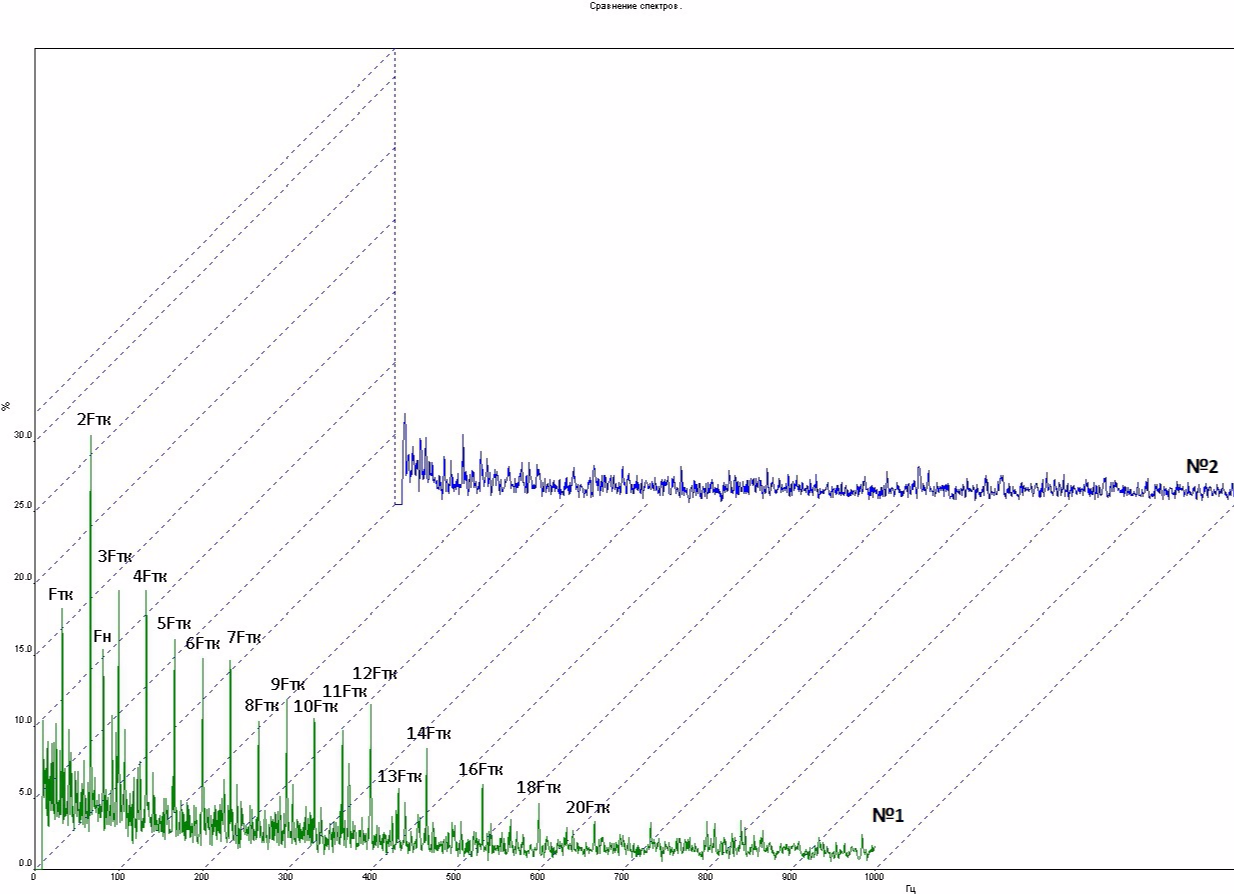
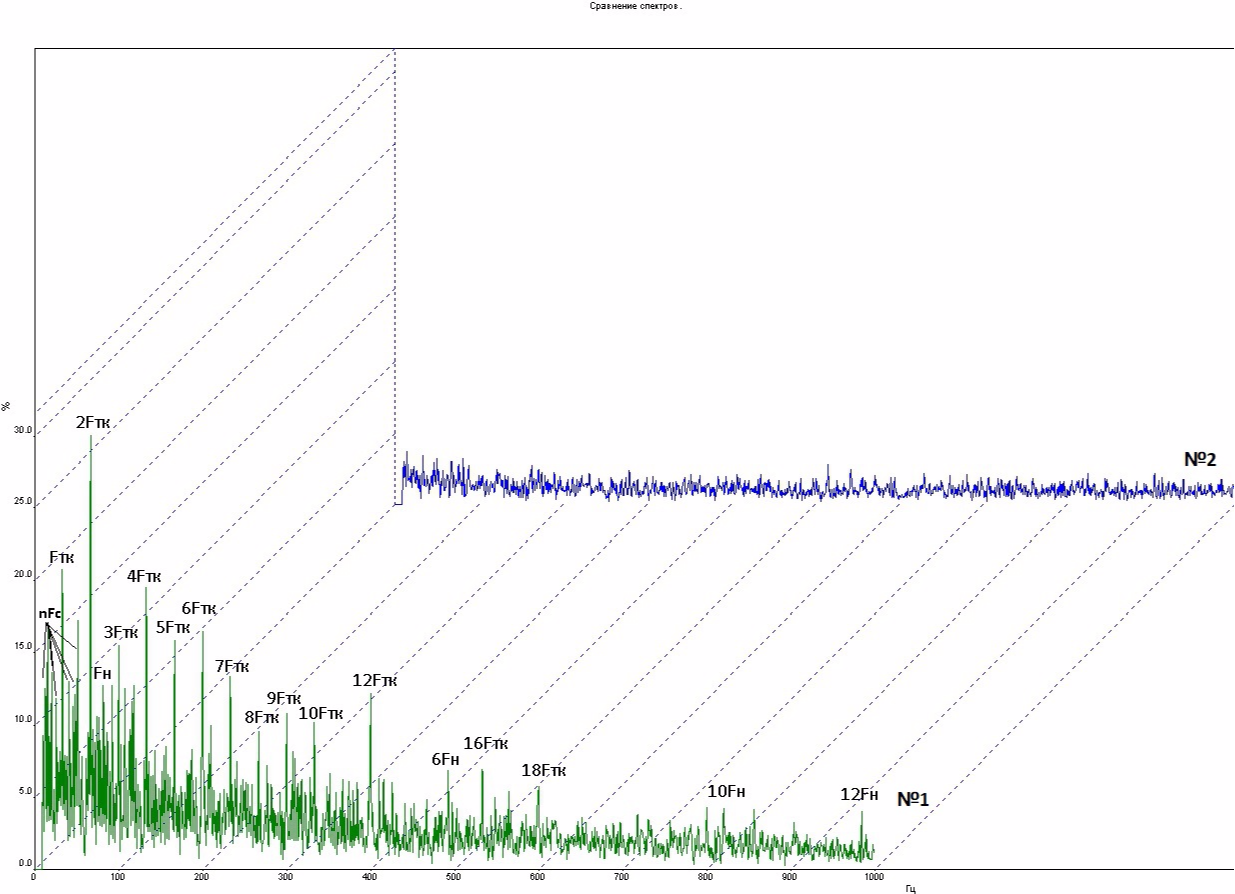
The presented envelope spectra complement the picture of the defect. Here defects on rolling elements (harmonics Fтк) are clearly expressed, which leads to uneven rotation of the separator (harmonics Fс).
To summarize, we have pronounced defects in the outer ring and rolling elements. From experience, this is most common when corrosion occurs inside a bearing after moisture has entered. I asked the driver a question: were there any strong leaks on the pump seal on the side of bearing No. 4? The answer is yes: there are often splashes in all directions, we often call repairmen to tighten seals.
As a result, he drew up a protocol in which he indicated that:
- the bearing 22320 is installed in the pump on the support No. 4;
- the bearing has developed defects in the outer ring and rolling elements;
- the likely cause of the bearing defect is corrosion due to leaks from the pump;
- it is necessary to track the development of the defect;
- during the next scheduled repair, replace bearing No. 4;
- provide the bearing to the diagnostic group to confirm the defect.
Management decided not to wait for the scheduled repair. Since there is no particular difficulty in replacing bearing No. 4, this work was soon completed. The repair staff washed, disassembled and provided me with a dismounted bearing (22320 SKF).
