Diagnostics of thrust bearings for the ЦНА 100-50-5 pump
Вибродиагностика, Дефекты подшипников
And again the vibration diagnostics showed its effectiveness. Today is another example from the practice of detecting defects in bearings. We have a TsNA pump 100-50-5, engine power 22 kW, 3000 rpm. Vibrocontrol is carried out once a month. The vibration of the bearing support with the thrust bearings 46-309 installed in it usually did not exceed 2 mm / s. At the next vibration control, a colleague revealed an increase in vibration velocity to 4 mm / s, reported a possible bearing defect and recommended replenishment of the lubricant.
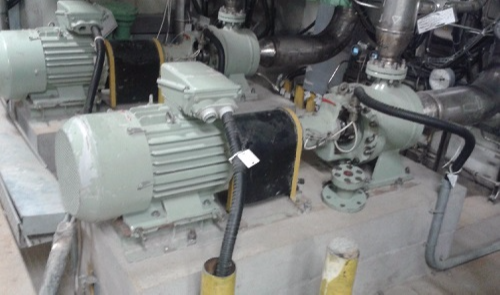
I was called for maintenance and diagnostics.
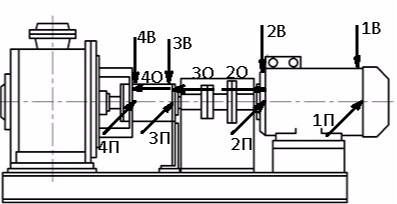
Measured vibration (RMS vibration velocity in the range of 10-1000 Hz):
Tolerance 4.5 mm / s. According to ISO and the requirements of factory documentation, everything is fine with us. When I fill the grease, but it does not go, squeezed out. Immediately in my head the question is, how did they do that before? Doesn’t it climb, and God bless her? I listen to the bearing through a metal tube - the standard sound of a defective bearing (like from a teaspoon in a mug with rapid stirring). There is a defect, to the analysis of the spectra a little later.
For the sake of interest, before switching to the standby pump, I measure vibration acceleration on the pump bearings (RMS vibration acceleration in the range of 100-10000 Hz):
And for comparison, vibration acceleration on the supports of a similar reserve defect-free pump (RMS vibration acceleration in the range of 100-10000 Hz):
This is an example of the sensitivity of vibration acceleration to bearing defects. Vibrodiagnostics specialists during vibration monitoring should evaluate not only the standardized parameters of vibration velocity, but also monitor vibration acceleration trends and compare with data from similar equipment.
Now we will analyze the spectra and calculate the bearing 46-309.
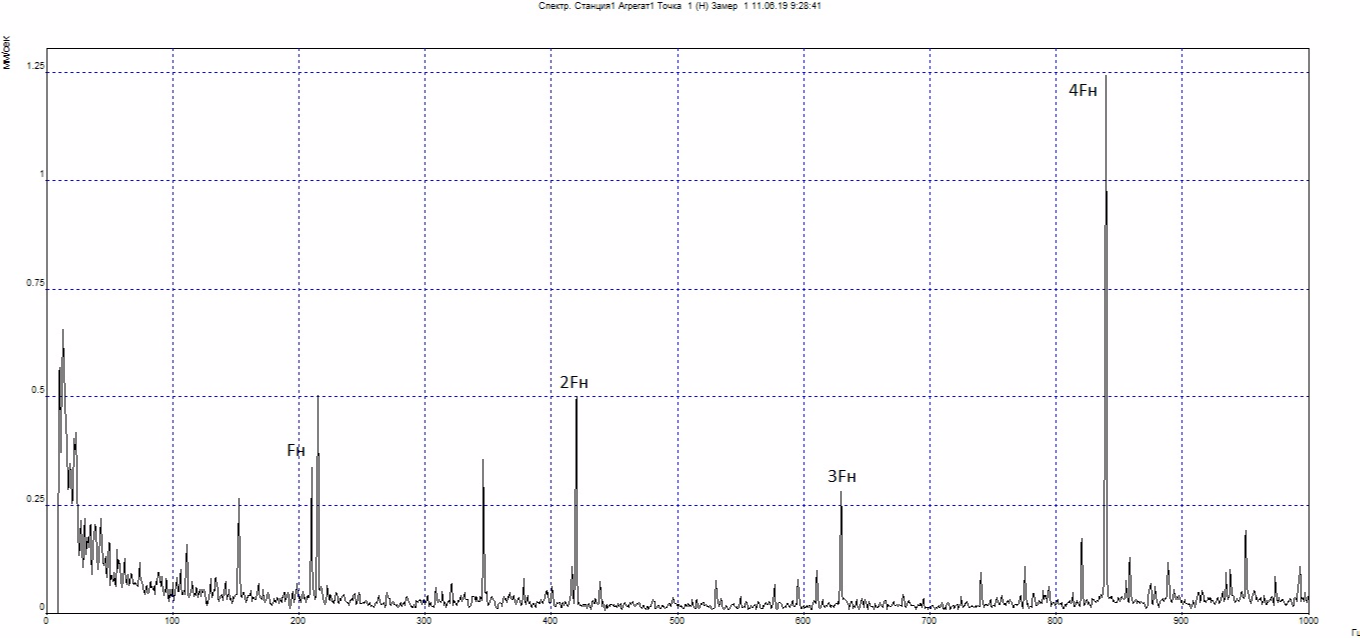
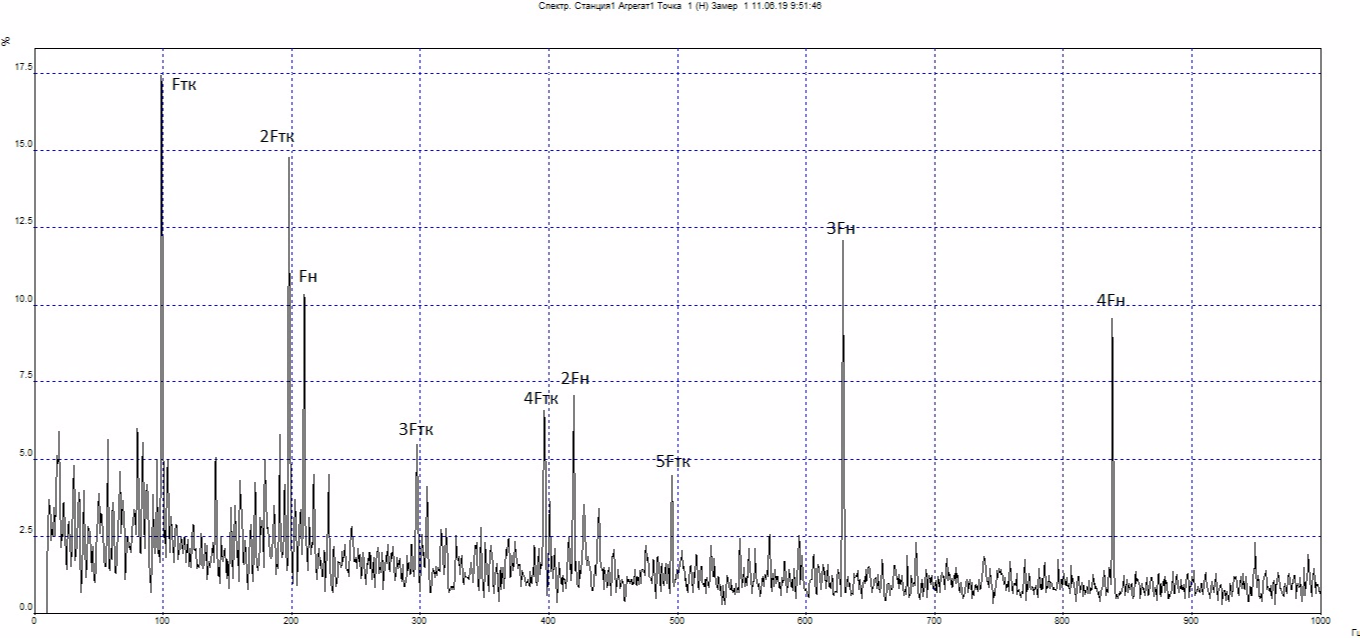
In the spectra, harmonics of the rolling body rolling frequency along the outer ring Fн = 209.38 Hz (210 Hz calculated) are observed, in the spectrum of the envelope of the vibration signal there are harmonics of the rolling body rotation frequency Fтк = 98.75 Hz (97.8 Hz calculated). It can be concluded that there are defects on the track of the outer ring and damage to the rolling elements. Since bearing frequencies are pronounced in the direct spectrum of vibration velocity, defects are developed. I recommend the conclusion of the pump for repair to replace bearings bearings №3.