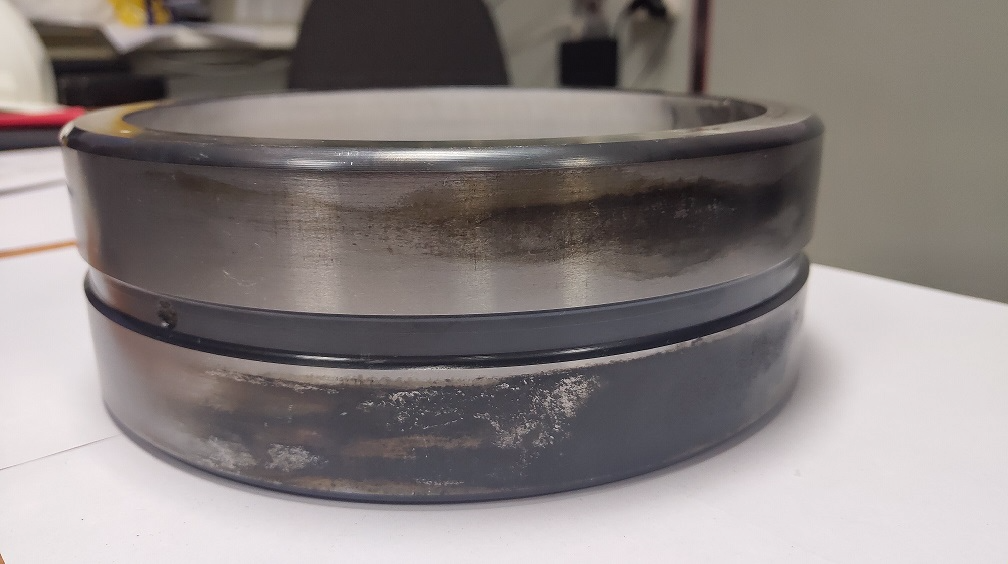
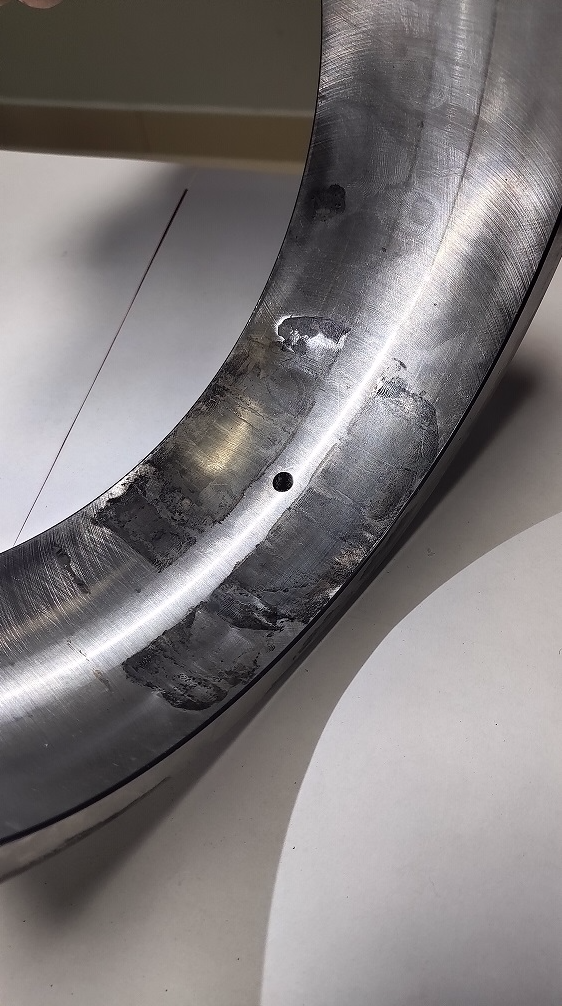
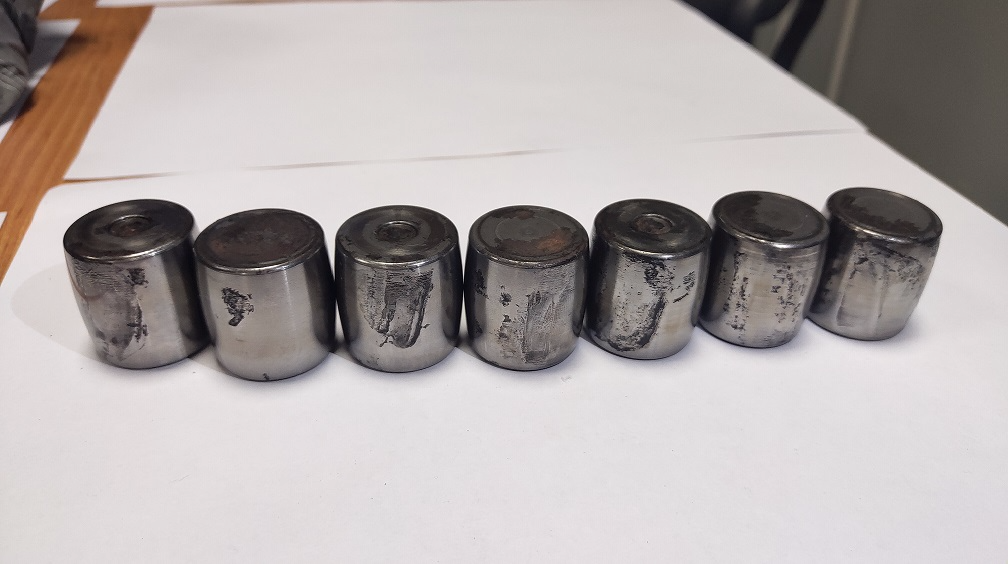
On examination, we see that the outer ring has undergone corrosion on only one side. Of the rollers, only 4 pairs were corroded (double row bearing). Correspondingly, the corrosion process occurred after ingress of moisture during standby of the pump. Defects and the root cause of their formation are fully confirmed. This story helped to draw attention to the consequences of a careless attitude to leaks in the pump seals, the repairmen promised during the scheduled repair to concentrate on the problems with the seals.
I’ll add from myself that I was glad of such a reaction of the management, the interested attitude of the repair personnel to this problem. This motivates to fulfill their duties not formally and, oddly enough, cheers up.