After removal, as usual, I proceed to study the dismantled bearings. The first thing that catches your eye is a grease of almost black color, very thick. When the cages rotate relative to each other, the rolling bodies practically do not rotate. When rolling one of the bearings on a flat surface, a slight crunch is heard, and the presence of defects is felt by hand. We disassemble the bearing.
Defects on the outer ring:
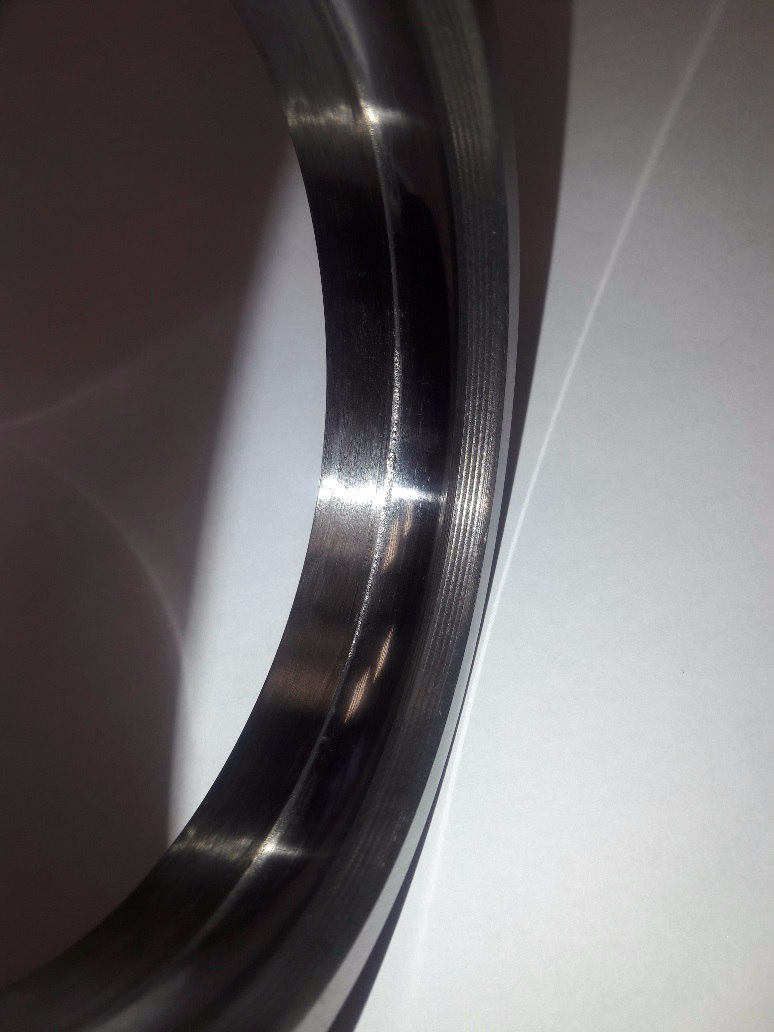
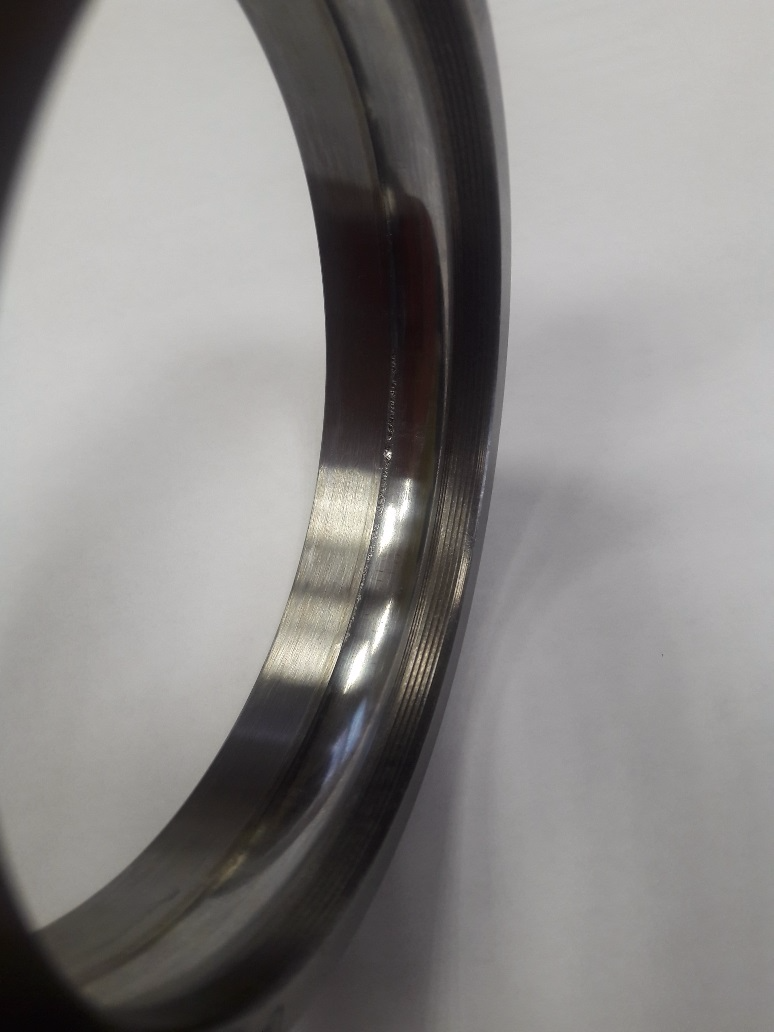
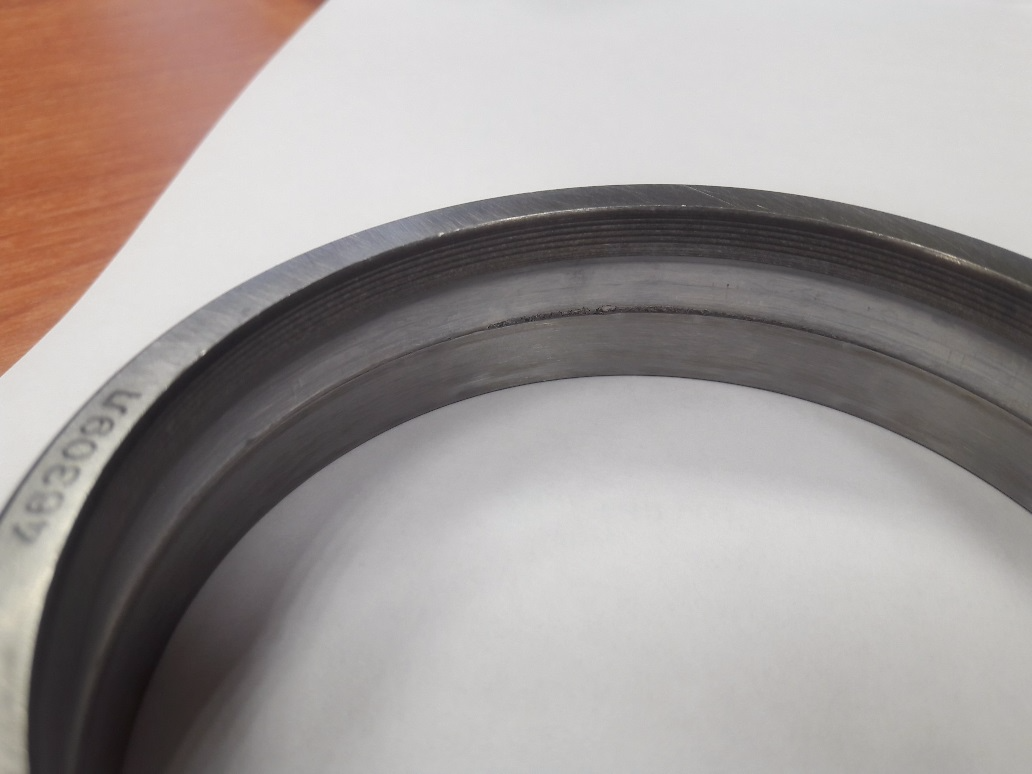
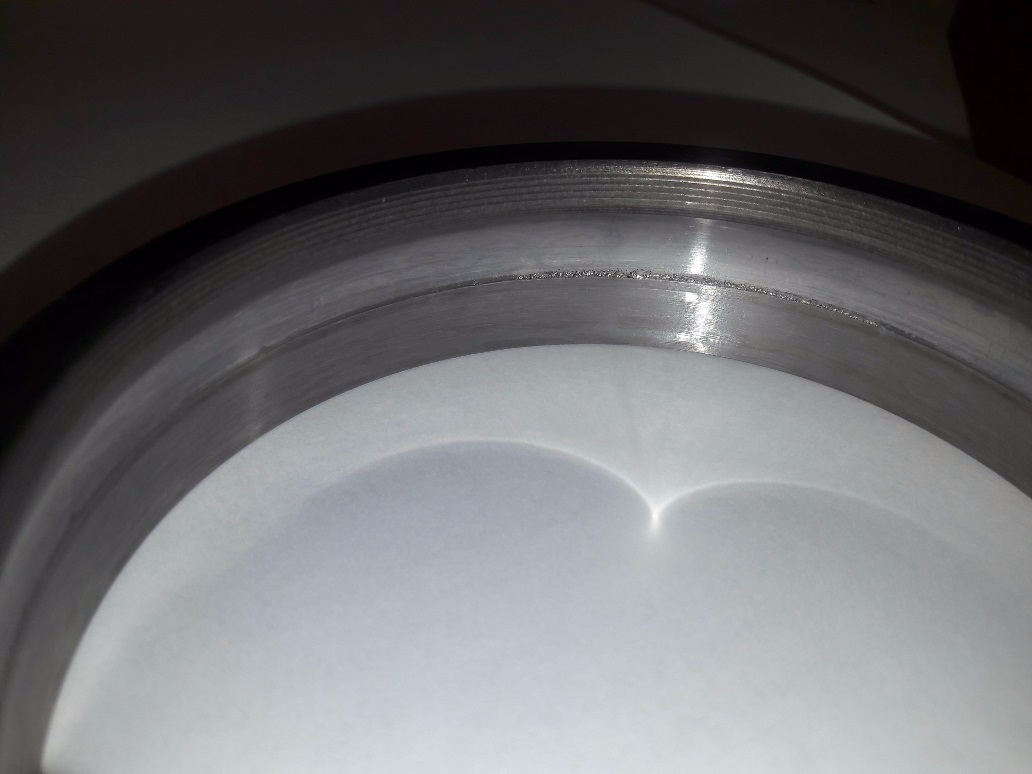
Defects of rolling elements:
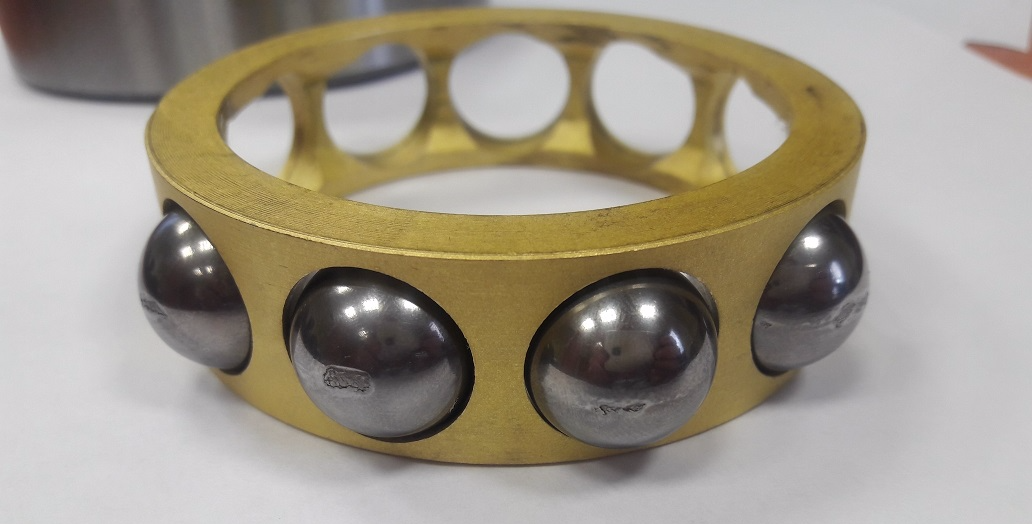
Damage to the outer ring is similar to long chipped edges of the track and is possibly a factory defect (a question about the quality of steel). Chips on rolling bodies are most likely caused by the presence of defects in the outer ring.
When rolling in on a flat surface, the second bearing had no visible defects, but just in case, it was also disassembled. On each ball around the perimeter, risks are barely visible to the eye. There are also similar risks on the inner ring track:
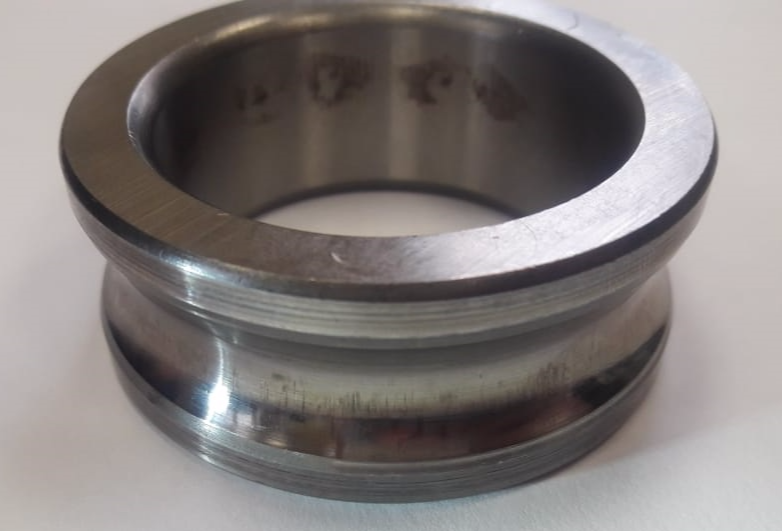
After replacing the bearings, the vibration on the pump was (RMS vibration velocity in the range of 10-1000 Hz):
The problem is timely identified, localized and resolved.